08
Portfolio
Officina 3
Intro
Reducción y normalización de los plazos de entrega en un entorno muy variable mediante la introducción de un priorizador

Industria
Producción y transformación de accesorios de alta costura
Oficina
Padova, Italia
Para Officina 3 -empresa especializada en la producción y elaboración de parches y etiquetas para alta costura, confección, calzado y marroquinería-, la variable tiempo es crucial.
La ausencia de una organización estructurada ralentizaba los procesos -en particular los de muestreo y creación de prototipos, caracterizados por una gran variabilidad de solicitudes-, lo que dificultaba el cumplimiento de los plazos y la garantía de plazos de entrega seguros .
Para mejorar la eficacia operativa de la empresa, iniciamos un proceso de reorganización basado en metodologías lean. Un análisis en profundidad identificó importantes ineficiencias, entre ellas una gestión de prioridades poco clara, que estaba provocando ralentizaciones en el flujo de producción. De ahí la necesidad de implantar un sistema pull que permitiera trabajar sólo sobre la demanda real, evitando pérdidas de tiempo y recursos. Al mismo tiempo, se estandarizaron los pasos operativos más críticos -gracias también a la introducción de un sistema de priorización- para garantizar una mayor calidad y reducir los imprevistos .
De este modo, Officina 3 ha reducido y estabilizado los plazos de entrega de muestras y prototipos, mejorando la gestión de las solicitudes y la puntualidad de las entregas. Ahora, la empresa puede ofrecer a las marcas de alta costura un servicio más fiable y eficaz, reforzando su papel de socio estratégico en un sector en el que la rapidez y la precisión son cruciales.
Resultados obtenidos
0
0
plazo de entrega(desde el inicio de la producción hasta el envío)
Filippo Fiorin
Gestión general: compras, subcontratación y logística - Officina 3
Giacomo Fiorin
Dirección General: Comercial, Desarrollo y Producción - Officina 3
Martina Fior
Jefe de producción - Officina 3
Stefano Cesarotto
Planificación de la producción - Officina 3
Alessio Accardo
Jefe de muestreo - Officina 3
¿Quiere mejorar el rendimiento de su empresa?
Historia
empresa
2001
Officina 3 se fundó en 2001 como empresa italiana especializada en la producción y transformación de accesorios para la industria de la moda, incluida la confección, el calzado y la marroquinería.
Hoy
Fundada hace casi veinte años, la empresa ofrece una gama de productos que incluye parches, etiquetas, cintas, accesorios y paneles para bolsos, accesorios y empeines de calzado. Todos los productos se diseñan, desarrollan y fabrican íntegramente en Italia, lo que permite un control total de cada fase del proceso de producción, desde la creación de prototipos hasta la producción final.
Empleados (2023)
0Facturación (2023)
0EBITDA (2023)
0
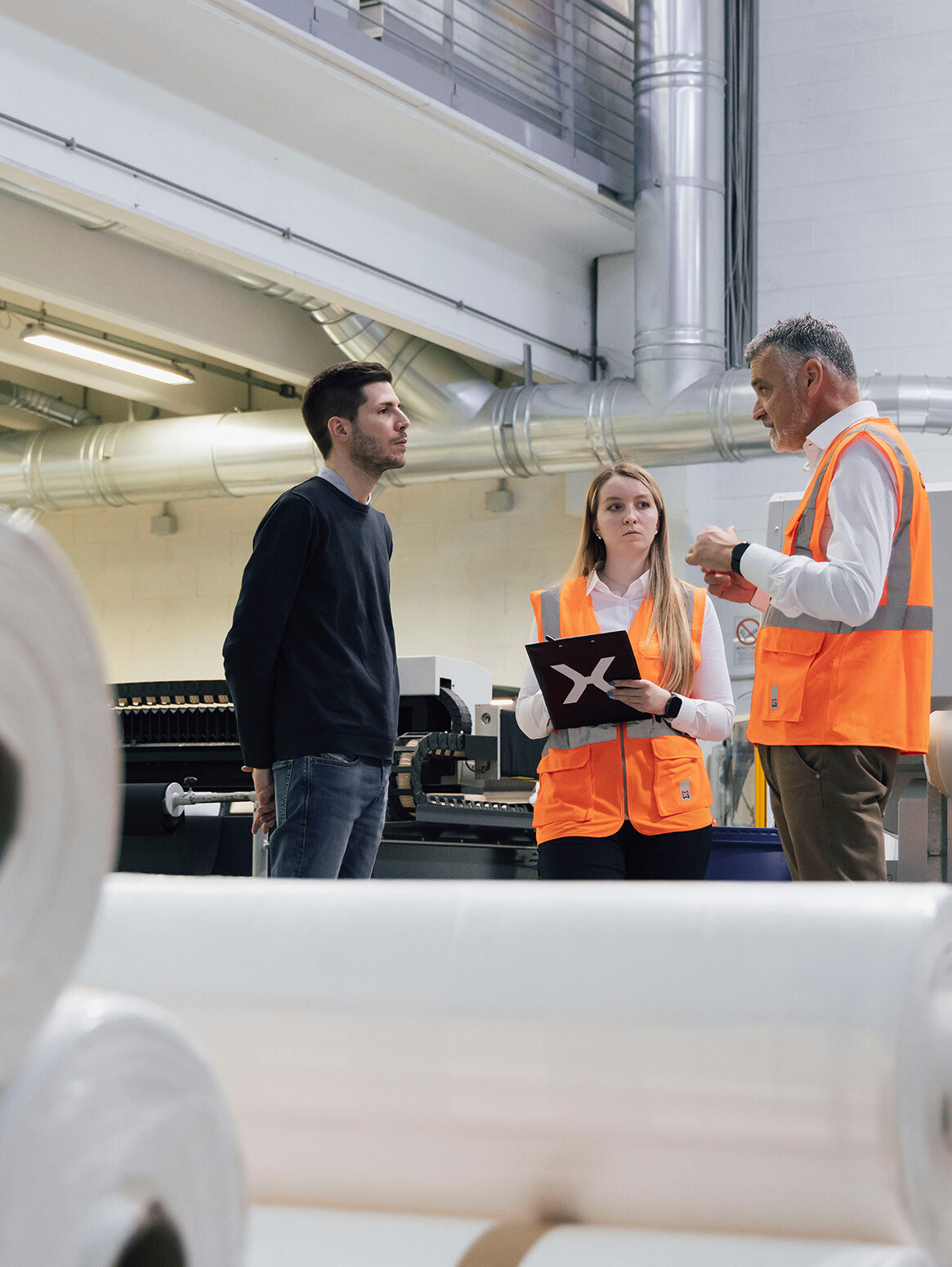
El reto del Officina 3
El reto de Officina 3 consistía en gestionar una demanda compleja -caracterizada por una amplia gama de productos y volúmenes discontinuos- dentro de un proceso de producción compuesto por numerosas fases de transformación con una gran variabilidad, reduciendo los plazos de entrega para responder con mayor prontitud a las exigencias del mercado.
El punto de partida
La transformación del primer macroproceso: la entrega
2020
Año de inicio de la colaboración
con auxiell
Fin
Con Officina 3 emprendimos inicialmente un proyecto sobre el macroproceso de entrega, que comprende la producción, la cadena de suministro y la gestión de pedidos.
Tras trabajar en la racionalización de los procesos de Entrega con el equipo de Officina 3, nos embarcamos en un proyecto sobre el macroproceso de Desarrollo, que incluye el desarrollo de nuevos productos y su modificación.
Tras trabajar en la racionalización de los procesos de Delivery y Development con el equipo de Officina 3, nos embarcamos en un proyecto sobre el macroproceso de Despliegue, que incluye la traducción de estrategias en actividades coordinadas.
SCAN
Lean Gap Analysis® en el Delivery
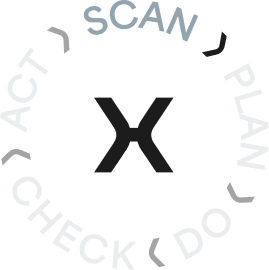
En un sector como el de la moda, en el que los productos tienen un ciclo de vida corto y están fuertemente ligados a las temporadas y colecciones del momento, la rapidez es un factor crítico de éxito. Cumplir un plazo de entrega concreto y garantizar la producción de los volúmenes requeridos marca la diferencia a la hora de conseguir pedidos de las principales marcas del sector.
Para analizar el estado actual de los procesos, el equipo de auxiell-Officina 3 emprendió el Lean Gap Analysis® del proceso de producción, centrándose en el análisis y el rediseño de las distintas fases de procesamiento, como el corte, el corte por láser, el grabado HP (alta precisión) y el grabado, el grabado HF (alta frecuencia), el grabado plano/continuo, la serigrafía, el laminado, el troquelado, el calandrado, el laminado, el bordado, la inyección y la microinyección.
Lean Gap Analysis
Fase indispensable para medir y analizar los procesos actuales y definir las diferencias entre el estado actual y el deseado. En esta primera fase se toma una "instantánea" del estado actual de los procesos en términos de cuantificación de residuos, identificación de posibles problemas y oportunidades de mejora, y cronometraje de todos los pasos. Tener una visión clara del rendimiento del proceso es necesario para identificar las contramedidas más correctas para eliminar la raíz del problema y planificar, de cara al futuro, las actividades que hay que hacer -y sobre qué KPI medir- para hacerlo más eficiente.
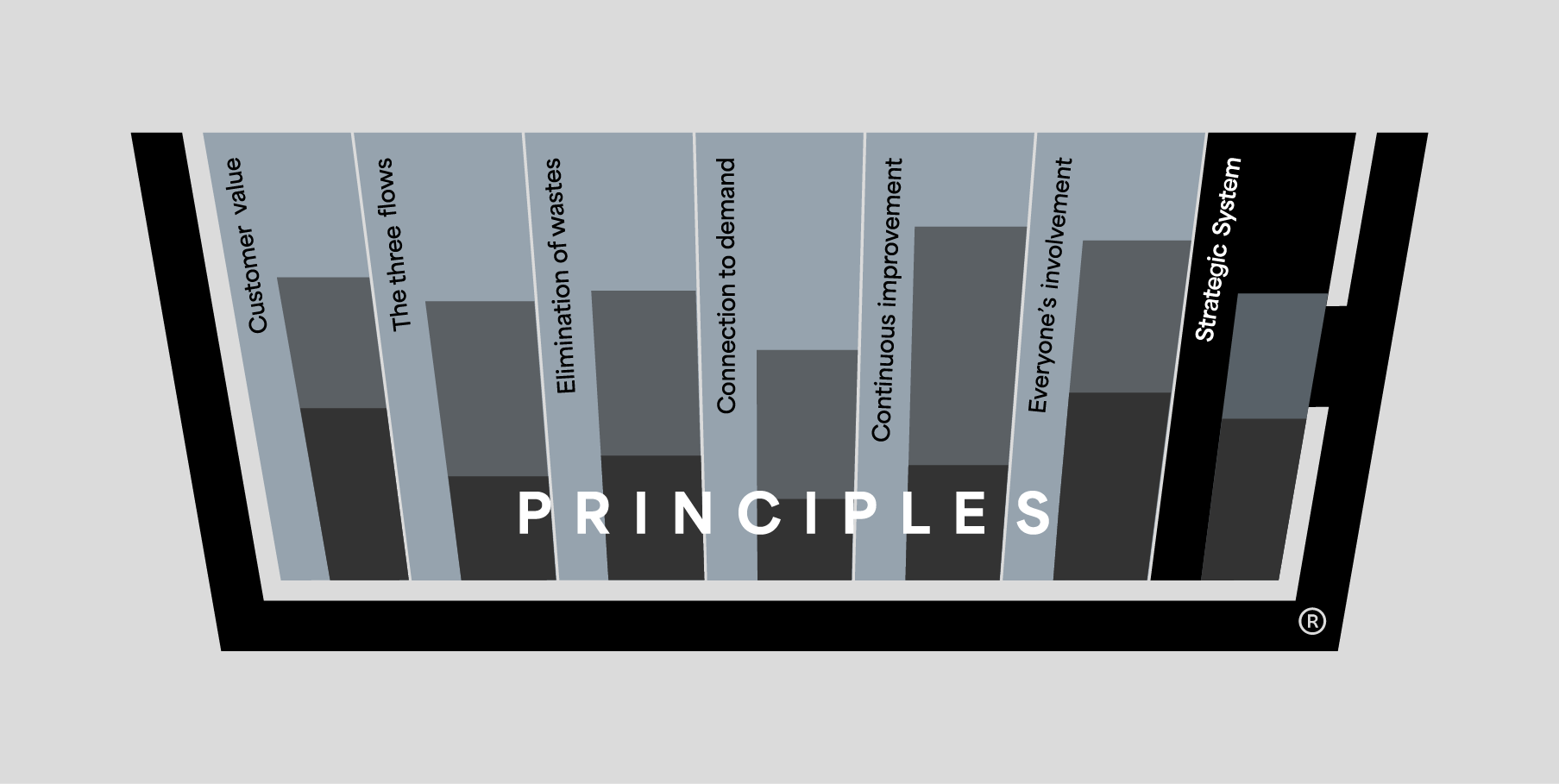
Las lagunas que surgieron
01
Retrasos en la entrega o entregas parciales de productos terminados
La gran variabilidad de la producción dio lugar a tiempos de producción inciertos que a veces provocaron retrasos en la entrega de los productos, negociaciones de cambio en fecha con el cliente y entregas parciales.
02
Elevado stock y wip
El largo plazo de entrega -desde el pedido hasta la expedición del producto terminado- llevó al cliente a solicitar cambios continuos que provocaban reprogramaciones de la producción. Las "urgencias" derivadas de los cambios de planeación "superaban" a los pedidos en curso. Además, los transportes entre departamentos eran frecuentes, al igual que las esperas provocadas por un sistema de producción "push" basado en la llegada de material de la fase anterior del proceso, en lugar de la "llamada" de la fase posterior.
03
Información incorrecta o incompleta para el proceso de producción
La información necesaria para el correcto desarrollo de las operaciones de elaboración del producto terminado no siempre era correcta o completa. Esto aumentaba el riesgo de error porque dejaba la discreción operativa en manos del capataz y/o el operario.
PLAN
Lean RoadMap® en el Delivery
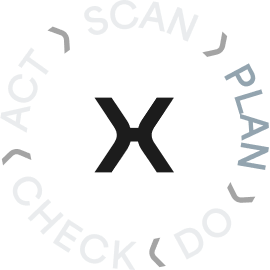
Una vez detectadas las carencias a partir del Lean Gap Analysis® pasamos a la siguiente fase, la fase de PLANIFICACIÓN. A través del Lean RoadMap® definimos así la secuencia de implementación de las técnicas Lean más adecuadas que nos permitirían alcanzar los objetivos acordados con el equipo de Officina 3. El Lean RoadMap® identifica las técnicas y métodos aplicados a lo largo del proyecto.
Hoja de ruta Lean
Fase en la que se planifica el estado futuro del proceso analizado desde una perspectiva multiescenario. Una vez elegido el escenario más correcto desde el punto de vista técnico y económico, se pasa a la planificación del camino a seguir para realizarlo. En el Lean RoadMap® surgen las actividades en las que hay que centrarse y el plazo en el que hay que completarlas.
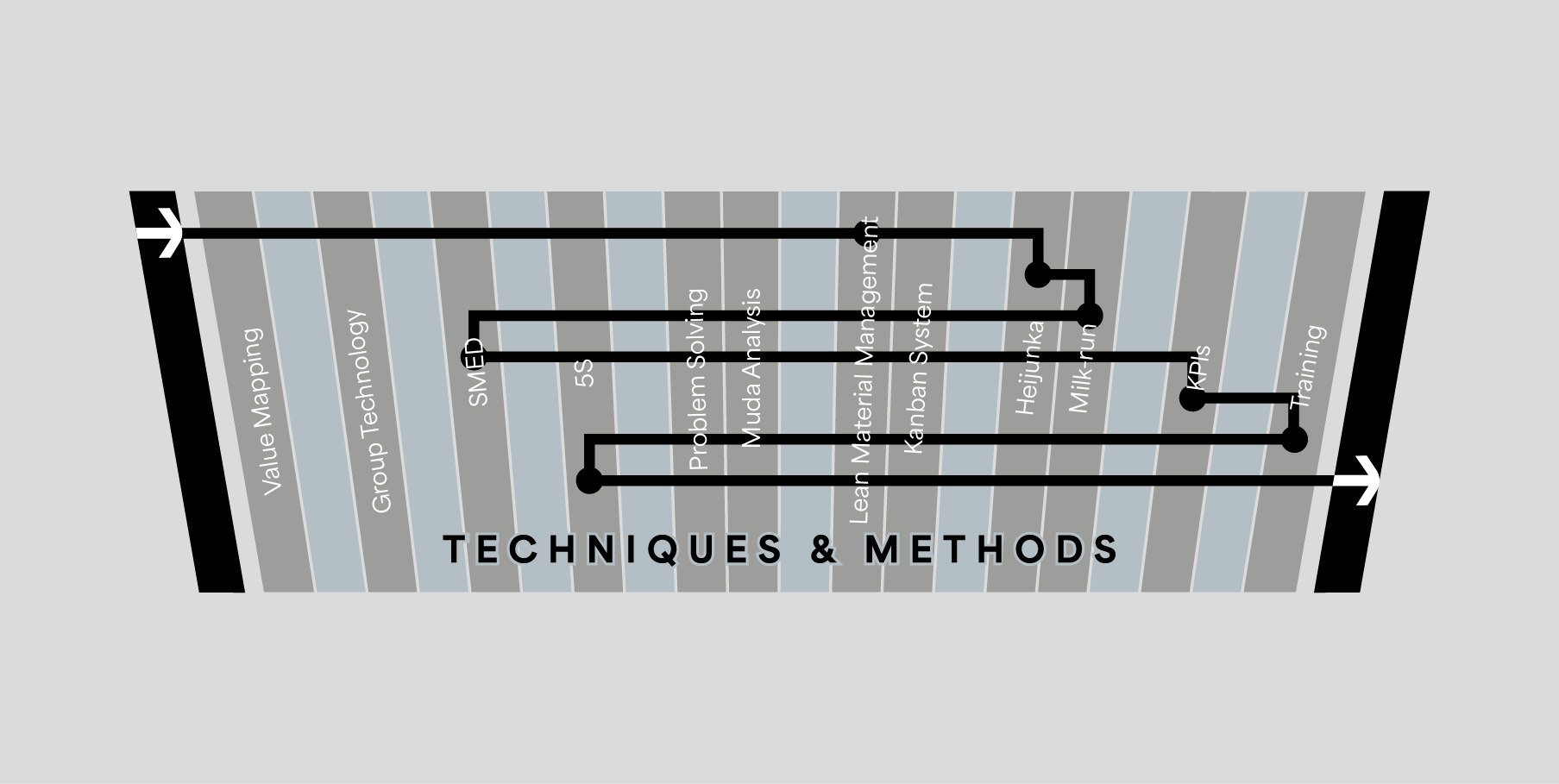
La dirección a seguir
01
Introducción de un priorizador
Para reducir los plazos de entrega en un proceso de producción con una gran variabilidad en términos de mezcla y volumen, es necesario vincular las distintas etapas en tiradas y definir criterios de prioridad -dictados por la capacidad disponible para producir las distintas fases- para el procesamiento en cada centro de trabajo.
