11
Portfolio
Officina 3
Intro
Ridurre e standardizzare i lead time di attraversamento in un ambiente estremamente variabile attraverso l'introduzione di un prioritizzatore

Settore
Produzione e lavorazioni di accessori per l'alta moda
Sede
Padova, Italia
Per Officina 3 – azienda specializzata nella produzione e nella lavorazione di patch ed etichette per l'alta moda, l'abbigliamento, la calzatura e la pelletteria – la variabile tempo è fondamentale.
L’assenza di un’organizzazione strutturata rallentava i processi – in particolare quelli di campionatura e prototipazione, caratterizzati da un’elevata variabilità delle richieste – rendendo difficile rispettare le scadenze e garantire tempi certi di consegna.
Per migliorare l’efficienza operativa con l’azienda abbiamo avviato un percorso di riorganizzazione basato su metodologie lean. Da un’analisi approfondita sono state individuate le principali inefficienze, tra cui una gestione poco chiara delle priorità che causava rallentamenti nel flusso produttivo. Da qui la necessità di implementare un sistema pull che permettesse di lavorare solo sulla reale domanda, evitando sprechi di tempo e risorse. Parallelamente le fasi operative più critiche sono state standardizzate – grazie anche all’introduzione di un sistema di prioritizzazione – per garantire maggiore qualità e ridurre gli imprevisti.
Officina 3 ha così ridotto e stabilizzato il lead time nella campionatura e nella prototipazione migliorando la gestione delle richieste e la puntualità delle consegne. L’azienda può ora offrire ai brand di alta moda un servizio più affidabile ed efficiente, rafforzando il proprio ruolo di partner strategico in un settore dove rapidità e precisione sono determinanti.
Performance Raggiunte
0
0
lead time di attraversamento (dal lancio in produzione alla spedizione)
Filippo Fiorin
Direzione generale: Acquisti, Terzisti e Logistica - Officina 3
Giacomo Fiorin
Direzione generale: Commerciale, Sviluppo e Produzione - Officina 3
Martina Fior
Responsabile Produzione - Officina 3
Stefano Cesarotto
Programmazione della Produzione - Officina 3
Alessio Accardo
Responsabile Campionatura - Officina 3
Vuoi migliorare le performance della tua azienda?
Storia
azienda
2001
Officina 3 nasce nel 2001 come azienda italiana specializzata nella produzione e nelle lavorazioni di accessori per l'industria della moda, tra cui abbigliamento, calzatura e pelletteria.
Oggi
Fondata quasi vent'anni fa, l'azienda offre una gamma di prodotti che include patches, etichette, nastri, accessori e pannelli per borse, accessori e tomaie per la calzatura. Tutti i prodotti sono ideati, sviluppati e realizzati interamente in Italia, consentendo un controllo completo su ogni fase del processo produttivo, dalla prototipazione alla produzione finale.
Dipendenti (2023)
0Fatturato (2023)
0EBITDA (2023)
0
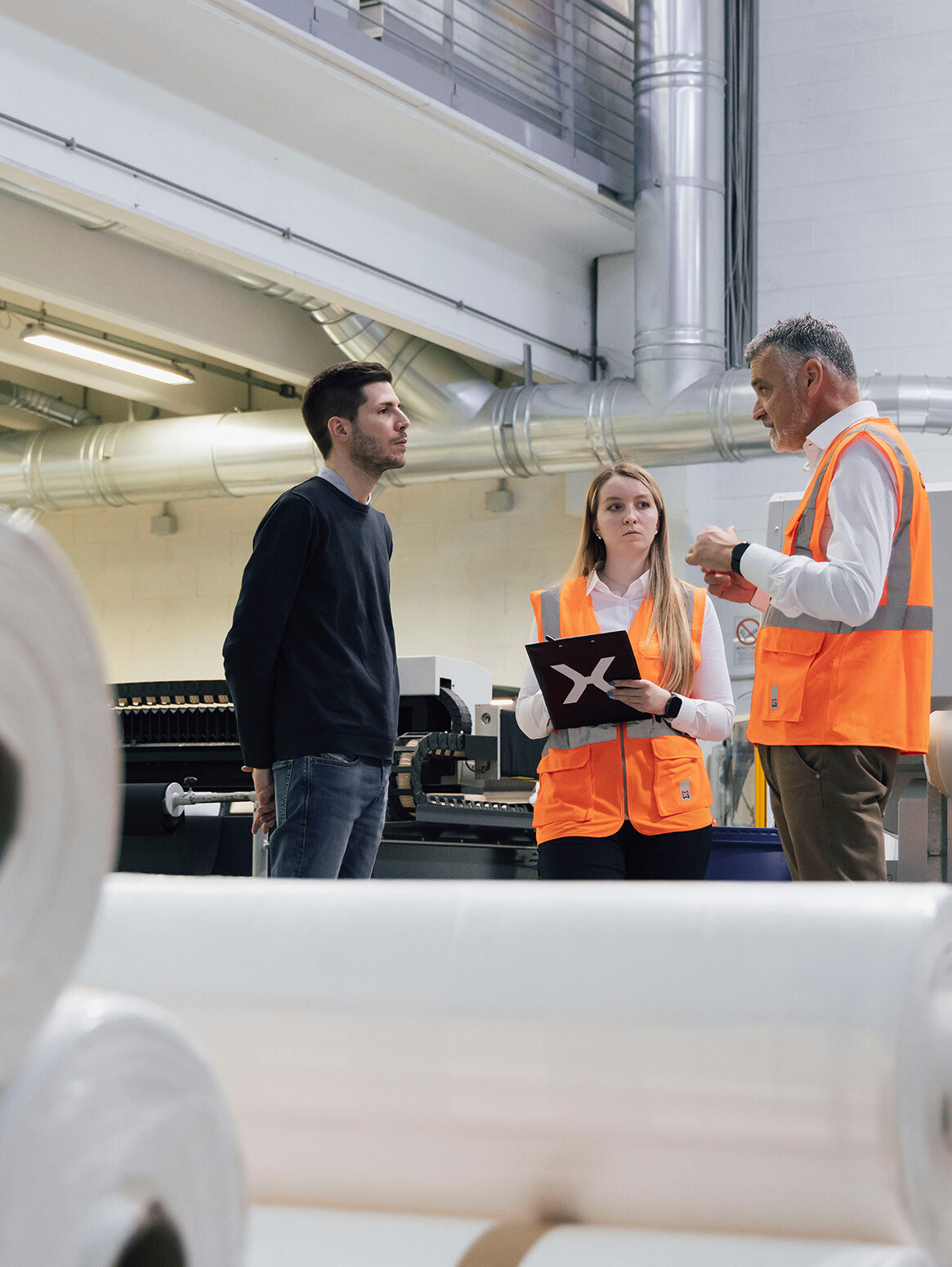
La sfida di Officina 3
La sfida di Officina 3 era gestire una domanda complessa – caratterizzata da un mix ampio di prodotti e volumi discontinui – all'interno di un processo produttivo articolato su molte fasi di lavorazione con elevata variabilità – riducendo il lead time per rispondere con maggiore prontezza alle esigenze del mercato.