02
Puesta en marcha de un milk run
Para reducir y estabilizar el plazo de entrega tanto de los proveedores de materias primas (calculado desde el momento en que se envía el pedido hasta el momento en que llega la mercancía) como de los subcontratistas (calculado desde el momento en que se envía el producto semiterminado hasta el momento en que se regresa una vez finalizada la transformación). Otra ventaja del milk run es que reduce los transportes extras y urgentes.
03
Aplicación de la técnica 5S
Facilitar el involucramiento, la formación y la polivalencia de los equipos y llevar la cultura del orden tanto a la producción como a las oficinas.
04
Gestión de la capacidad de producción
Para gestionar mejor los turnos de producción y asignar correctamente las tareas a los distintos operarios, se introdujo un sistema de supervisión con identificación de picos.
05
Creación de una matriz de competencias
Para que el equipo sea multifuncional y canalizar la formación hacia las fases de trabajo más críticas. También facilita la asignación de tareas a recursos específicos en función de sus conocimientos y competencias.
06
Kanban de materias primas
Para mantener bajo control el nivel de existencias de materias primas y, al mismo tiempo, evitar la urgencia y la escasez de existencias.
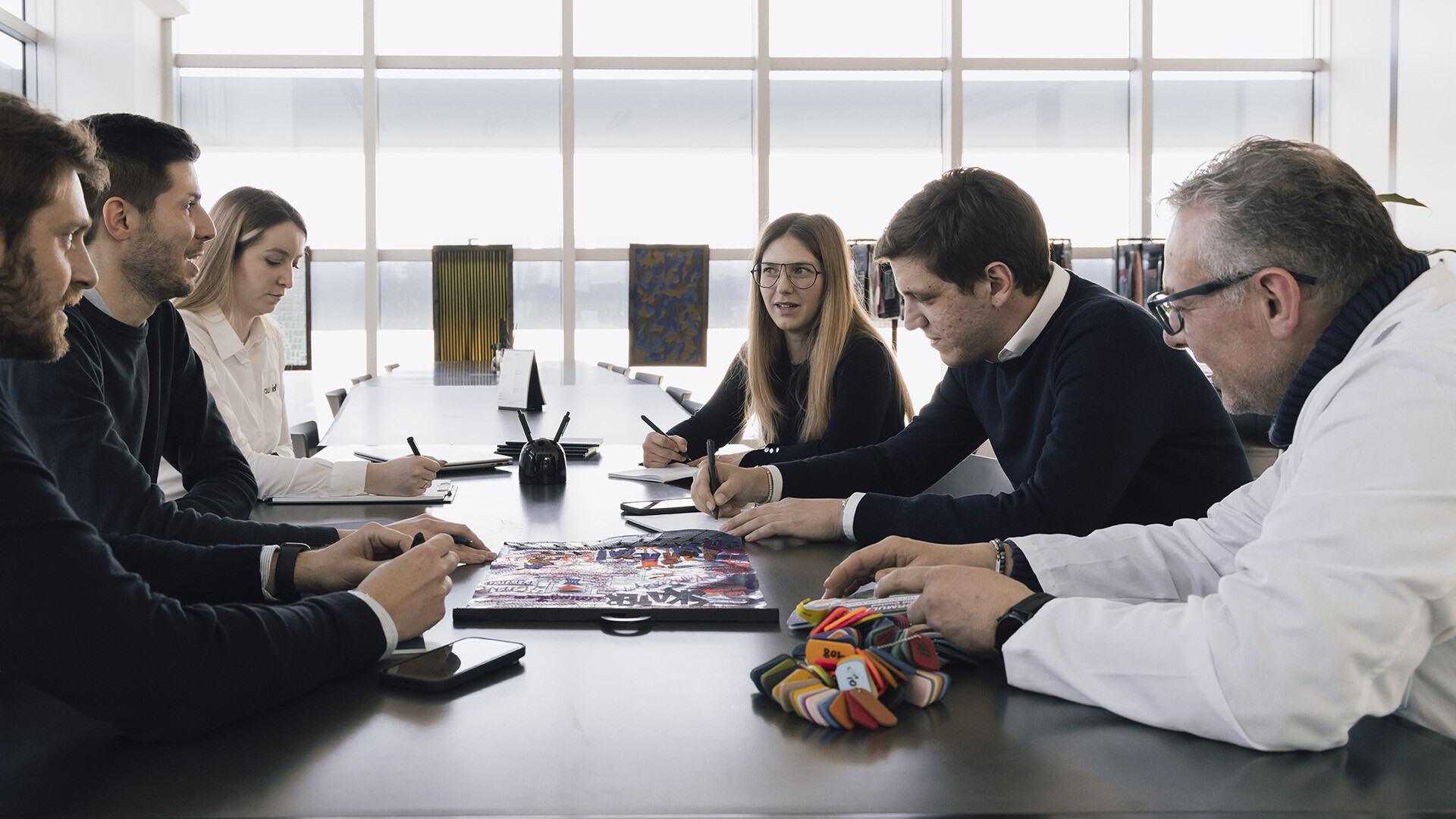
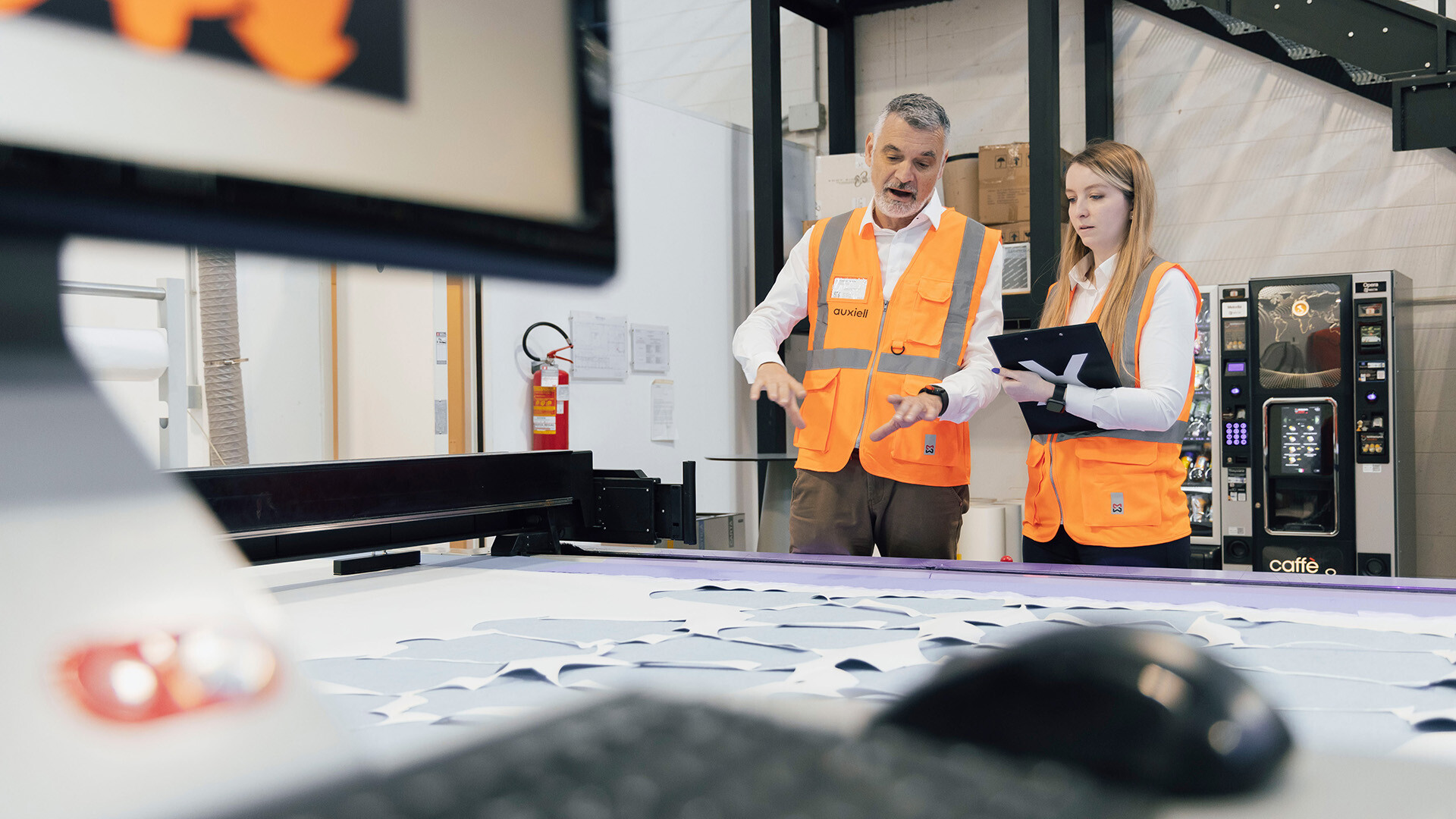
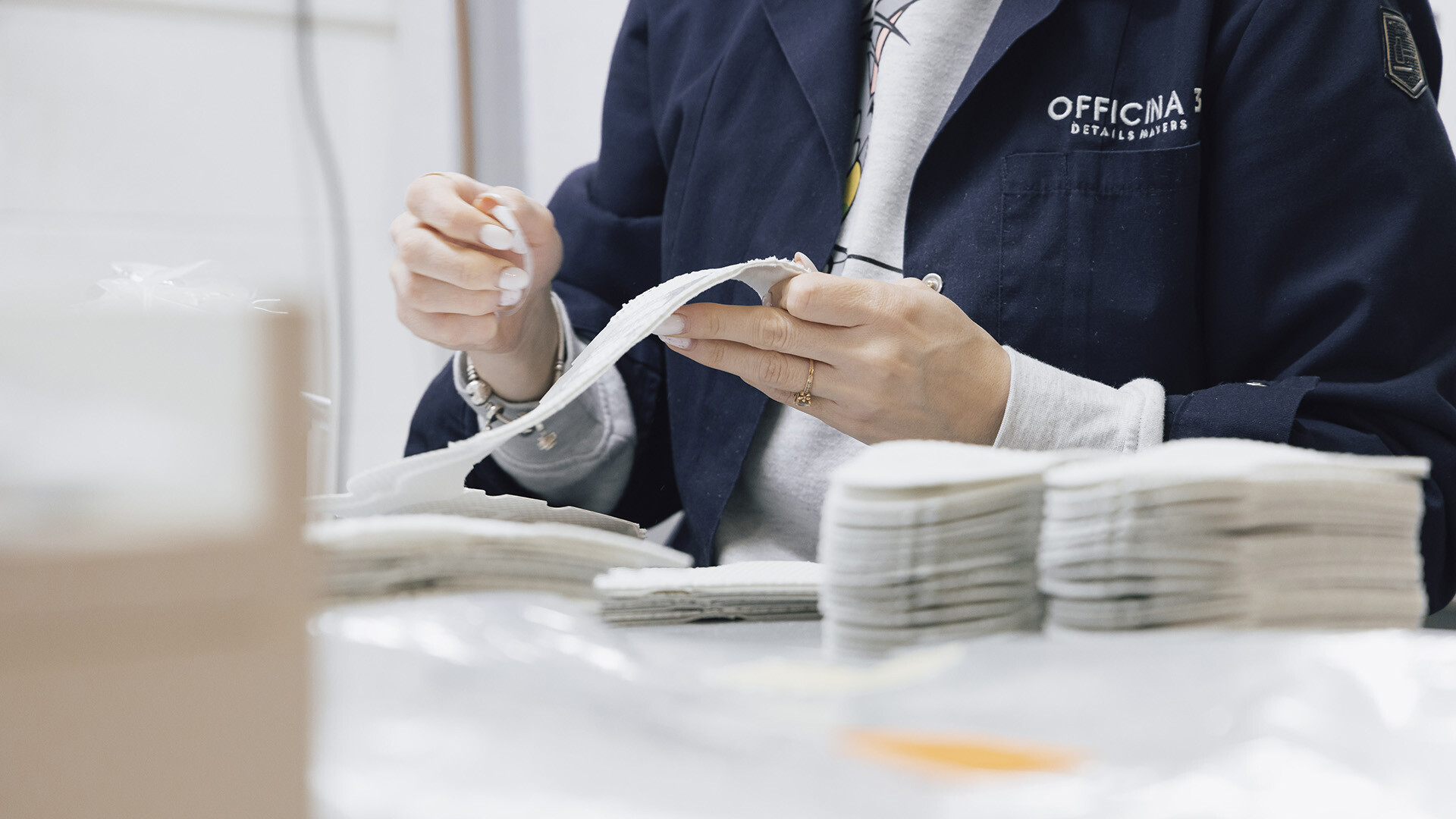
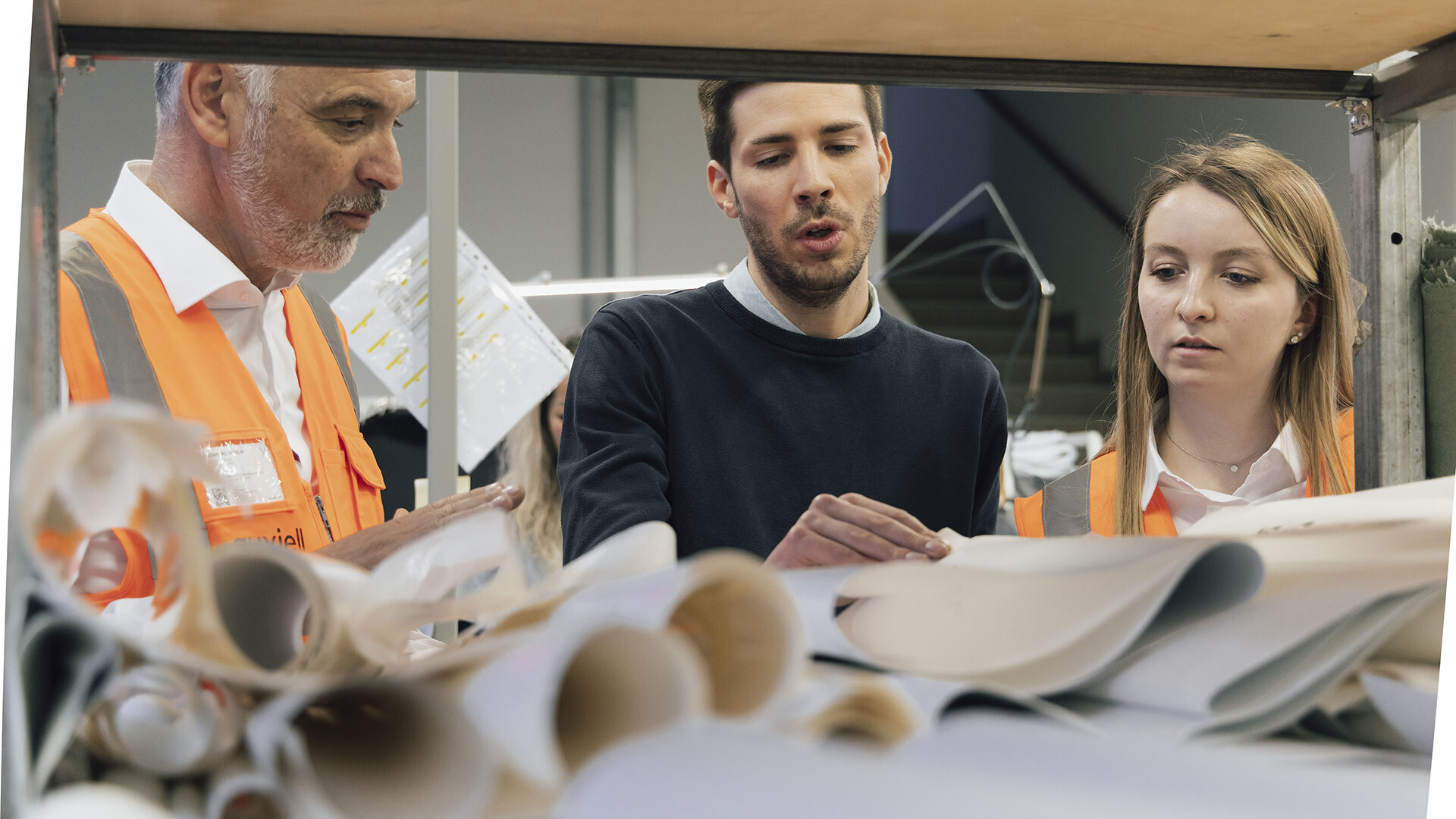
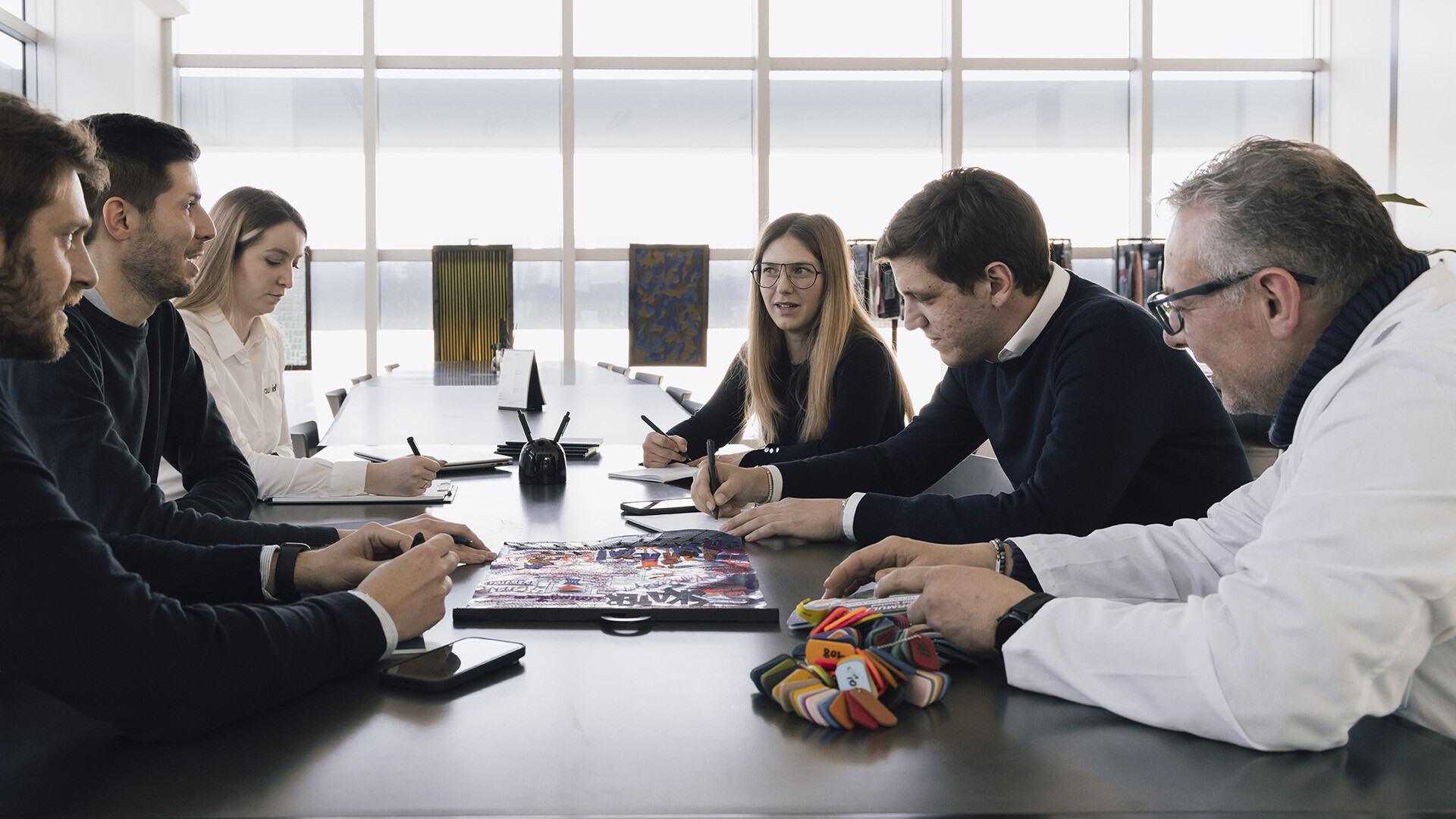
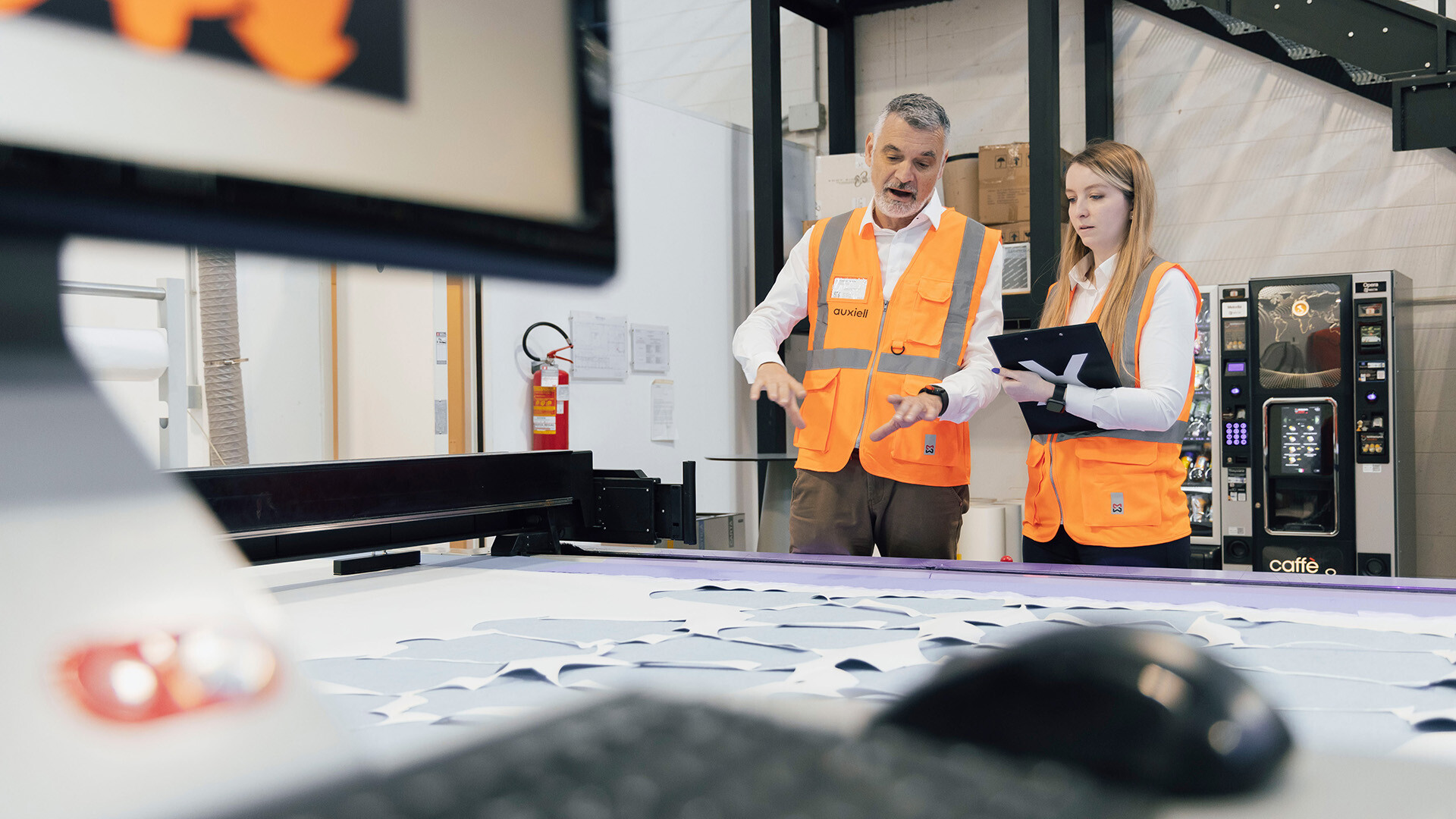
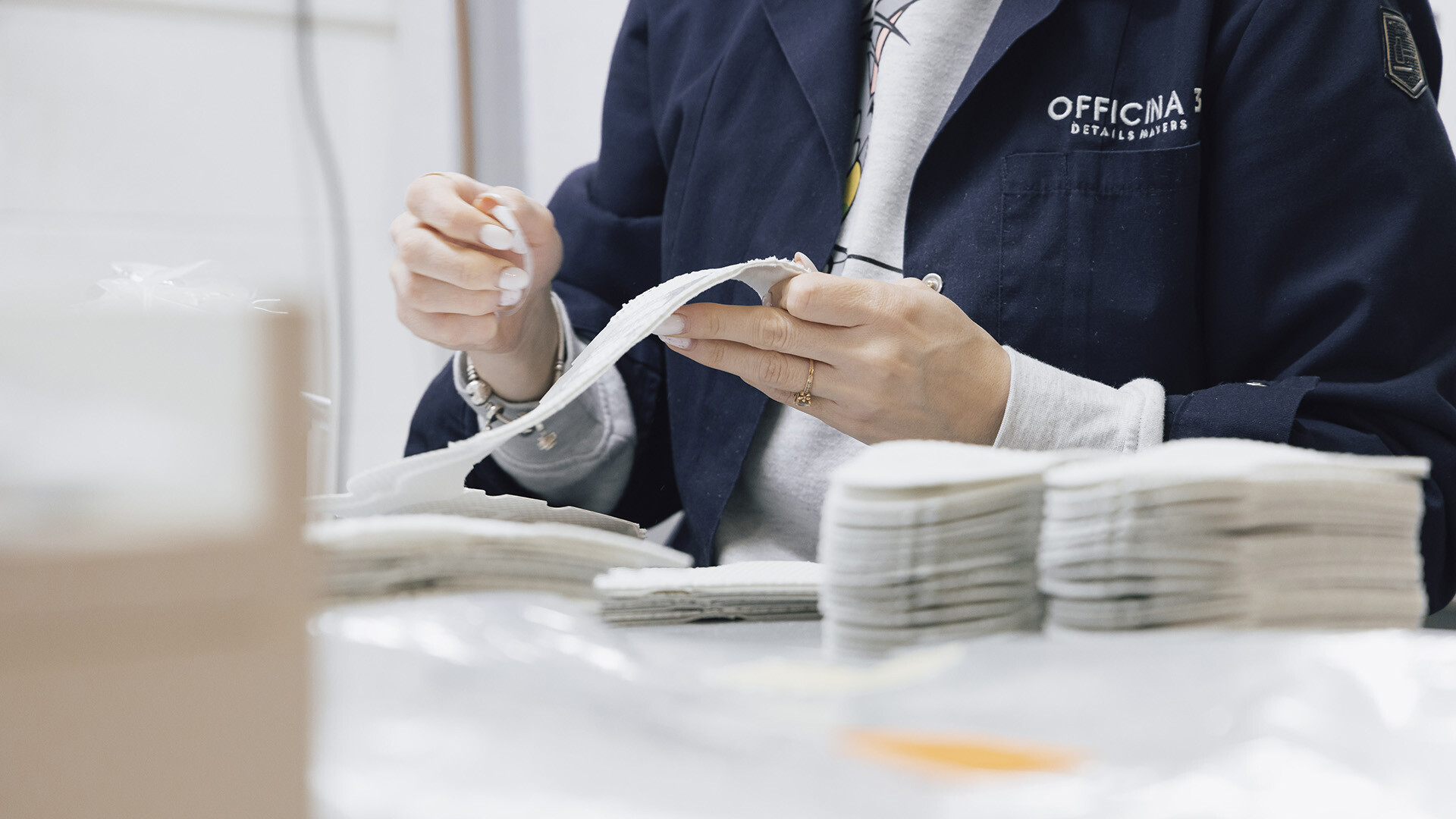
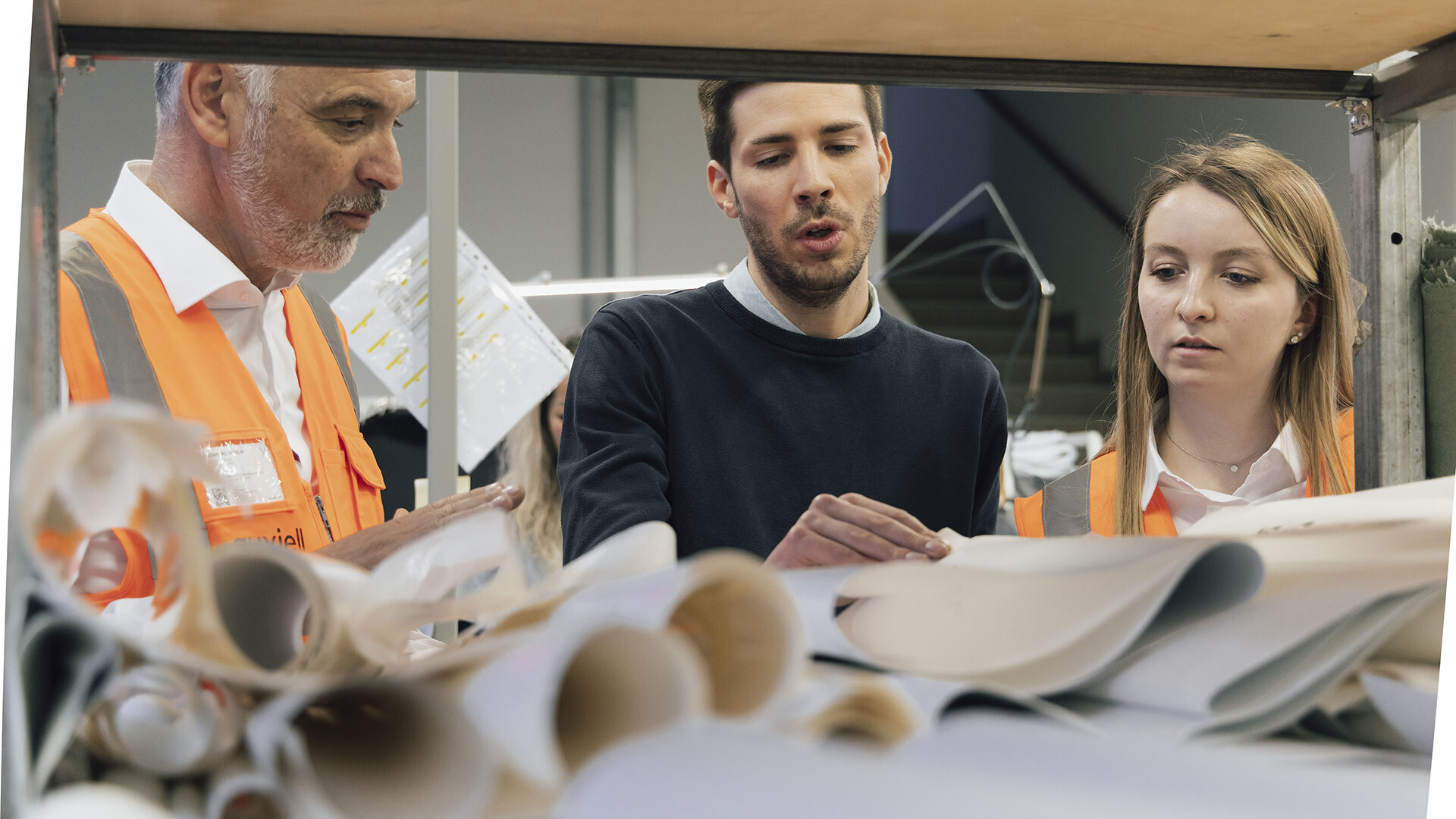
DO
Delivery Overall Transformation
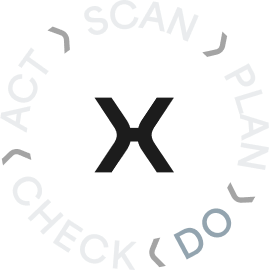
¿Qué actividades y técnicas lean nos han permitido alcanzar el objetivo definido?
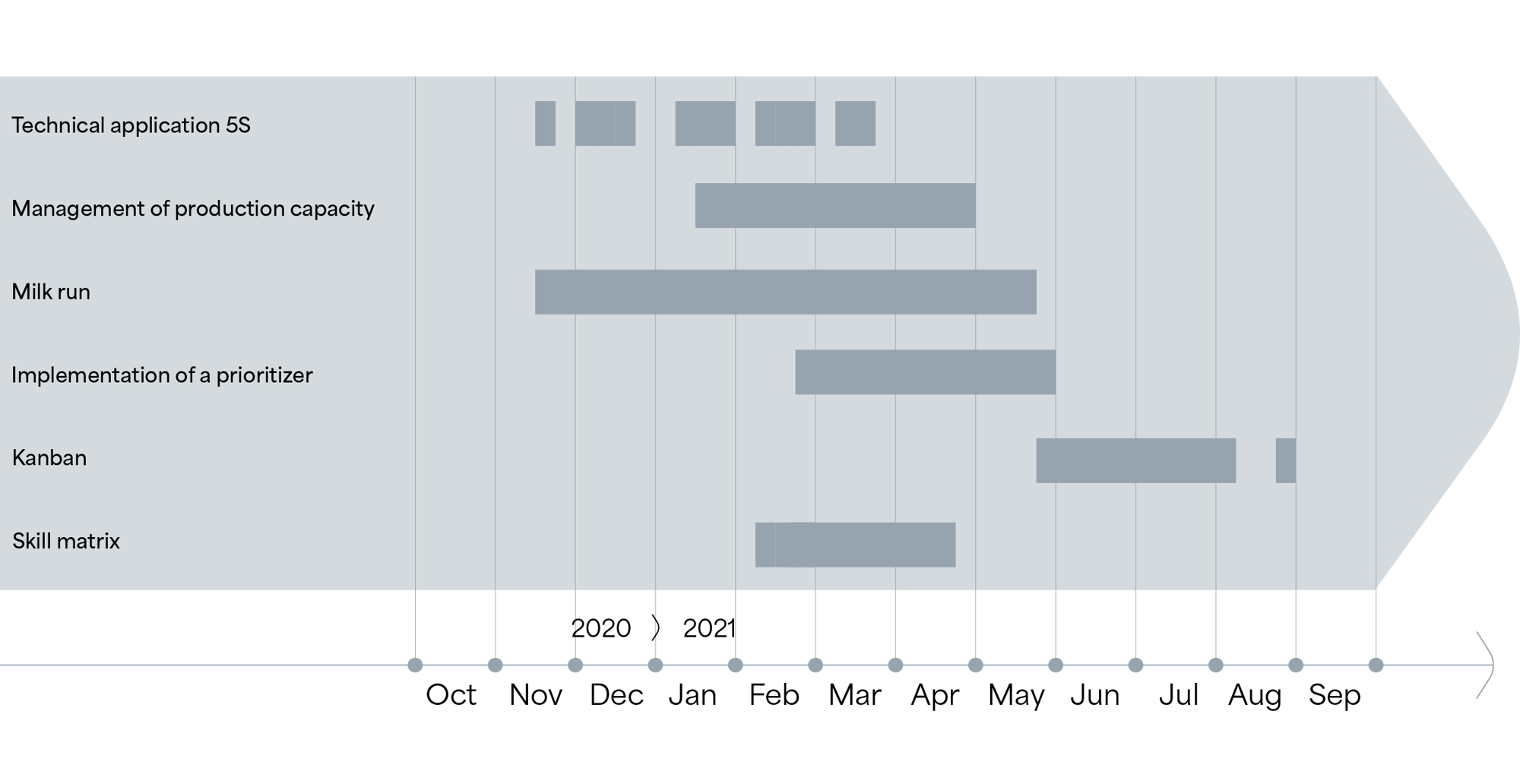
Implantación de un priorizador
Se desarrolló una herramienta ad-hoc para regular y controlar la cantidad de material entre centros en una perspectiva pull. Concretamente, para implantar dicha herramienta, en primer lugar se mapearon los centros de trabajo y sus características (distintas o similares entre mecanizados). En segundo lugar, se asignó a cada centro un determinado número de tarjetas kanban representativas de la capacidad de producción. Posteriormente, se instaló una pizarra que muestra los centros de mecanizado en filas y los tiempos en términos de franjas horarias y semanas en columnas. A continuación, se pueden utilizar las intersecciones individuales para introducir las tarjetas kanban. La tabla -denominada priorizador- indica qué centro de mecanizado está más descargado en un momento determinado y, por tanto, debe alimentarse con prioridad. El priorizador muestra la capacidad libre de los centros de mecanizado.
Recolección milk-run
Se implementó un sistema "flexible" para la recolección de materiales de proveedores y subcontratistas, con etapas estándar preestablecidas y etapas "según las necesidades" dictadas por los requerimientos de producción.
Aplicación de la técnica de las 5S
Se realizaron siete talleres sobre la aplicación de la técnica de las 5S, que incluyeron tanto formación teórica como aplicación práctica en puestos de trabajo específicos (tanto en producción como en las oficinas) para crear y mantener un entorno limpio y ordenado y formar al equipo para que luego fuera autónomo al momento de reproducir la técnica. Todos los miembros del equipo de Officina 3 participaron en la actividad y la acogieron con entusiasmo. Los puestos de trabajo rediseñados desde la perspectiva de las 5S nos permitieron recabar comentarios positivos de los clientes que nos visitaban y extender la actividad a los subcontratistas.
Gestión de la capacidad de producción
La gestión de inventario mediante el priorizador permitió estabilizar los plazos de las etapas y prever así la carga de trabajo diaria de cada centro para intervenir en caso de que superara la carga de trabajo máxima. El efecto final es un flujo de producción que fluye sin interrupciones.
Matriz de competencias
Para cada recurso, se estableció el nivel de conocimientos y competencias relacionados con cada operación de mecanizado. Esta información, combinada con los requisitos de producción para los centros de trabajo específicos, permitió definir un nivel de polivalencia objetivo. A continuación, la formación impartida por los líderes a los distintos operarios fue “motivada” por el objetivo de polivalencia definido y se centró en las competencias críticas. Por último, se puso en marcha un proceso de medición periódica del nivel de polivalencia de las figuras con el fin de conocer la evolución de los niveles establecidos.
Kanban de materias primas
Para reponer los códigos de las materias primas, se calculó la cantidad óptima que debía mantenerse en stock en función del consumo previsto y del plazo de suministro. Se adjuntó una etiqueta kanban a cada unidad que, cuando se agota, desencadena el proceso de reposición de material.
CHECK
¿Hemos alcanzado nuestros objetivos?
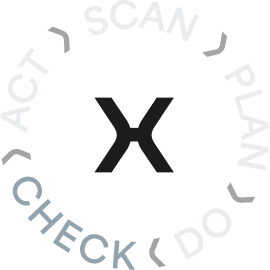
El plazo desde la puesta en producción hasta el envío se redujo en un 46%.
Limitar los movimientos innecesarios y las largas distancias ha contribuido a reducir la fatiga y el riesgo de accidentes de los operadores, mejorando la seguridad y la comodidad durante las actividades diarias. Un entorno más ergonómico también favorece una mayor concentración y un clima de trabajo más positivo, lo que repercute directamente en la motivación y la satisfacción del personal.