Il punto di partenza
La trasformazione del primo macro-processo: Delivery
2020
Anno avvio collaborazione
con auxiell
Fine
Con Officina 3 abbiamo inizialmente intrapreso un progetto sul macro-processo di Delivery che comprende produzione, supply chain e gestione degli ordini.
Dopo aver lavorato nell'efficientamento dei processi di Delivery con il team Officina 3 abbiamo intrapreso un progetto sul macro-processo di Development che comprende lo sviluppo di nuovi prodotti e modifica degli stessi.
Dopo aver lavorato nell'efficientamento dei processi di Delivery e Development con il team Officina 3 abbiamo intrapreso un progetto sul macro-processo di Deployment che comprende la traduzione delle strategie in attività coordinate tra loro.
SCAN
Lean Gap Analysis® in Delivery
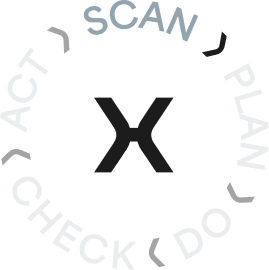
In virtù di un settore come quello del fashion in cui i prodotti hanno un ciclo di vita breve e sono fortemente legati a stagioni e collezioni del momento, la velocità è un fattore critico di successo. Il rispetto di un determinato lead time e la garanzia di produzione dei volumi richiesti fa la differenza nell'acquisizione di ordini da parte di grandi brand del settore.
Per analizzare lo stato corrente dei processi il team auxiell-Officina 3 si è quindi impegnato nella Lean Gap Analysis® del processo produttivo focalizzandosi sull'analisi e la riprogettazione delle diverse fasi di lavorazione quali taglio, taglio laser, incisione e incisione HP (high precision), incisione HF (high frequency), incisione piana/continua, serigrafia, accoppiamento, fustellatura, calandratura, accoppiatura, ricamo, iniezione e micro-iniezione.
Lean Gap Analysis®
Fase indispensabile per misurare e analizzare i processi attuali e definire i gap tra lo stato attuale e quello desiderato. In questa prima fase si va a “fotografare” lo stato corrente dei processi in termini di quantificazione degli sprechi, individuazione di eventuali problematiche e opportunità di miglioramento, nonché di tempificazione di tutte le fasi. Avere una visione chiara delle performance del processo è necessario per individuare le più corrette contromisure volte a rimuovere la causa radice del problema e progettare, in ottica futura, le attività da fare – e su quali KPI misurarsi – per efficientarlo.