La optimización de los procesos de producción en el área de entregas ha permitido a Officina 3 garantizar plazos de entrega más estables y previsibles, reduciendo retrasos e ineficiencias. La mayor fiabilidad en los plazos ha reforzado la relación con las marcas de alta costura, que pueden contar con un socio capaz de responder con precisión y rapidez a sus necesidades.
Del Delivery al Development
Tras los resultados obtenidos y el alto nivel de implicación encontrado en la mejora del macroproceso de Delivery, el equipo de Officina 3 lanzó de forma independiente nuevas iniciativas, aplicando las competencias adquiridas durante la transformación. La mejora de los resultados en Delivery llevó a la empresa a extender la optimización también al macroproceso de Development, confirmando su compromiso con la evolución continua y la gestión cada vez más eficaz de los procesos.
SCAN
Lean Gap Analysis® en development
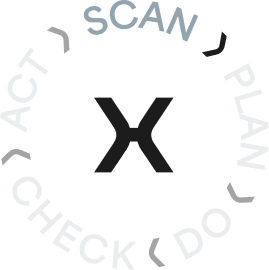
Reducir y estabilizar los plazos de entrega de muestras y prototipos era una prioridad. Si los plazos de entrega son cruciales para la producción en serie, lo son aún más cuando se trata de desarrollar prototipos y muestras, donde la rapidez y la precisión marcan la diferencia.
Lean Gap Analysis
Fase indispensable para medir y analizar los procesos actuales y definir las diferencias entre el estado actual y el deseado. En esta primera fase se toma una "instantánea" del estado actual de los procesos en términos de cuantificación de residuos, identificación de posibles problemas y oportunidades de mejora, y cronometraje de todos los pasos. Tener una visión clara del rendimiento del proceso es necesario para identificar las contramedidas más correctas para eliminar la raíz del problema y planificar, con vistas al futuro, las actividades que hay que hacer -y sobre qué KPI medir- para hacerlo más eficiente.
Las brechas que surgieron
01
Retrasos y puntualidad para muestras y prototipos
Al igual que en el macroproceso Delivery, los plazos de entrega de muestras también son críticos en Development. Aquí también se registraron retrasos o entregas urgentes.
PLAN
Lean RoadMap® en development
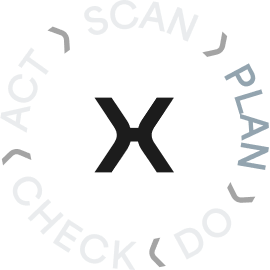
Una vez identificadas las carencias a partir del Lean Gap Analysis®, pasamos a la siguiente fase, la fase de PLAN. A través del Lean RoadMap® definimos así la secuencia de implementación de las técnicas Lean adecuadas que nos permitirían alcanzar los objetivos acordados con el equipo de Officina 3. El Lean RoadMap® identifica las técnicas y métodos aplicados a lo largo del proyecto.
Hoja de ruta Lean
Fase en la que se planifica el estado futuro del proceso analizado desde una perspectiva multiescenario. Una vez elegido el escenario más correcto desde el punto de vista técnico y económico, se pasa a la planificación del camino a seguir para realizarlo. En el Lean RoadMap® surgen las actividades en las que hay que centrarse y el plazo en el que hay que completarlas.
La dirección a seguir
01
Planeación del Heijunka
Se implantó un tablero Heijunka a la entrada de la zona de muestreo para nivelar las cargas de trabajo en las máquinas de muestreo y planear correctamente la producción en función de las fechas exigidas por el cliente.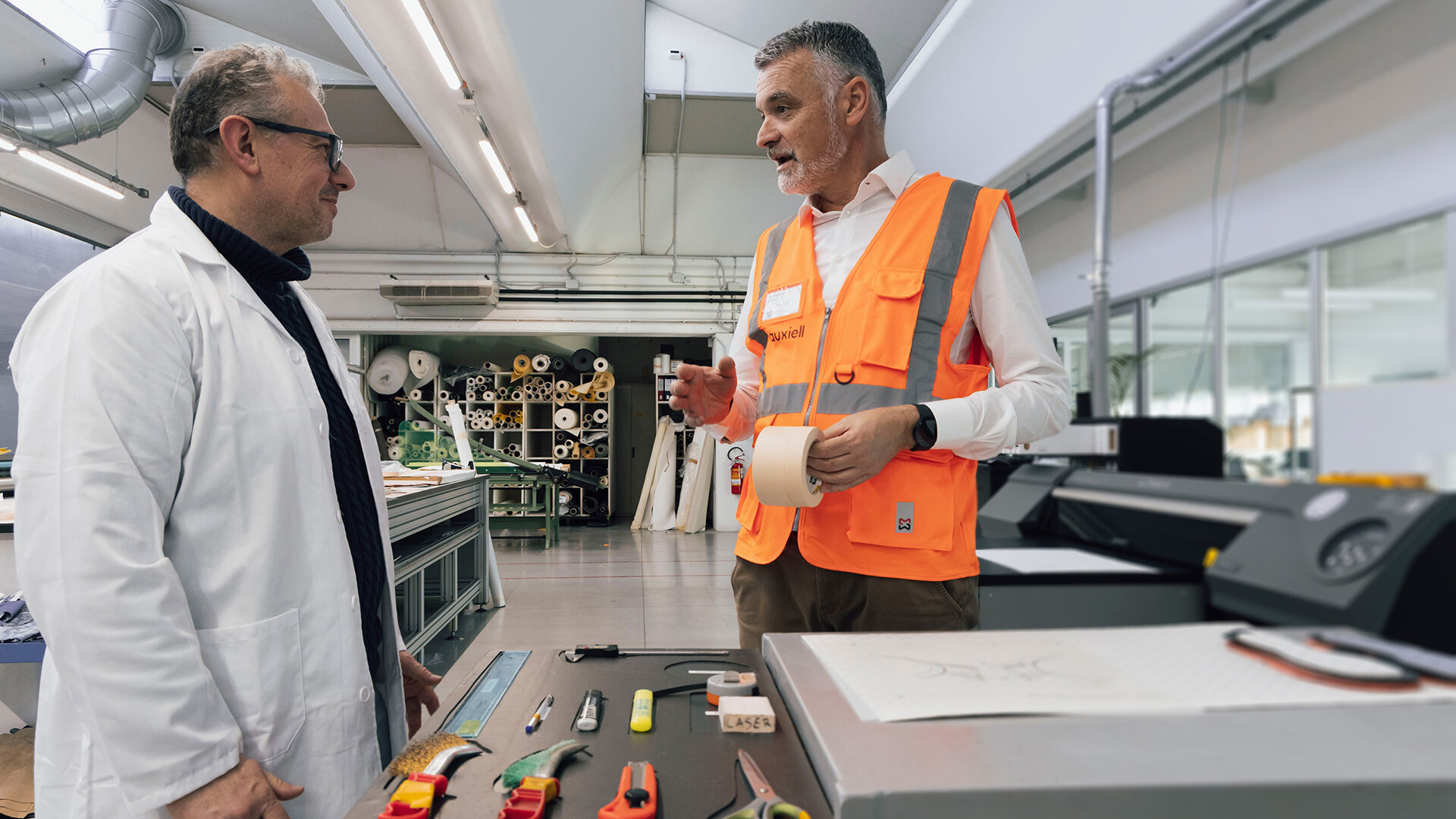
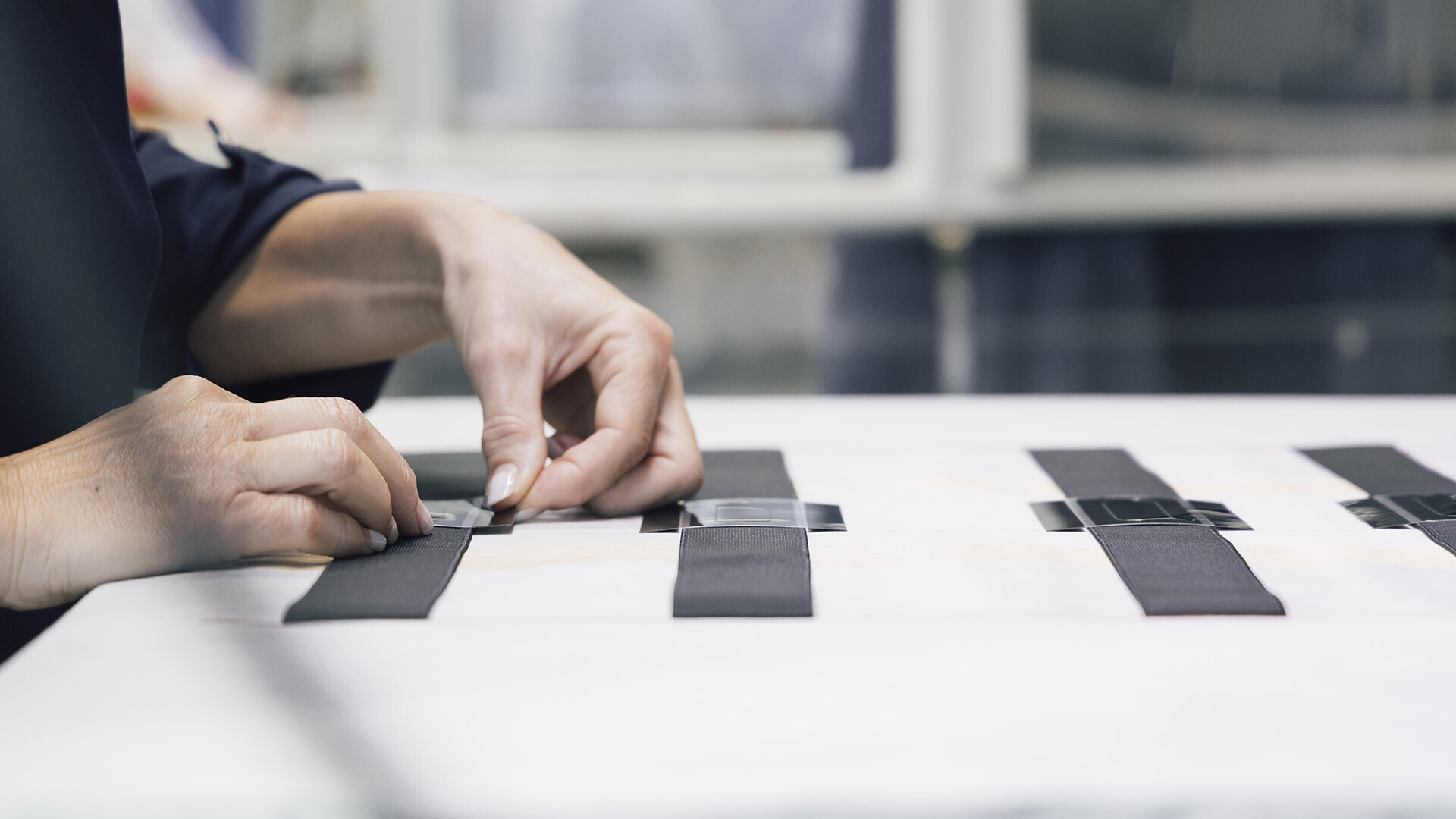
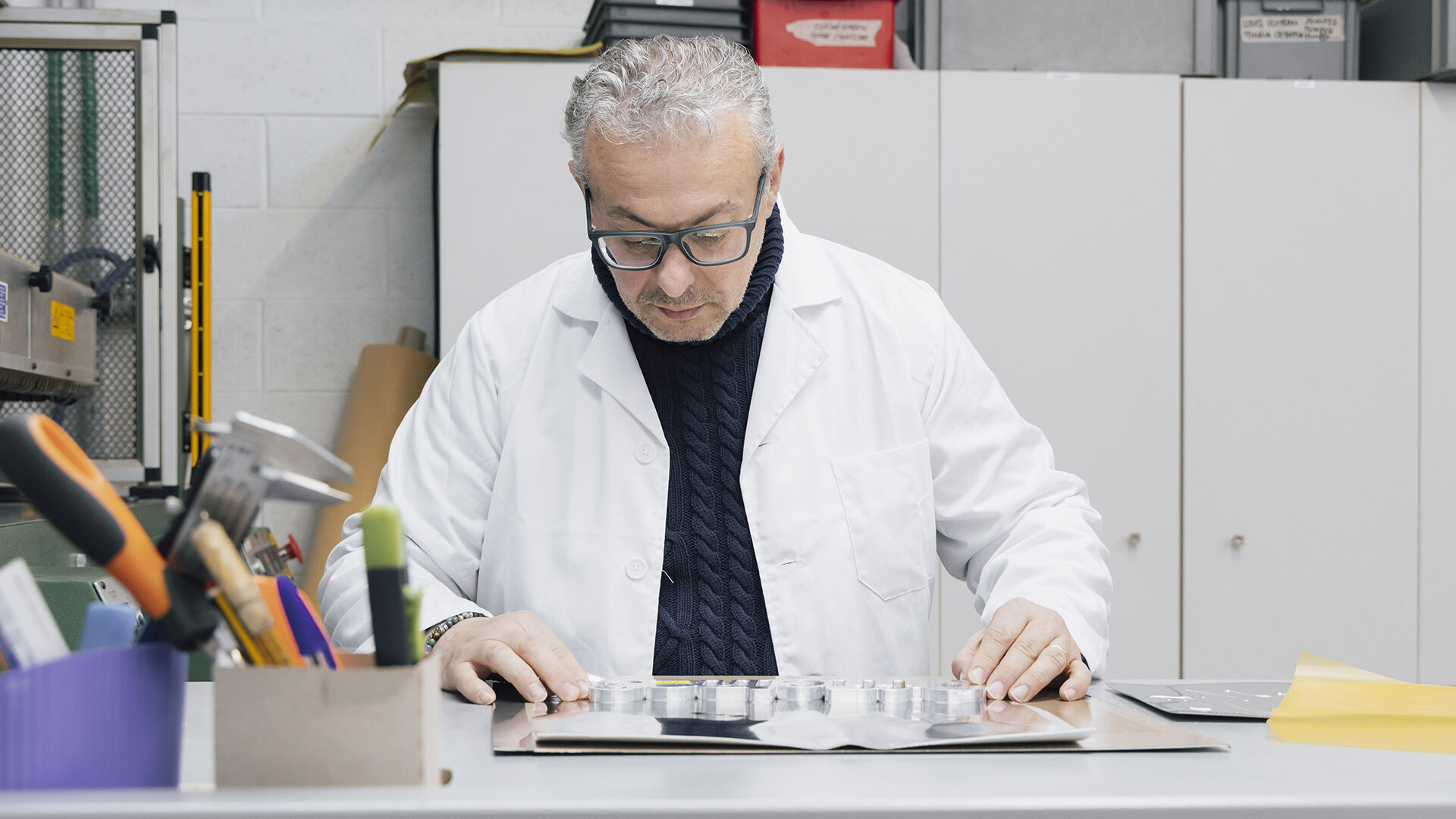
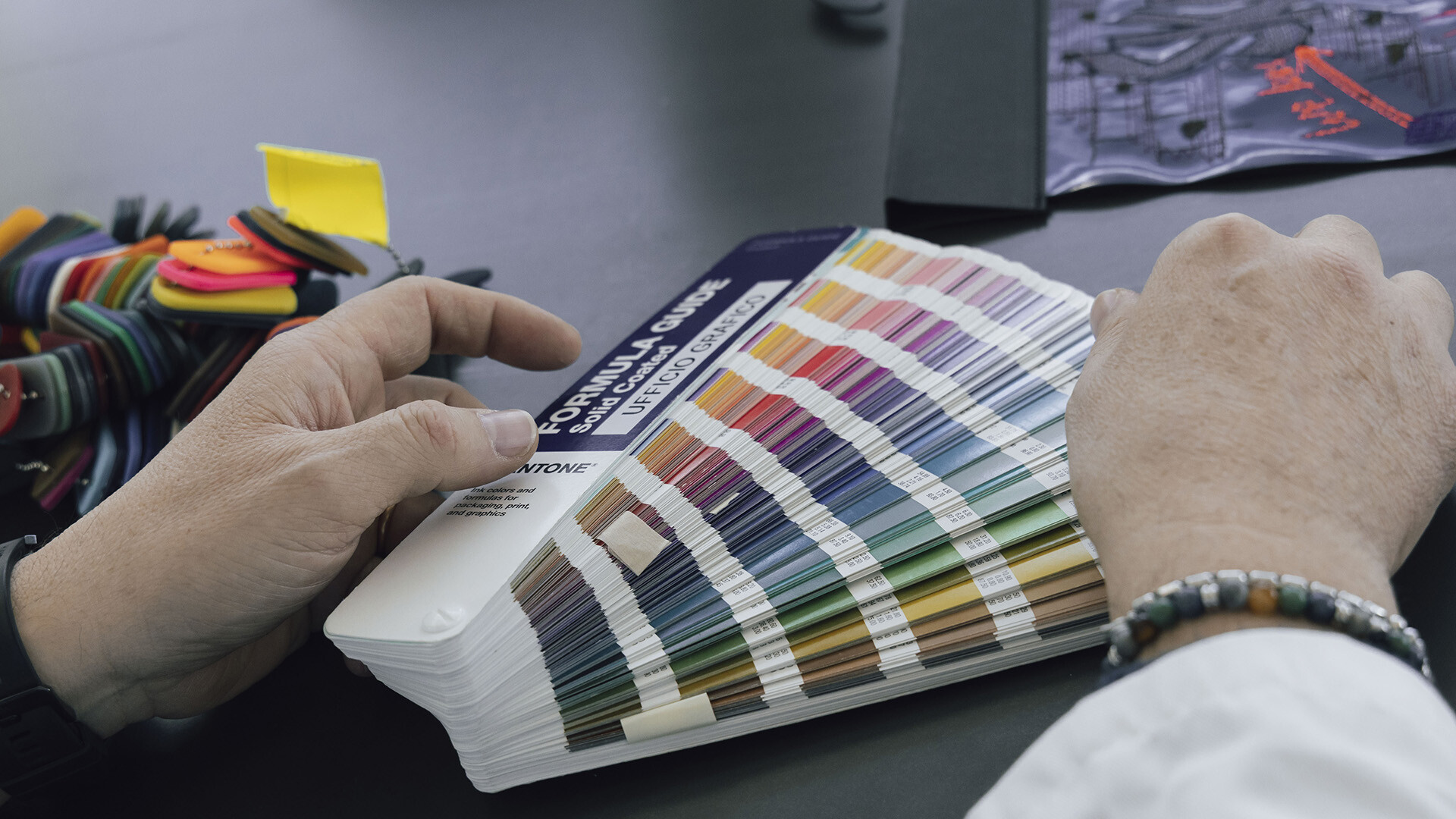
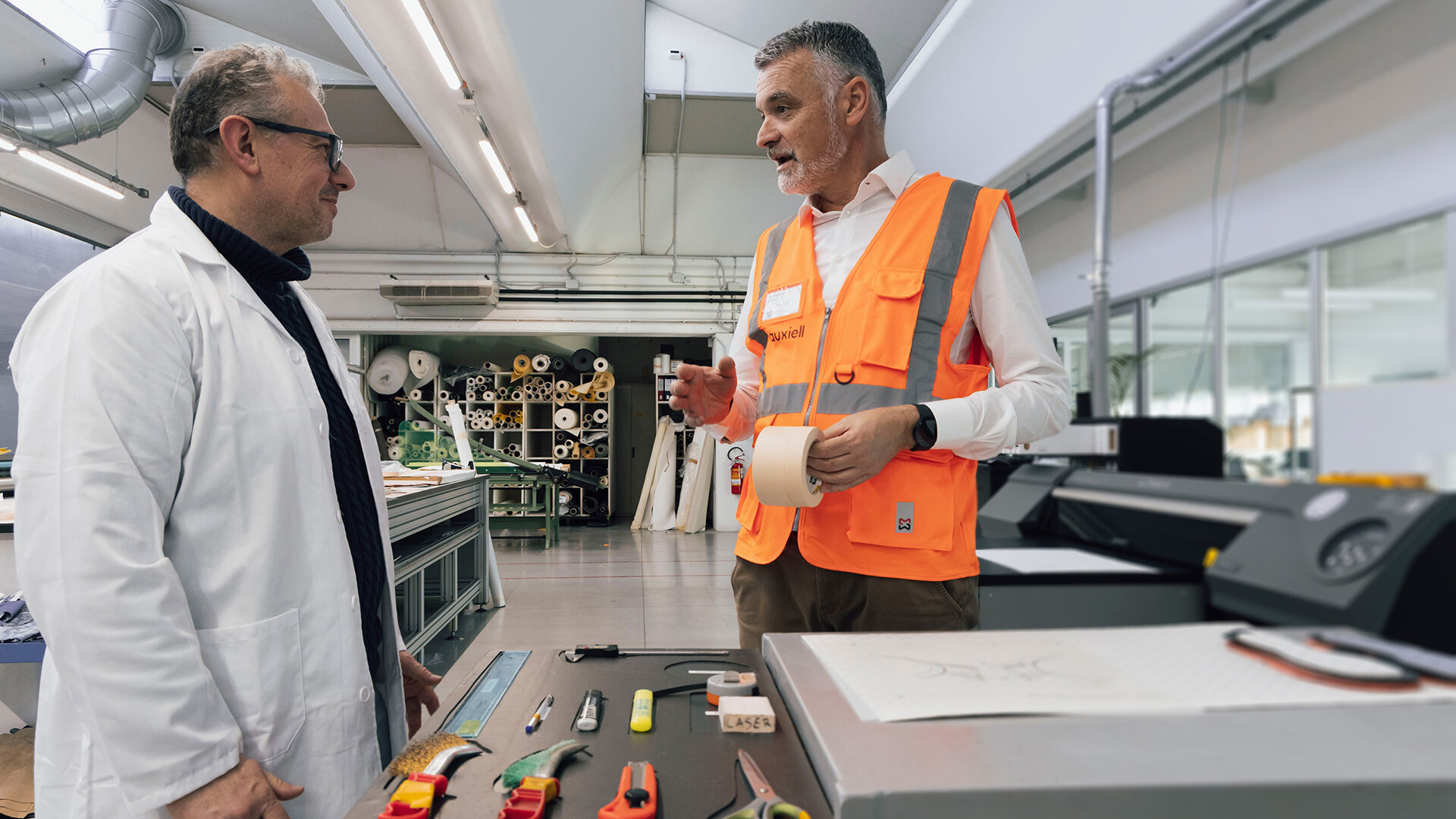
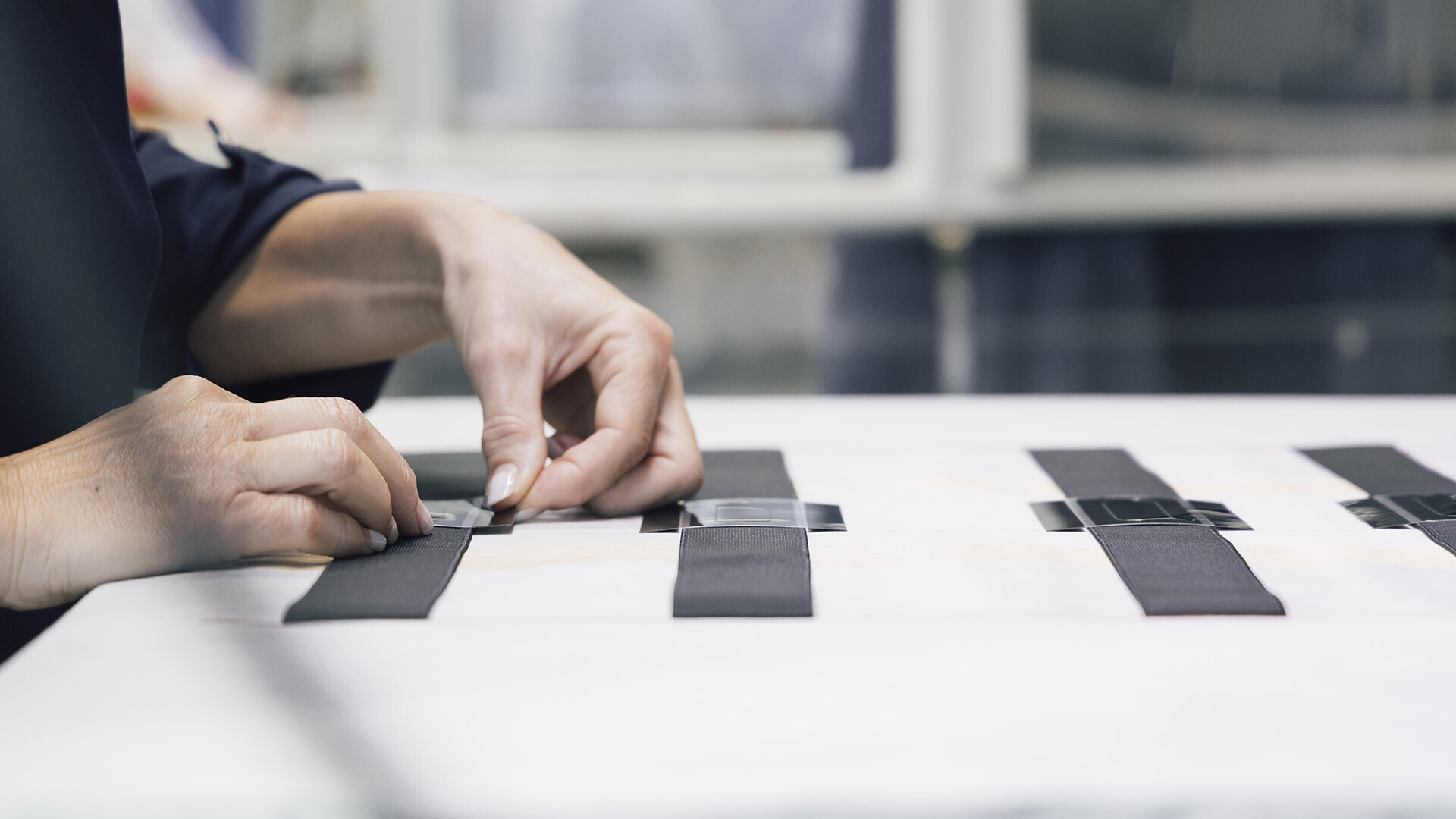
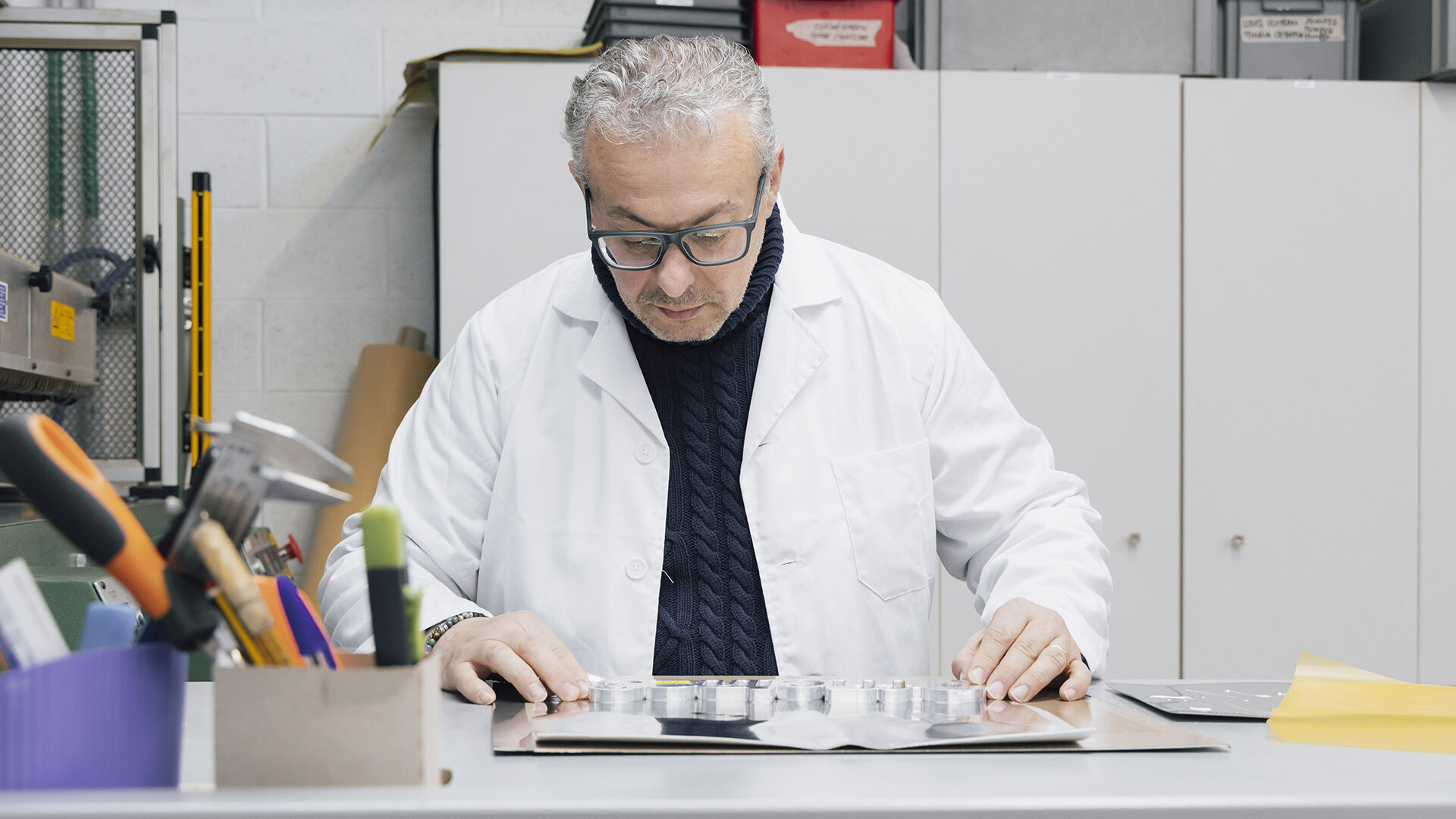
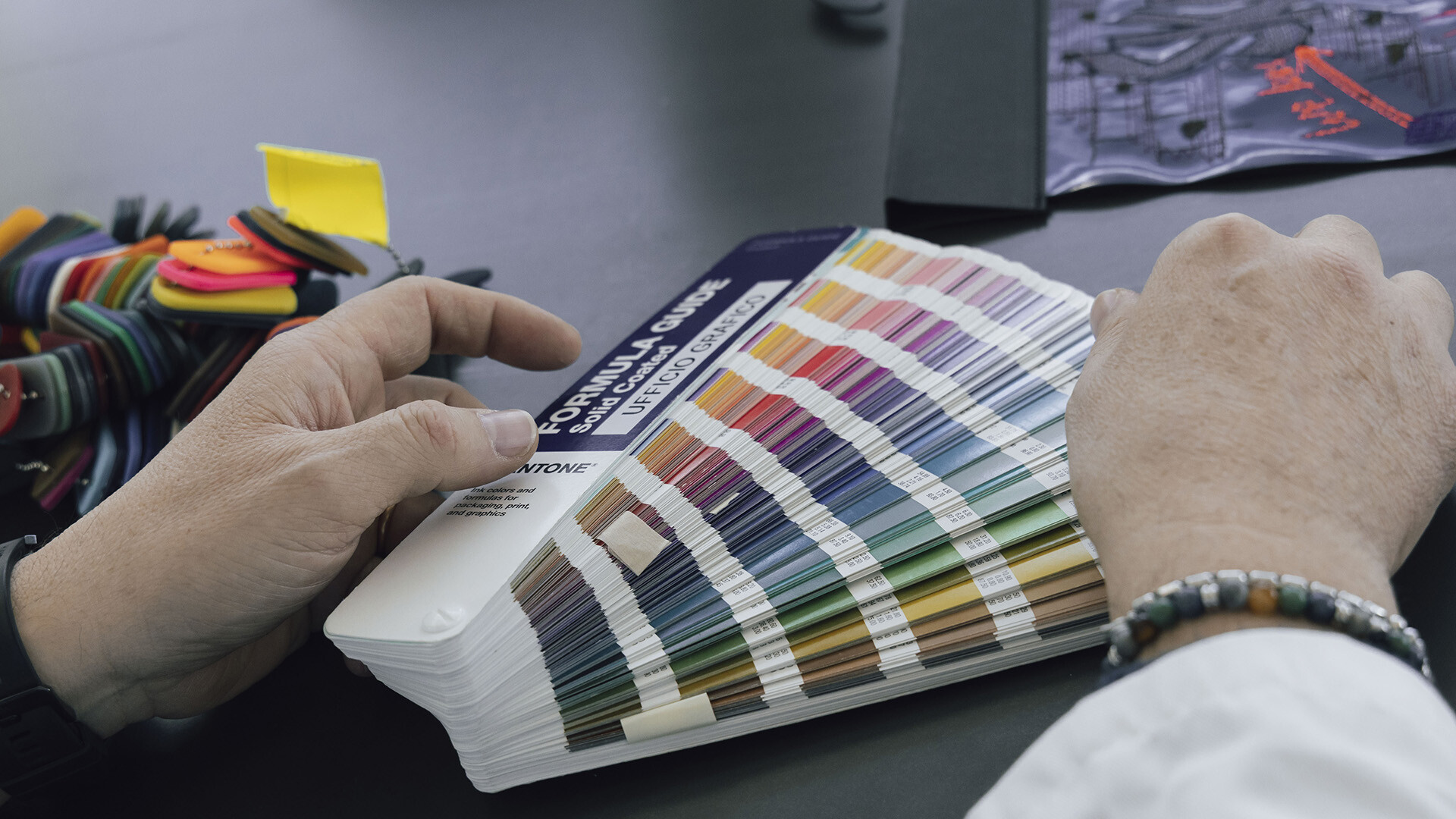
DO
Diseño para simplificar
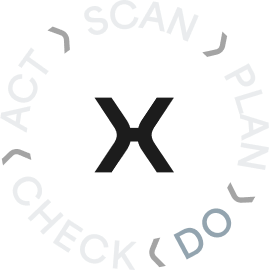
¿Qué actividades y técnicas lean nos han permitido alcanzar el objetivo fijado?
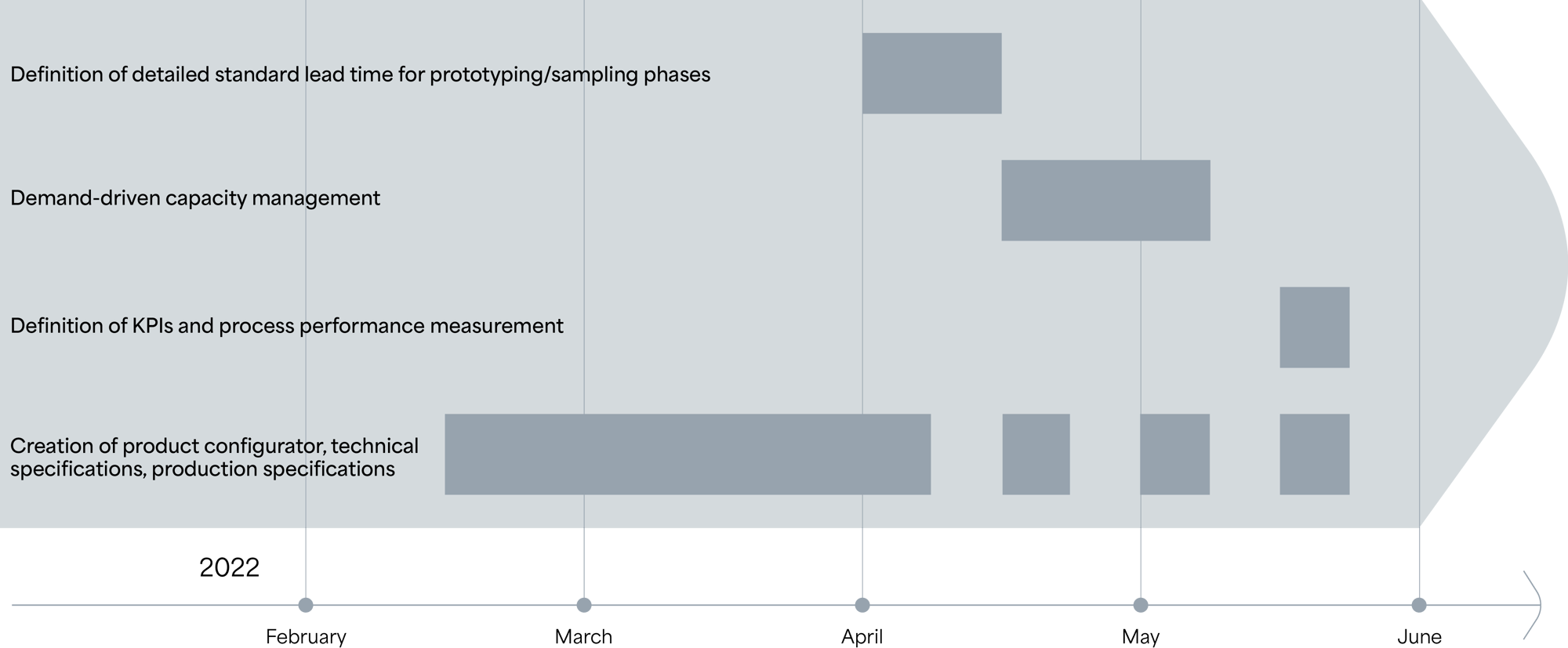
Aplicación de la Heijunka
Se identificaron las fases de trabajo del proceso de muestreo y se recopilaron datos sobre limitaciones y tiempos de ciclo. Mediante la implementación de un tablero visual, fue posible dar visibilidad de planeación a los operadores de muestreo, lo que les permitió organizar los materiales y equipos con suficiente antelación. Para ello, es esencial una gestión ordenada de los materiales en la zona. Por ello, la Heijunka de planeación se definió con una gestión visual en el suelo: el material que se preveía procesar un día determinado se colocaba en el espacio dedicado a ello. De este modo, los operadores perdían menos tiempo buscando el material.
CHECK
¿Hemos alcanzado nuestros objetivos?
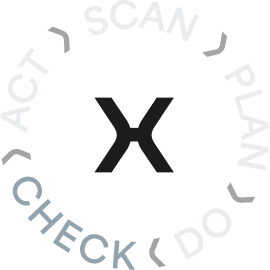
La actividad de creación de herramientas como Heijunka Board y Visual Management en piso fue llevada a cabo de forma independiente por el equipo de Officina 3 con destreza y proactividad, utilizando las nociones aprendidas durante la transformación del proceso de Delivery.
Gracias a una gestión más clara de las prioridades y a la introducción de un sistema pull, el muestreo y la creación de prototipos siguen ahora un flujo más lineal, sin interrupciones ni acumulaciones.
La implementación de Heijunka mejoró la gestión del muestreo, garantizando una planeación clara y estructurada. El tablero visual dio visibilidad a las actividades, permitiendo organizar los materiales y equipos con anticipación, mientras que la gestión visual en planta eliminó los tiempos de búsqueda. El equipo de Officina 3 aplicó estas herramientas de forma autónoma, consolidando las competencias adquiridas en la transformación del proceso de Delivery. El resultado es un flujo más lineal, sin interrupciones ni amontonamientos, gracias a una gestión eficaz de las prioridades y a la introducción de un sistema pull.
Del Development al Deployment
Debido a los resultados obtenidos y al alto nivel de involucramiento en la mejora del macroproceso de Development, el equipo de Officina 3 emprendió de forma independiente nuevas iniciativas, aplicando las competencias adquiridas durante la transformación.
Un ejemplo concreto fue la aceptación independiente de las herramientas Heijunka y Visual Management, demostrando capacidad de gestión y espíritu proactivo. La optimización del Development llevó a la empresa a ampliar la intervención también al macroproceso de Deployment, reforzando la eficacia operativa y la continuidad de la mejora.
SCAN
Lean Gap Analysis® en el Deployment
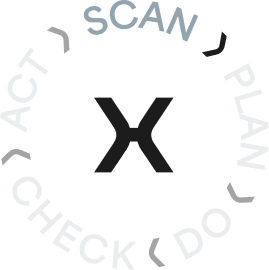
La empresa, especializada en el apoyo a marcas de alta costura, necesitaba reorganizar su estrategia para mejorar la eficacia operativa. La rapidez y variabilidad de las solicitudes hacían compleja la gestión estructurada de las actividades, lo que creaba dificultades para priorizar y optimizar los flujos de trabajo. En respuesta a esta necesidad, se inició un proceso de reorganización para poner orden en los procesos, garantizando una ejecución más rápida y una gestión más eficaz de las actividades. El objetivo era reforzar la posición de la empresa como socio de referencia para el sector de la alta costura.
Lean Gap Analysis
Fase indispensable para medir y analizar los procesos actuales y definir las diferencias entre el estado actual y el deseado. En esta primera fase se toma una "instantánea" del estado actual de los procesos en términos de cuantificación de residuos, identificación de posibles problemas y oportunidades de mejora, y cronometraje de todos los pasos. Tener una visión clara del rendimiento del proceso es necesario para identificar las contramedidas más correctas para eliminar la raíz del problema y planificar, de cara al futuro, las actividades que hay que hacer -y sobre qué KPI medir- para hacerlo más eficiente.
Las brechas que surgieron
01
Falta de priorización de los proyectos a realizar
Los objetivos estratégicos estaban claros para la dirección y los propietarios, pero la prioridad y la frecuencia de ejecución de los distintos proyectos en relación con los objetivos que debían alcanzarse no estaban claras.
PLAN
Implantación de Lean RoadMap
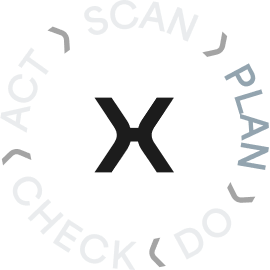
Una vez detectadas las carencias a partir del Lean Gap Analysis® pasamos a la siguiente fase, la fase de PLANEACIÓN. A través del Lean RoadMap® definimos así la secuencia de implementación de las técnicas Lean más correctas que nos permitirían alcanzar los objetivos acordados con el equipo de Officina 3. El Lean RoadMap® identifica las técnicas y métodos aplicados a lo largo del proyecto.
Hoja de ruta Lean
Fase en la que se planifica el estado futuro del proceso analizado desde una perspectiva multiescenario. Una vez elegido el escenario más correcto desde el punto de vista técnico y económico, se pasa a la planificación del camino a seguir para realizarlo. En el Lean RoadMap® surgen las actividades en las que hay que centrarse y el plazo en el que hay que completarlas.