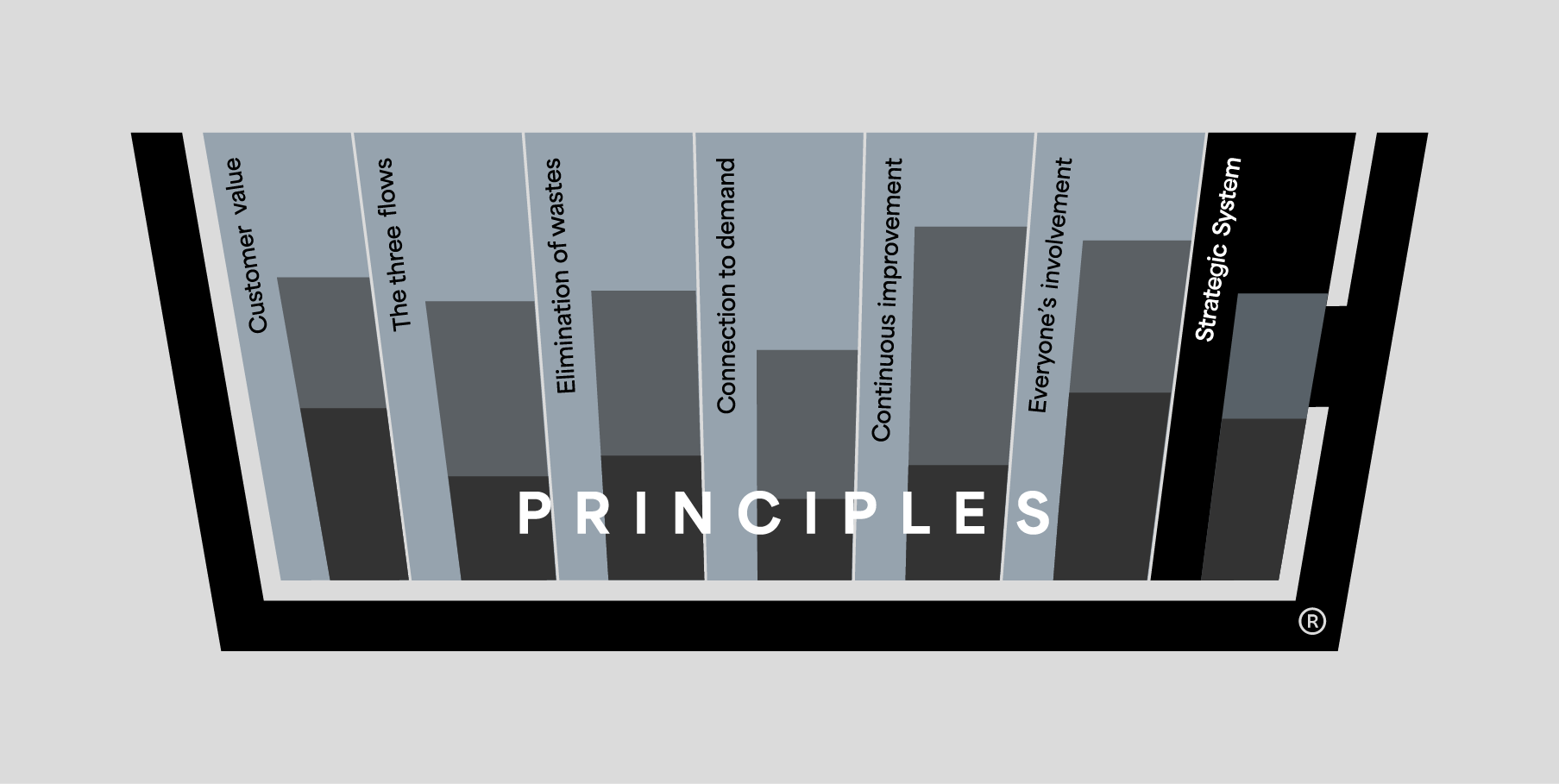
I gap emersi
01
Ritardi di consegna o consegne parziali dei prodotti finiti
L'alta variabilità nella produzione comportava tempi di produzione incerti che a volte comportavano ritardi nella consegna dei prodotti, contrattazioni di cambio data con il cliente e consegne parziali.
02
Scorte e wip elevati
Il lungo lead time di attraversamento - dall'ordine alla spedizione del prodotto finito - portava il cliente a richiedere continue modifiche con conseguente rischedulazione della produzione. Le "urgenze" nate dai cambi della pianificazione "sorpassavano" gli ordini in lavorazione. Inoltre i trasporti tra i reparti erano frequenti così come le attese causate da un sistema di produzione push basato sull'arrivo del materiale dalla fase a monte del processo piuttosto che "chiamato" dalla fase a valle.
03
Informazioni per il processo produttivo non corrette o incomplete
Le informazioni necessarie al corretto svolgimento delle operazioni che permettevano di realizzare il prodotto finito non sempre erano corrette o complete. Questo aumentava il rischio di errore perché lasciava discrezionalità operativa al caporeparto e/o all'operatore.
PLAN
Lean RoadMap® in Delivery
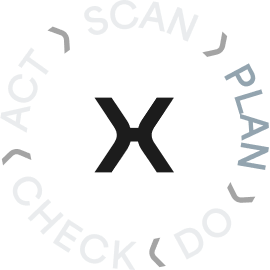
Una volta emersi i gap dalla Lean Gap Analysis® siamo passati alla fase successiva, ossia quella di PLAN. Attraverso la Lean RoadMap® abbiamo così definito la sequenza di implementazione delle più corrette tecniche lean che ci permettessero di raggiungere gli obiettivi concordati con il team Officina 3. La Lean RoadMap® identifica tecniche e metodi applicati nel corso del progetto.
Lean RoadMap®
Fase in cui si progetta lo stato futuro del processo analizzato in ottica multiscenario. Una volta scelto lo scenario più corretto dal punto di vista tecnico-economico si passa alla pianificazione del percorso da intraprendere per realizzarlo. Nella Lean RoadMap® emergono le attività su cui focalizzarci e le tempistiche con cui portarle a termine.
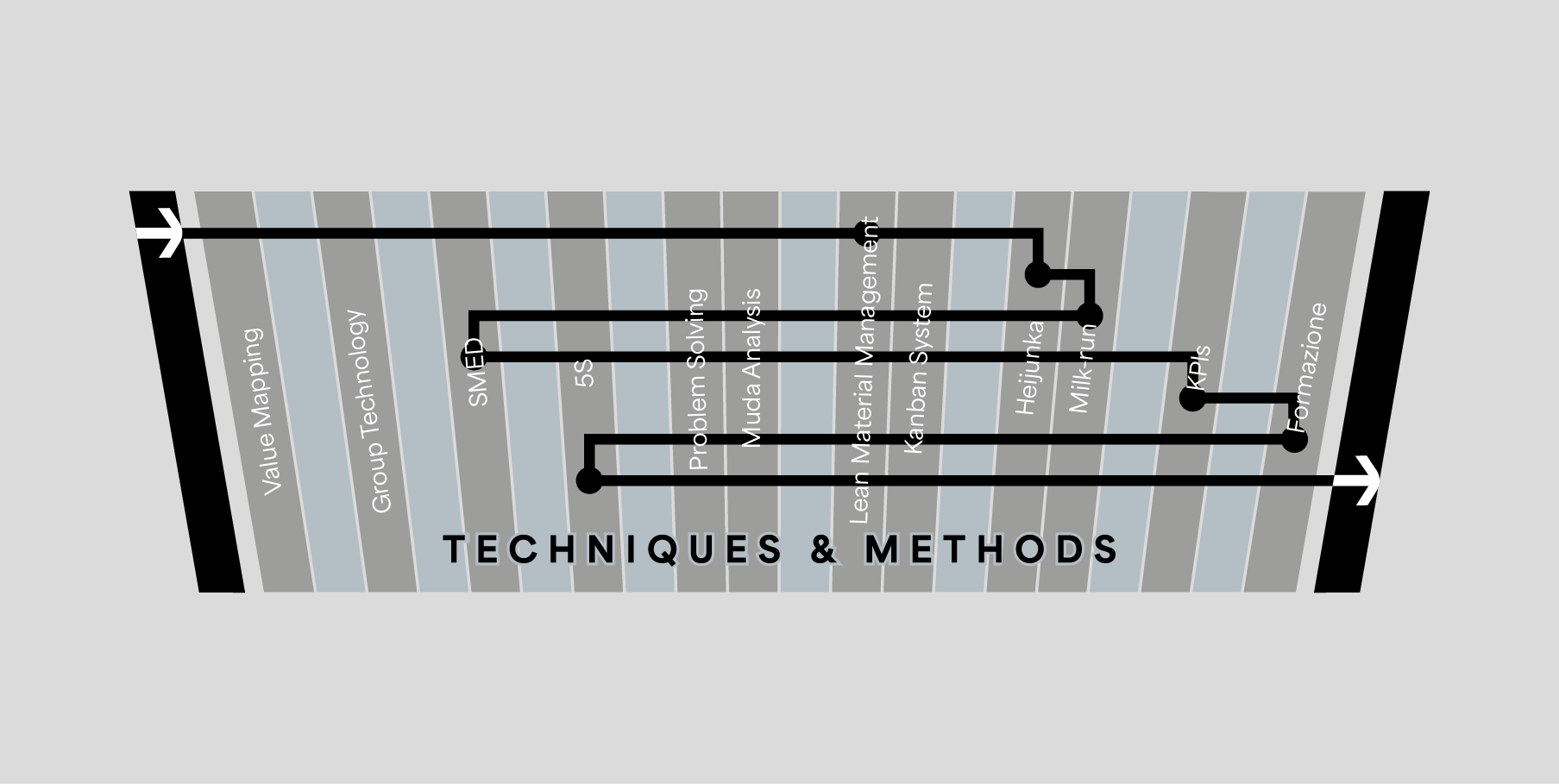
La direzione da percorrere
01
Introduzione di un prioritizzatore
Per ridurre i tempi di attraversamento in un processo produttivo con alta variabilità in termini di mix e volumi, è necessario collegare in pull le diverse fasi e definire criteri di priorità - dettata dalla capacità disponibile per produrre delle varie fasi - di lavorazione su ogni centro di lavoro.
02
Implementazione di un milk run
Per ridurre e stabilizzare il lead time sia dei fornitori di materia prima (calcolato dal momento dell'invio dell'ordine al momento di arrivo della merce) che dei terzisti (calcolato dal momento di invio del semilavorato al momento del rientro dello stesso a lavorazione compiuta). Un ulteriore beneficio del milk run è ridurre trasporti eccezionali e urgenti.
03
Applicazione della tecnica 5S
Per facilitare il coinvolgimento, la formazione e la polivalenza del team e portare la cultura dell'ordine sia in produzione, sia negli uffici.
04
Gestione della capacità produttiva
Per gestire al meglio i turni di produzione e assegnare correttamente le mansioni ai diversi operatori è stato introdotto un sistema di monitoraggio con identificazione dei picchi.
05
Creazione di una Skill Matrix
Per rendere il team polifunzionale e canalizzare la formazione verso le fasi di lavoro più critiche in termini di carico. Facilita inoltre l'assegnazione delle attività alle specifiche risorse a seconda delle loro conoscenze e competenze.
06
Kanban della materia prima
Per tenere controllato il livello di scorte di materia prima altorotante e allo stesso tempo evitare urgenze e rotture di stock.