La dirección a seguir
01
Aplicación de A3-X
Una herramienta para definir proyectos relevantes para la estrategia corporativa y relacionarlos con las personas, los objetivos y los indicadores clave.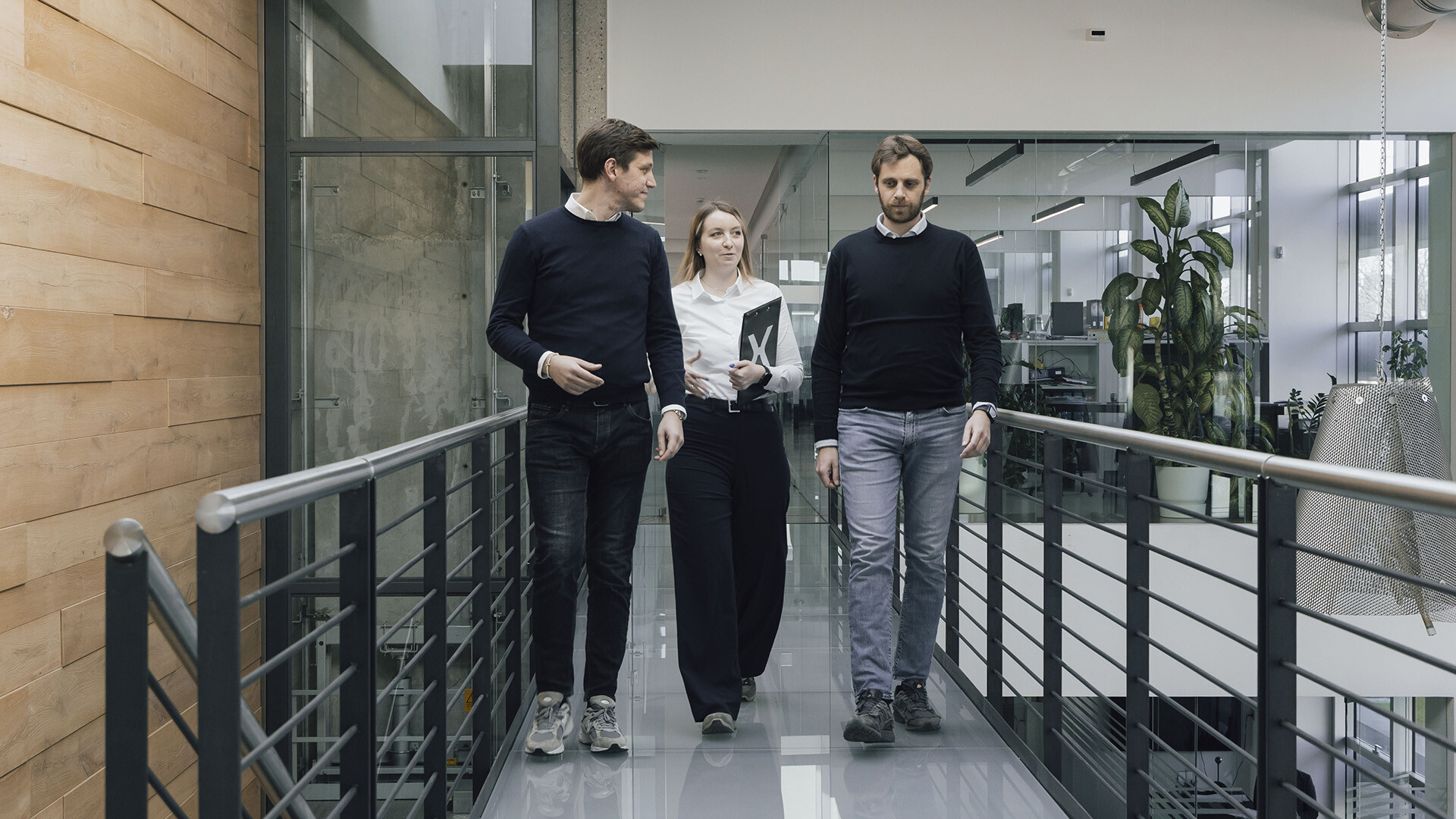
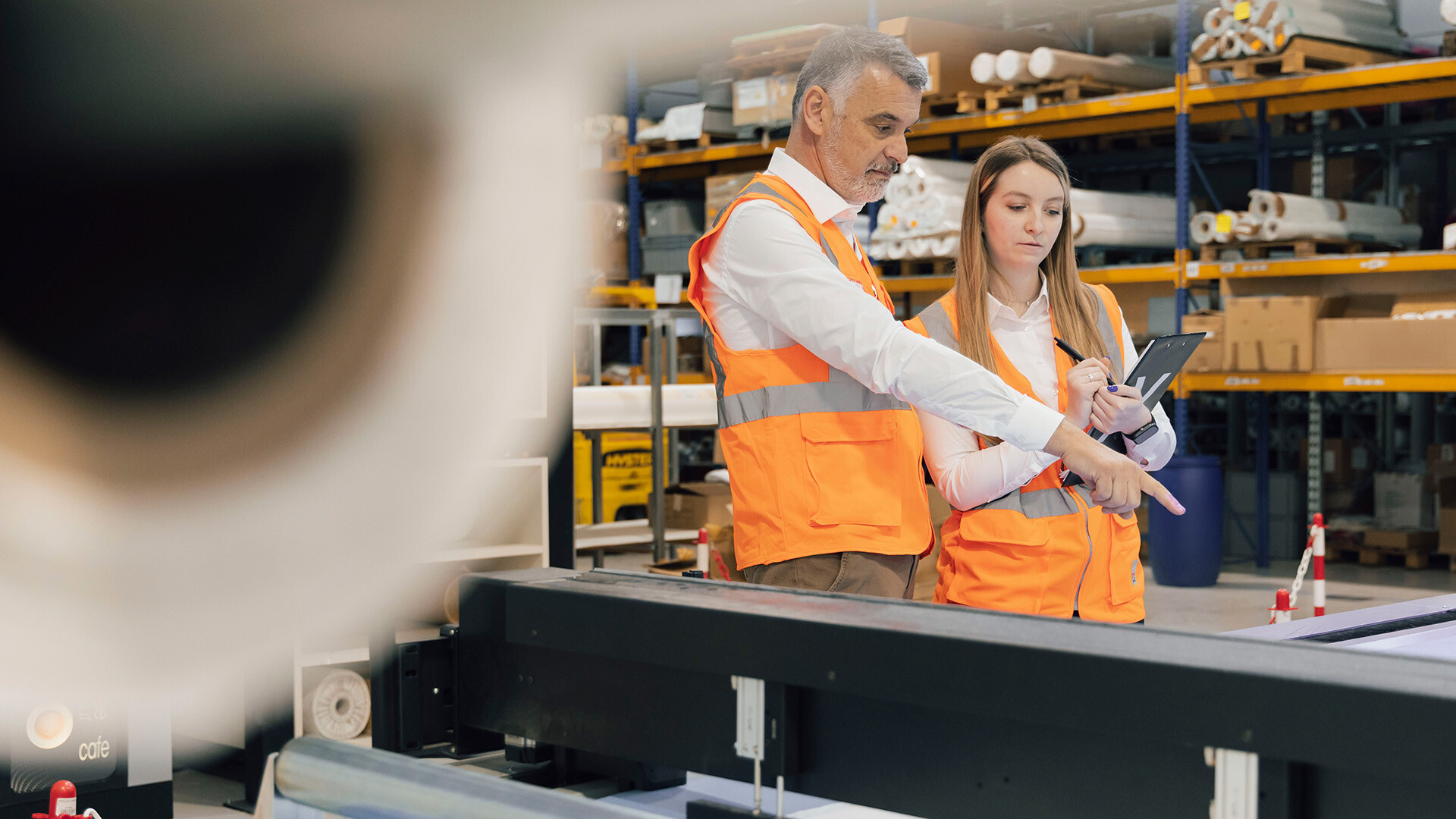
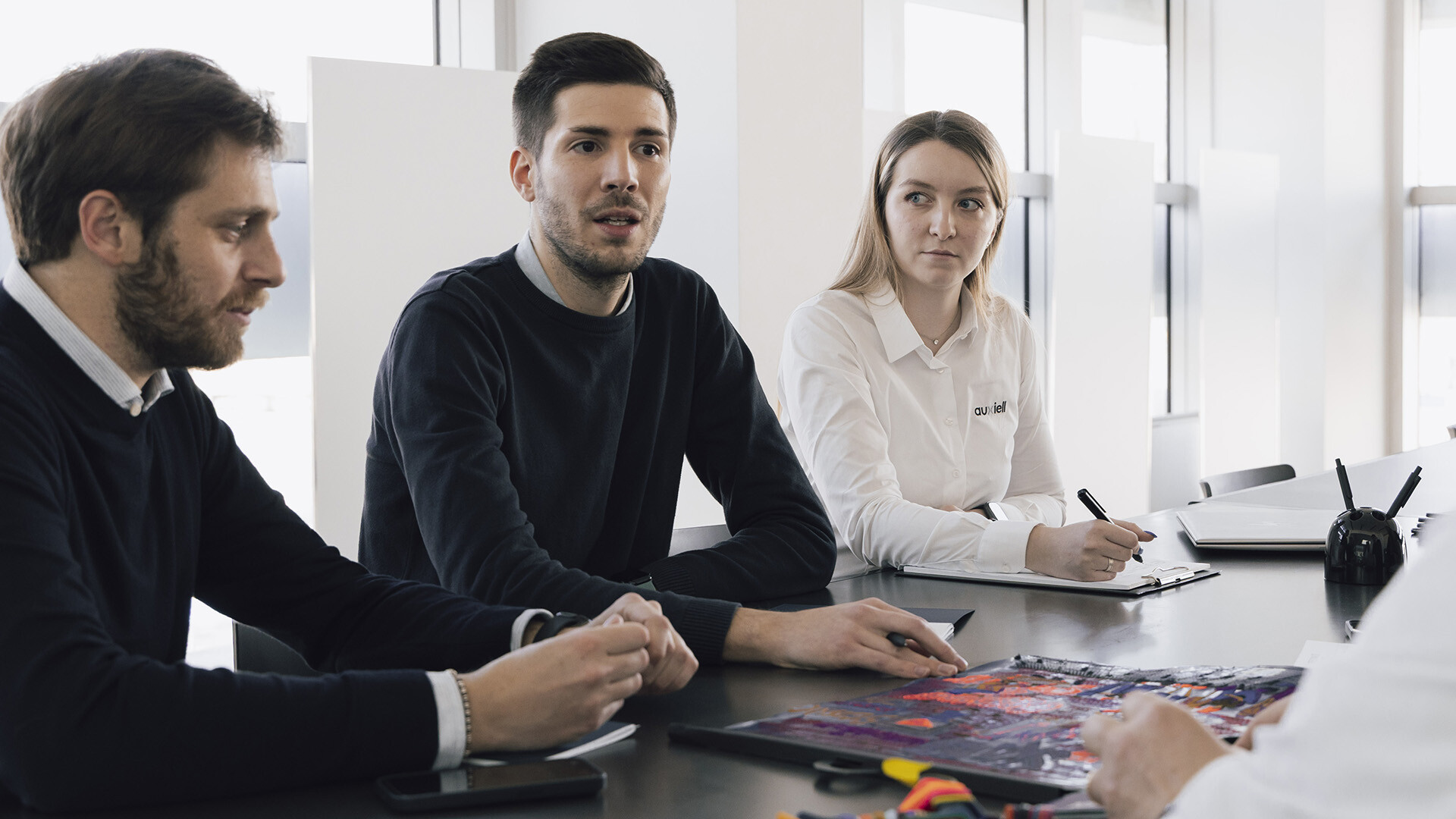
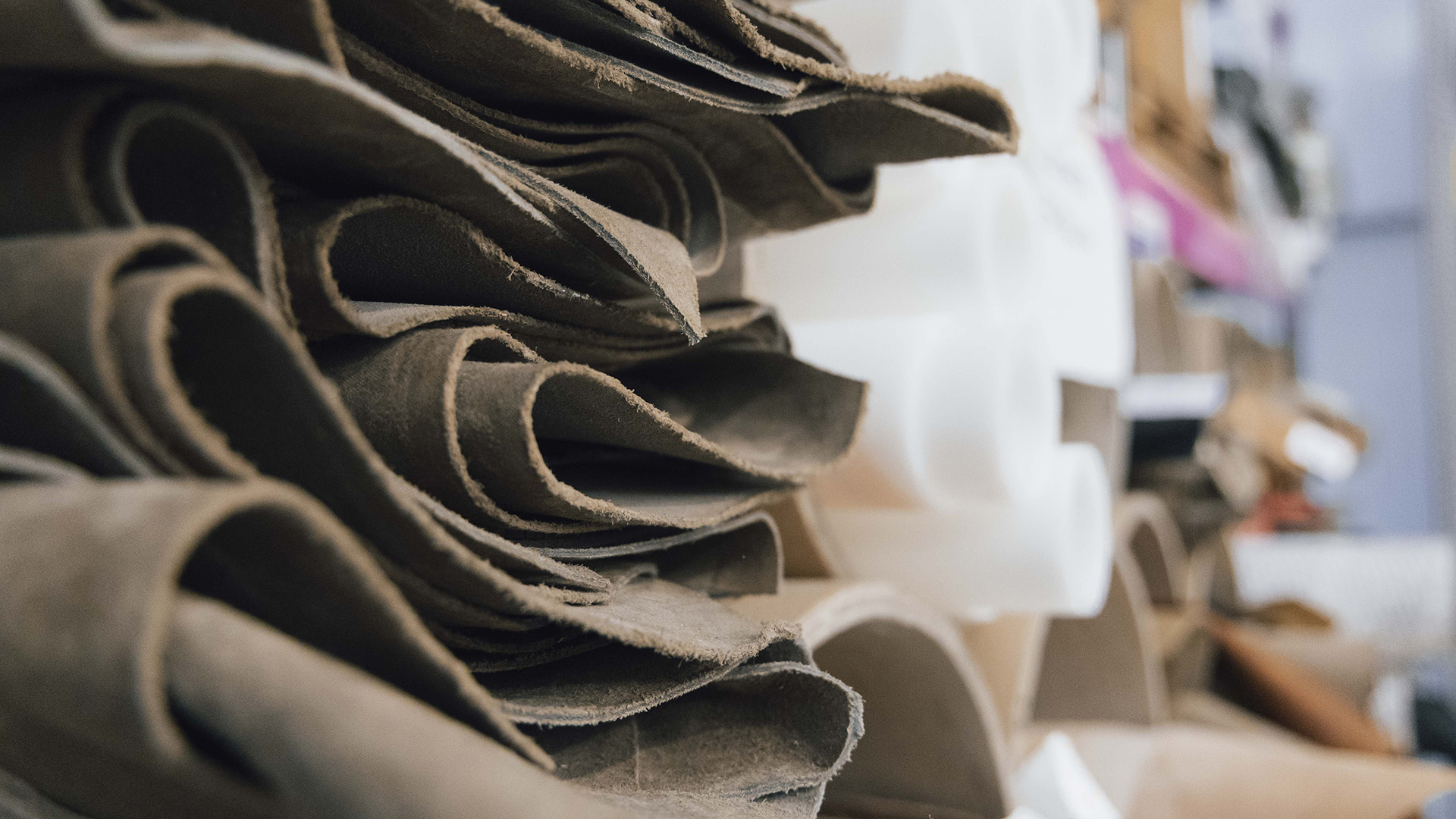
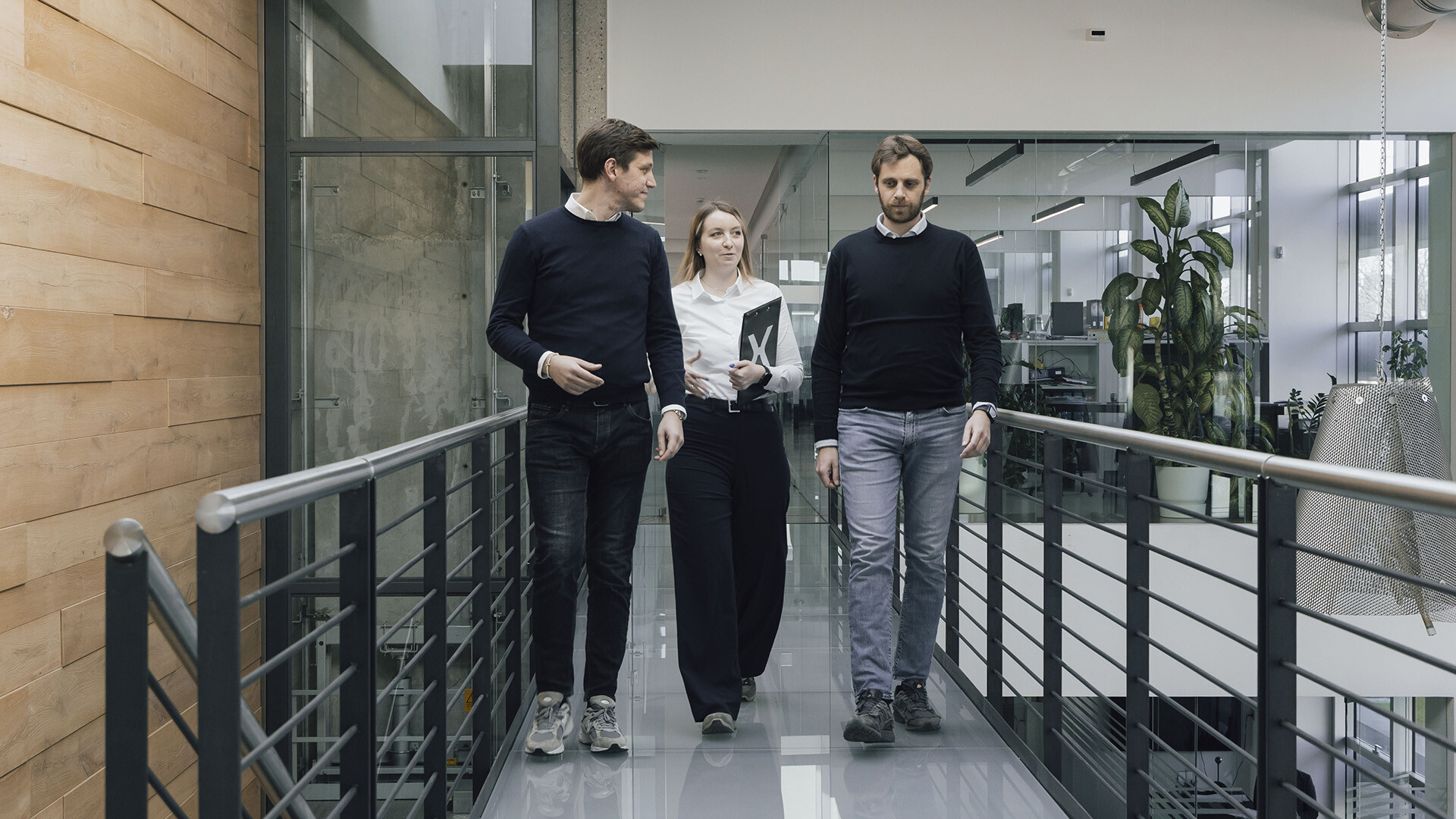
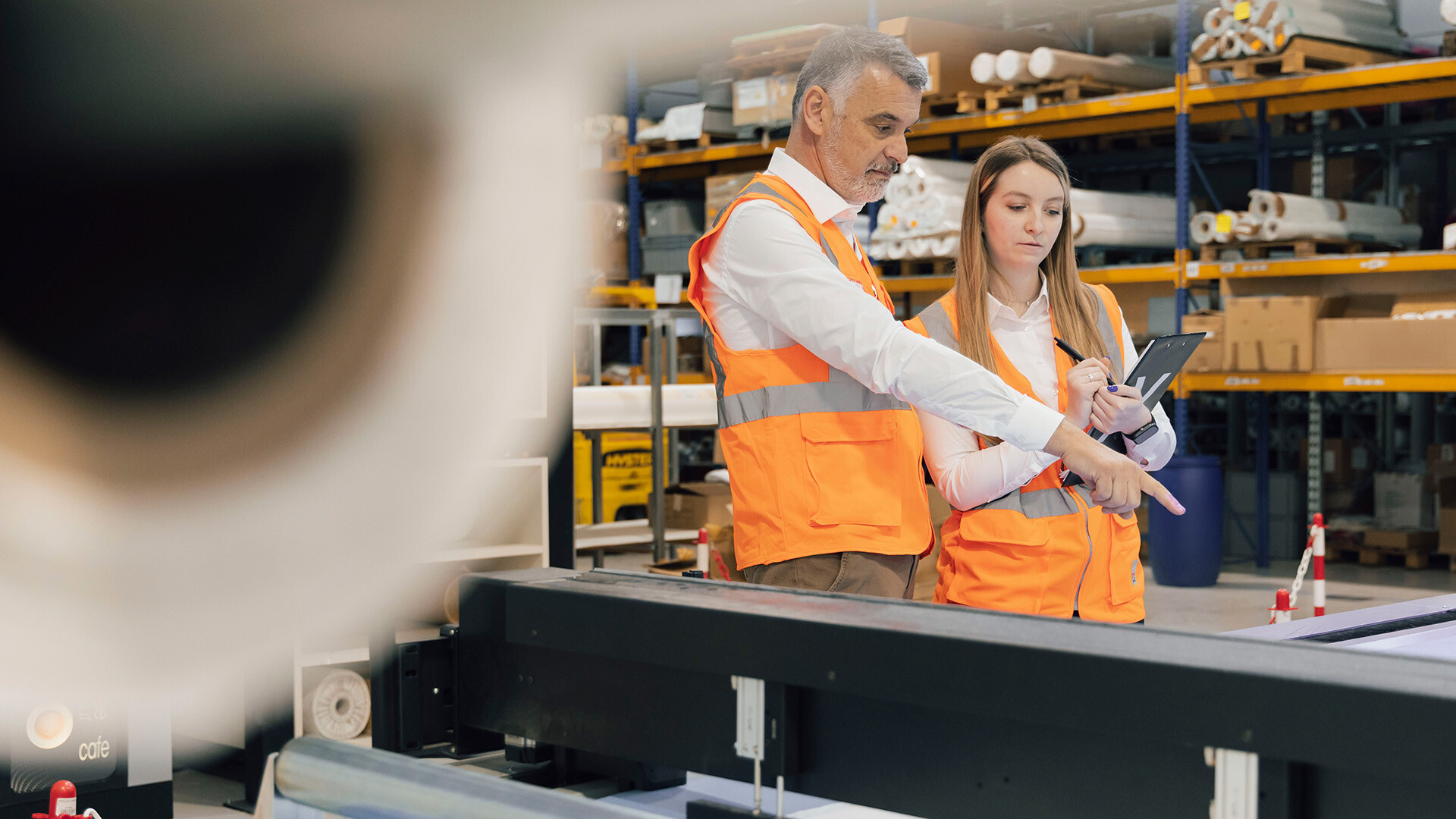
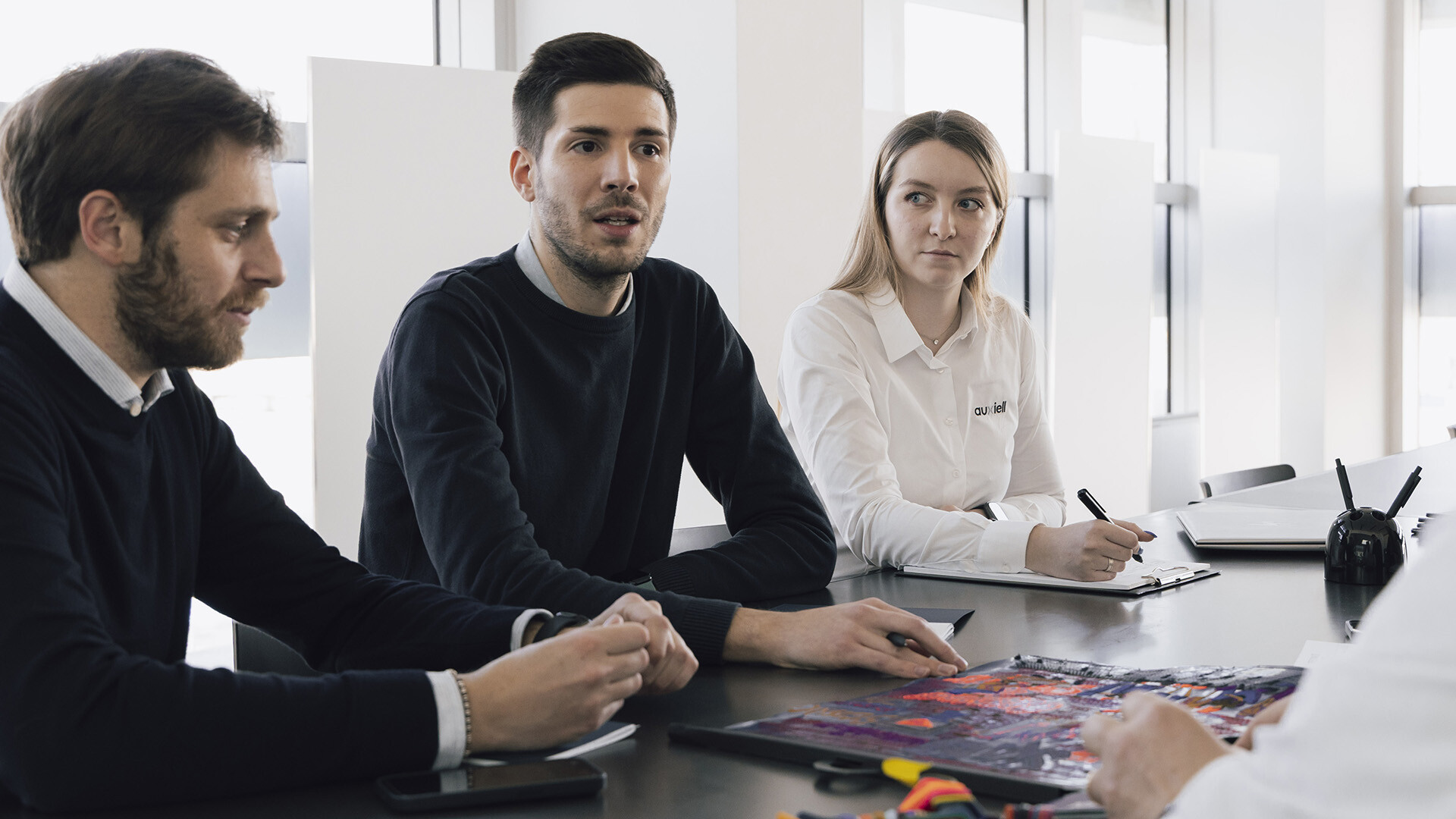
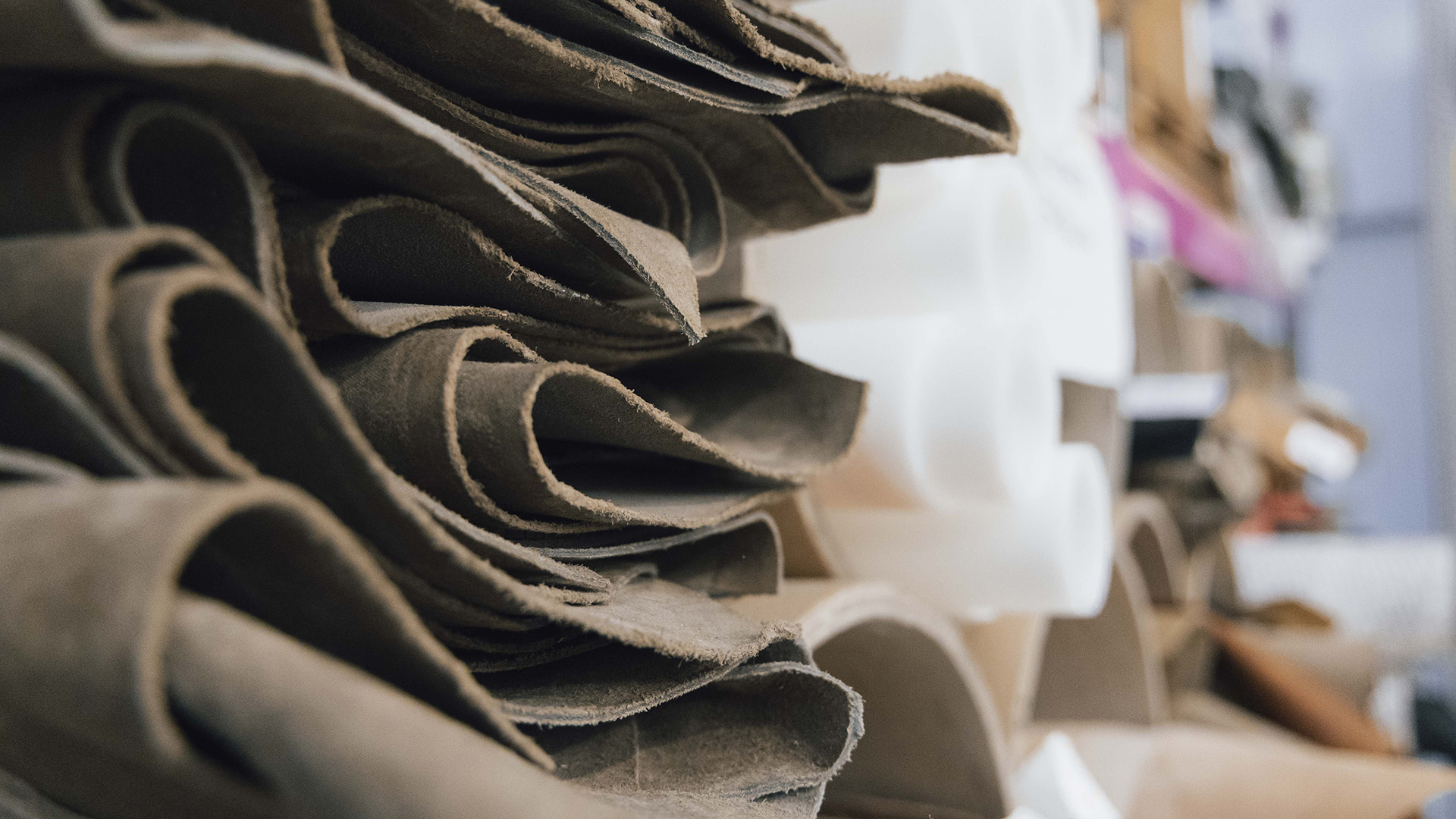
DO
Hoshin Kanri
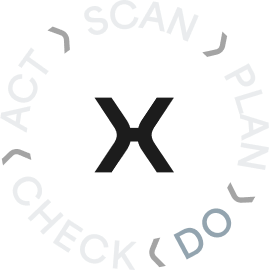
¿Qué actividades y técnicas lean nos han permitido alcanzar el objetivo establecido?
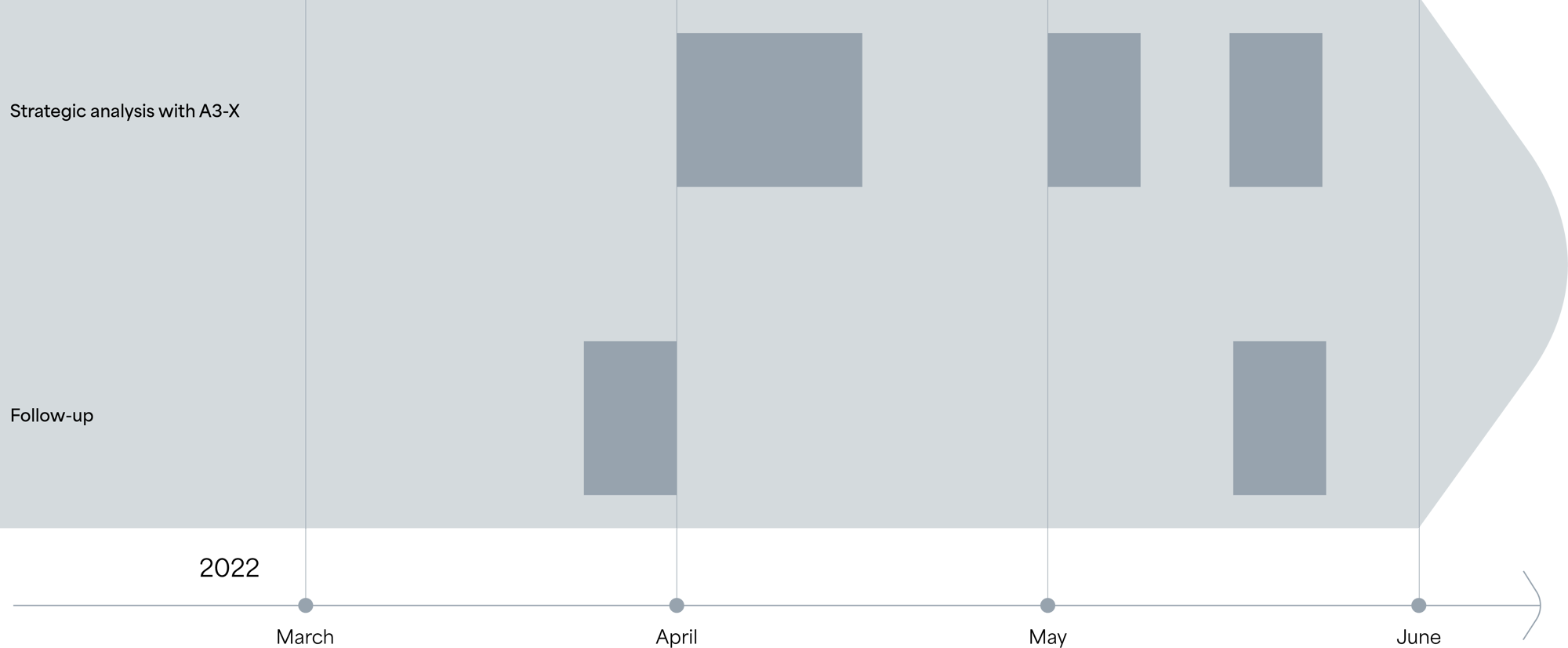
A3-X
En primer lugar se definieron las estrategias corporativas de la empresa. A partir de ellas, se definieron todos los grandes proyectos de la empresa y -mediante la correlación entre estrategia y proyecto- se priorizó la ejecución de cada proyecto sobre la base de una GANTT.
CHECK
¿Hemos alcanzado nuestros objetivos?
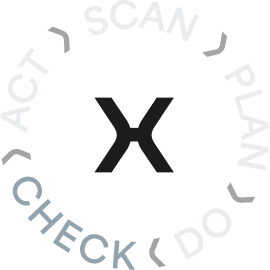