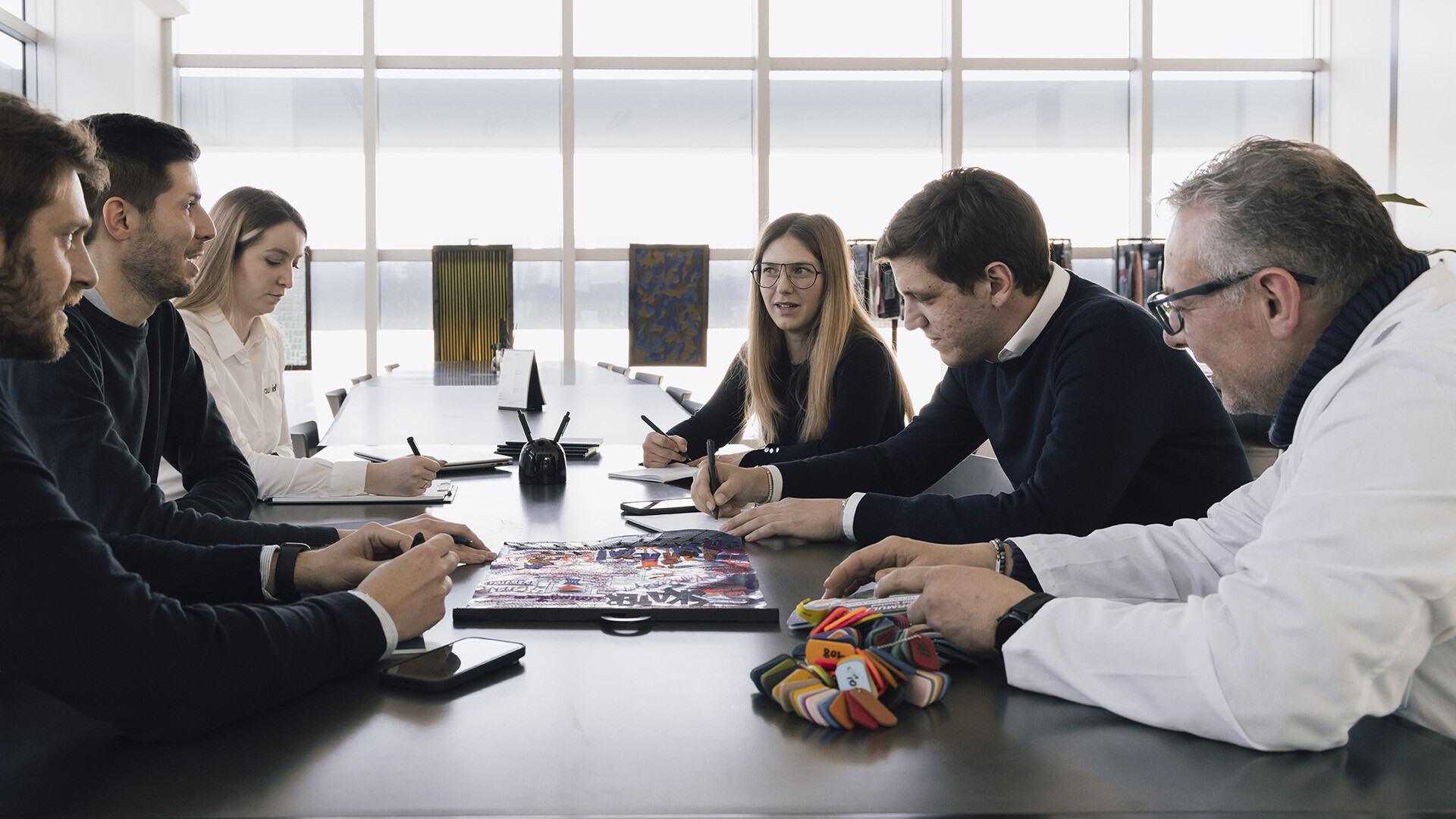
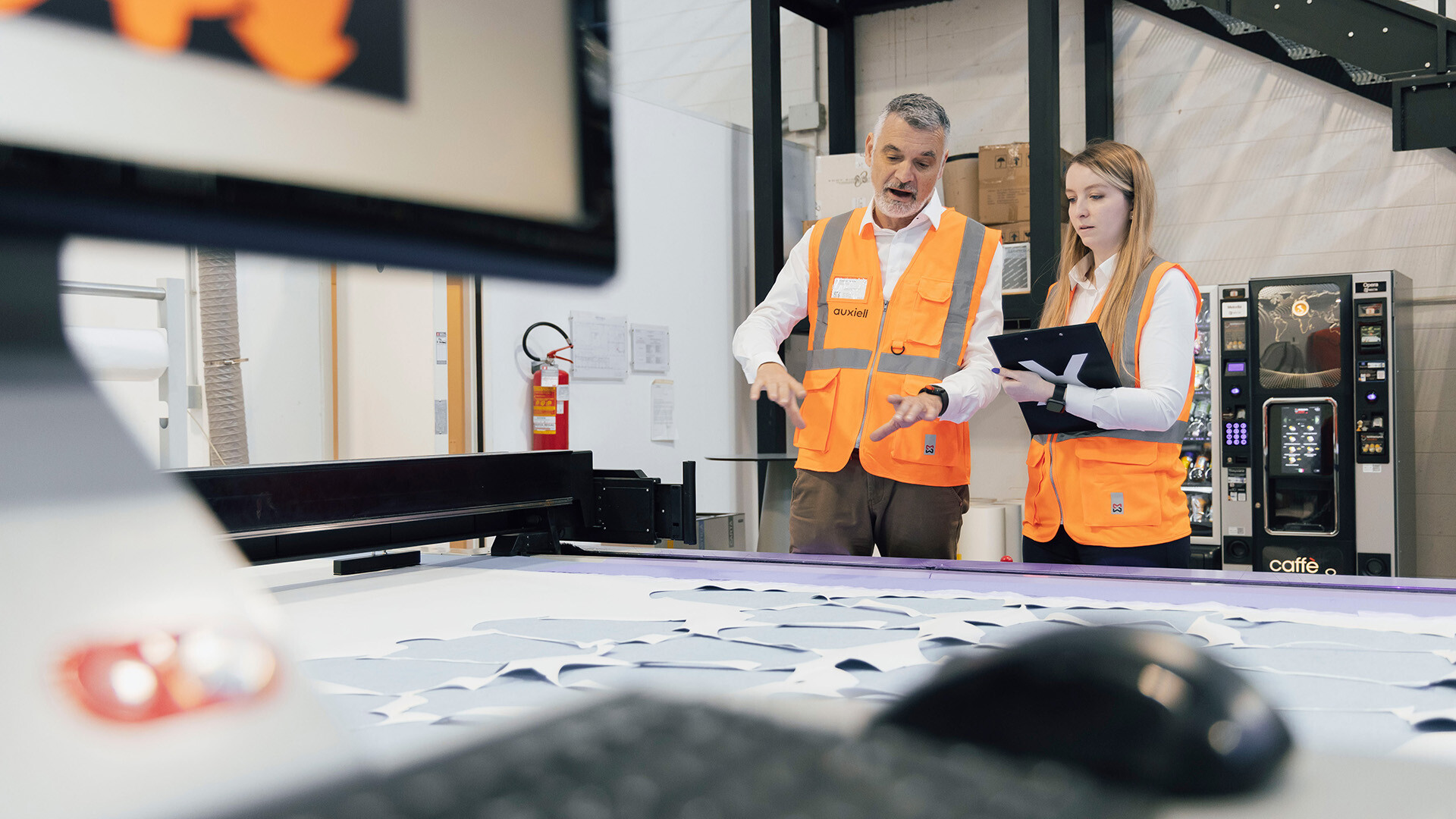
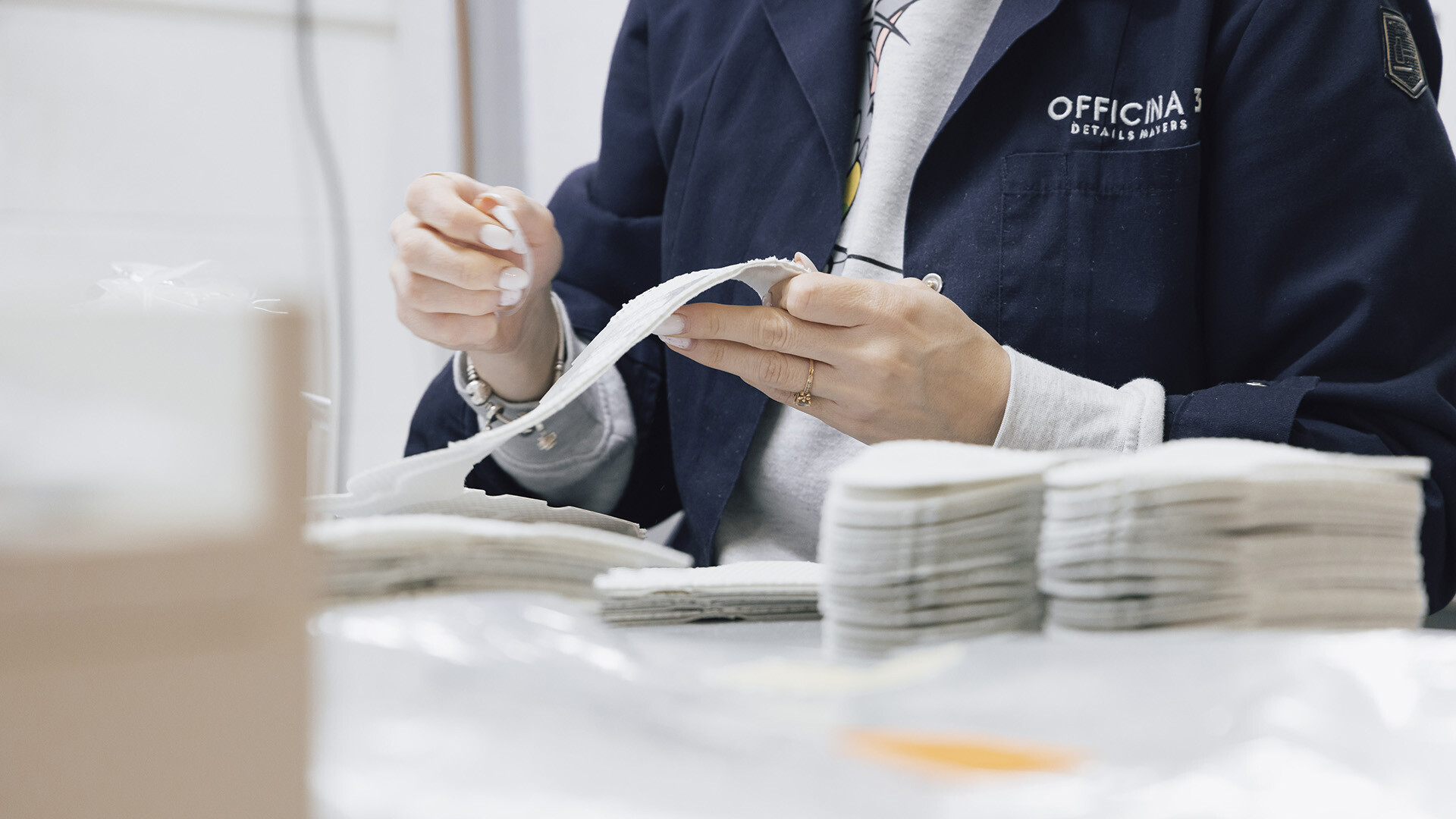
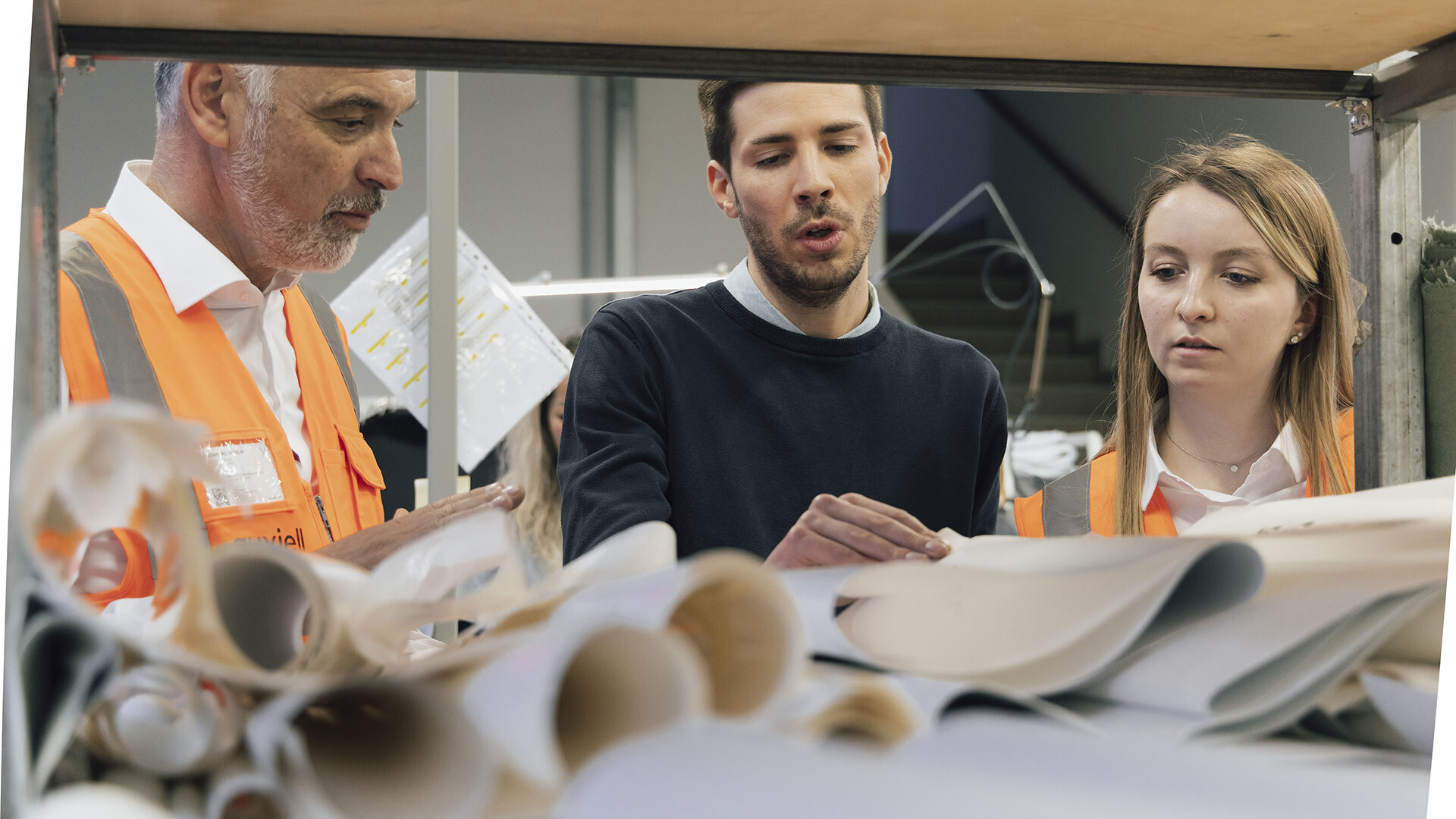
DO
Delivery Overall Transformation
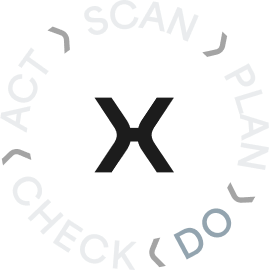
Quali attività e tecniche lean ci hanno permesso di raggiungere l’obiettivo stabilito?
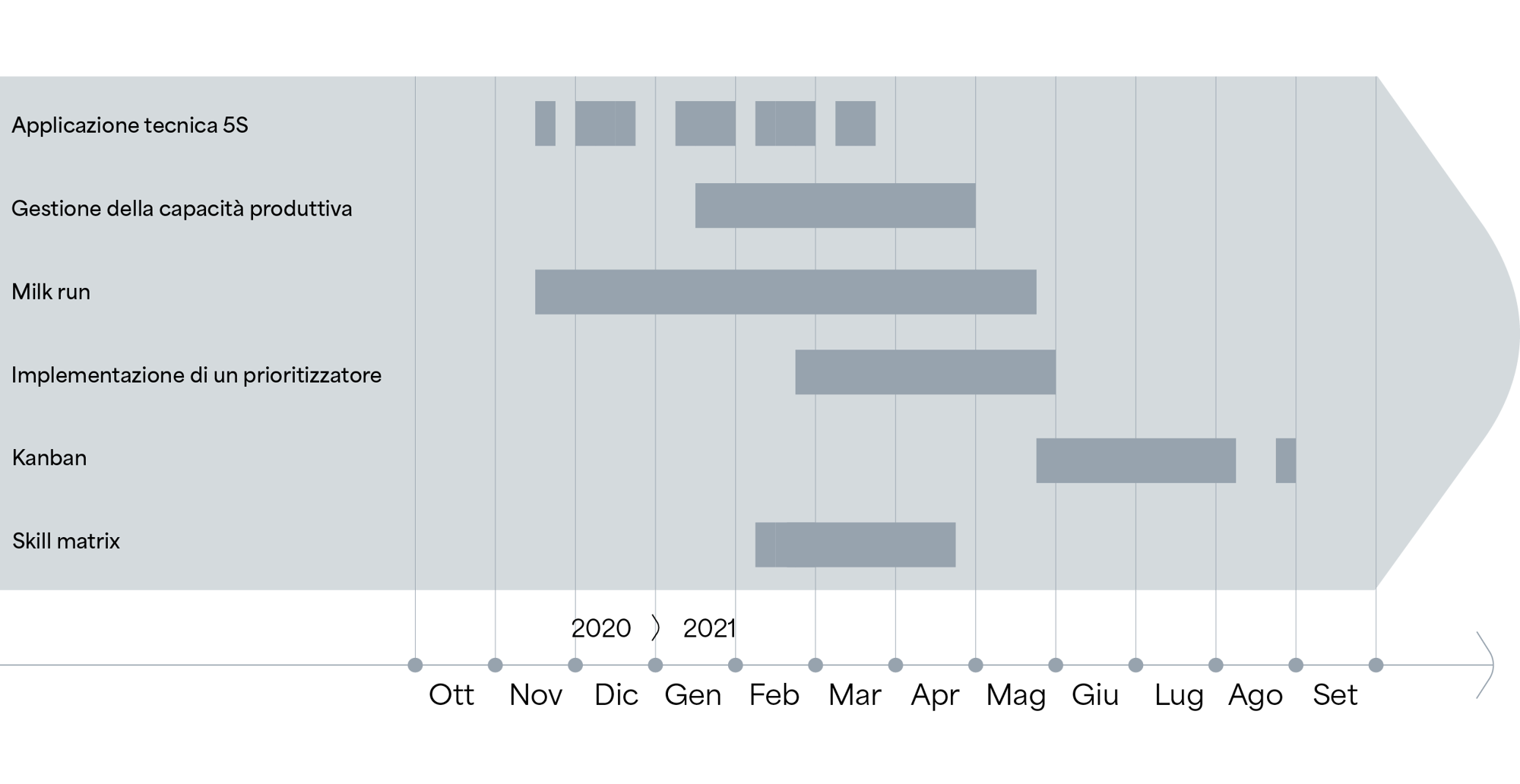
Implementazione di un prioritizzatore
Con l'impiego di lavagna e cartellini è stato sviluppato uno strumento ad hoc per regolare e monitorare la quantità di materiale tra i centri in ottica pull. Nello specifico, per realizzare tale strumento sono stati dapprima mappati quali fossero i centri di lavoro e le loro caratteristiche (distanze o similitudini tra lavorazioni). In secondo luogo, a ciascun centro è stato attribuito un certo numero di cartellini kanban rappresentativi della capacità produttiva. è stata poi installata una lavagna mostrando in riga i centri di lavorazione e in colonna i tempi in termini di slot orari e settimane. I singoli incroci sono poi utilizzabili per inserirci i cartellini kanban. La tabella - chiamata prioritizzatore - segnala quale sia il centro di lavorazione più scarico in uno specifico momento e quindi da alimentare con priorità. Il prioritizzatore, infatti, illustra la capacità libera dei centri di lavoro.
Milk run
Un milk run "flessibile" è stato implementato per il ritiro dei materiali da fornitori/terzisti che prevede sia delle tappe standard prestabilite, sia delle tappe "al bisogno" dettate dalle necessità produttive.
Applicazione della tecnica 5S
Sono stati attivati sette workshop di applicazione della tecnica delle 5S che includevano sia formazione teorica che applicazione pratica in specifiche postazioni di lavoro (sia in produzione che negli uffici) che hanno permesso di creare e mantenere un ambiente pulito e ordinato e di formare il team affinché fosse poi autonomo nel replicare la tecnica. Ogni figura del team Officina 3 è stata coinvolta e ha accolto l'attività con entusiasmo. Le postazioni di lavoro riprogettatte in ottica 5S hanno permesso di raccogliere feedback positivi da parte di clienti in visita e di estendere l'attività anche ad aziende terziste.
Gestione della capacità produttiva
La gestione delle code tramite il prioritizzatore ha permesso di stabilizzare i lead time delle fasi e quindi di prevedere il carico di lavoro giornaliero per ogni centro così da intervenire nel caso in cui questo fosse superiore al carico massimo di lavoro. L'effetto finale è un flusso produttivo che scorre senza interruzioni.
Skill matrix
Per ogni risorsa è stato mappato il livello di conoscenza e competenza relativo a ogni lavorazione. Queste informazioni, unite al fabbisogno produttivo per gli specifici centri di lavoro, hanno permesso di definire un livello di polivalenza obiettivo. La formazione effettuata dai capireparto ai vari operatori era quindi "tirata" dall'obiettivo di polivalenza stabilito e focalizzata sulle competenze critiche. In ultima istanza è stato implementato un processo di misurazione periodica del livello di polivalenza delle figure per capire lo stato di avanzamento sui livelli stabiliti.
Kanban della materia prima