La optimización de la gestión estratégica se logró a través de A3-X, una herramienta que permitió seleccionar únicamente los proyectos prioritarios en línea con los objetivos corporativos, asignar equipos dedicados y definir indicadores clave de rendimiento. Este enfoque condujo a la normalización de las reuniones semanales de sprint "team hoshin" y a la realización de formación estratégica y alineación para todos los primeros niveles, lo que garantizó una mayor coherencia y concentración en los objetivos corporativos.
Ha aumentado el nivel de alineación de los proyectos con la estrategia corporativa.
Del Deployment a las Oportunidades Futuras
El proyecto en Deployment fue el que permitió sacar adelante todos los demás proyectos en las otras D, ahora analizados como alineados con la estrategia de la empresa.
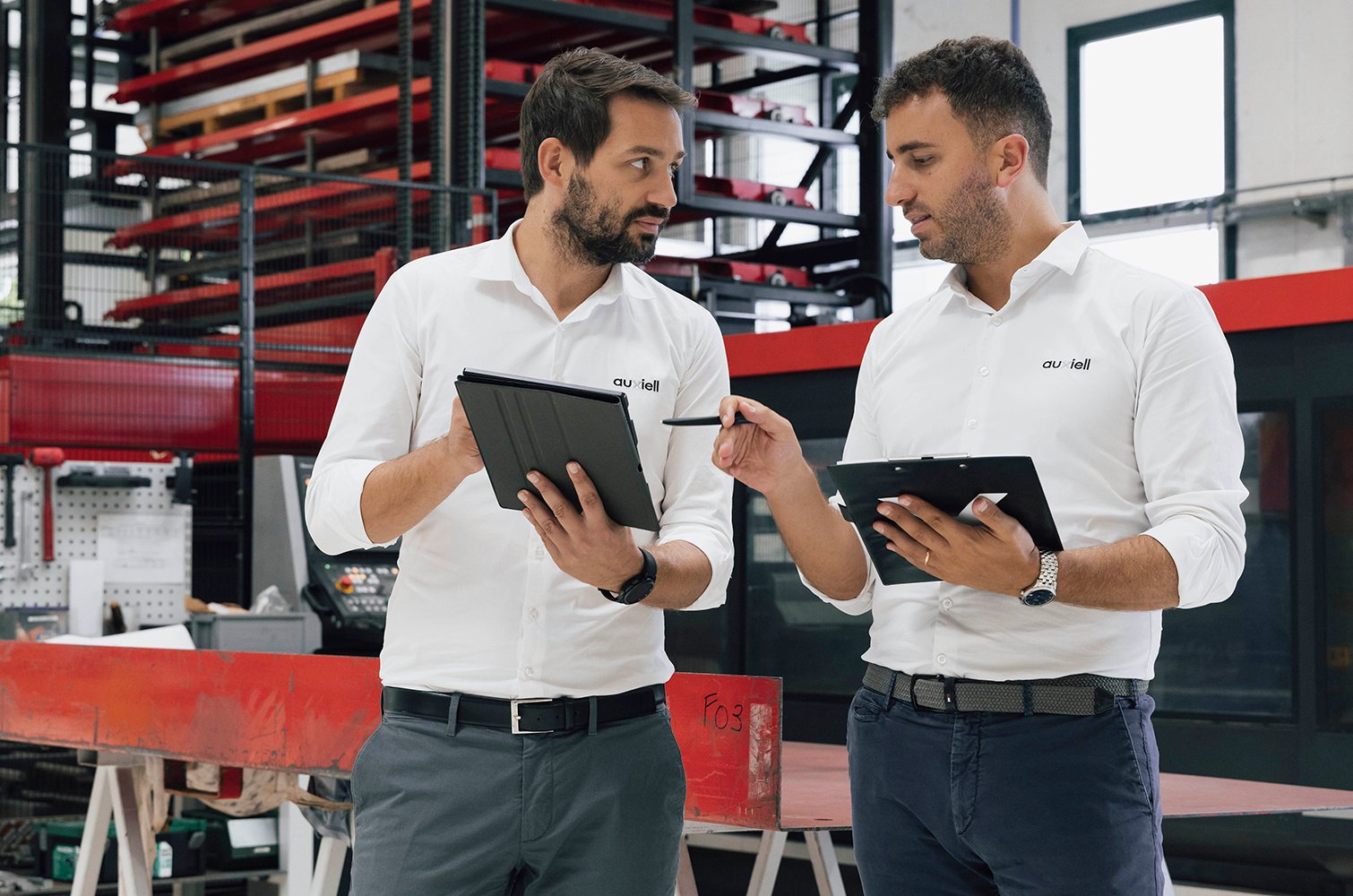
Nuestros expertos están disponibles para ayudarte en la transformación de los procesos
¡Suscríbete a nuestro boletín de noticias y recibe contenidos exclusivos, consejos prácticos y novedades directamente en tu bandeja de entrada!