Per i codici di materie prime altorotanti è stato calcolato il quantitativo ottimale da tenere a stock in funzione del consumo previsto e del lead time di approvvigionamento. A ogni unità è stato attaccato un cartellino kanban che, all'esaurimento, attiva il processo di ripristino del materiale.
CHECK
Abbiamo raggiunto gli obiettivi stabiliti?
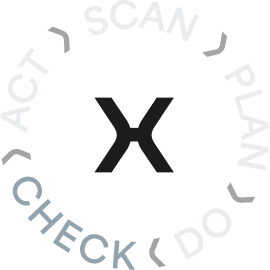
Il tempo di attraversamento dal lancio in produzione alla spedizione si è risotto del 46%.
Limitare movimenti superflui e percorsi lunghi ha contribuito a ridurre l’affaticamento e il rischio di infortuni per gli operatori, migliorando la sicurezza e il comfort durante le attività quotidiane. Un ambiente più ergonomico favorisce inoltre una maggiore concentrazione e un clima di lavoro più positivo, con ricadute dirette sulla motivazione e sulla soddisfazione del personale.
L’ottimizzazione dei processi produttivi in ambito Delivery ha permesso a Officina 3 di garantire tempi di consegna più stabili e prevedibili, riducendo ritardi e inefficienze. La maggiore affidabilità nelle tempistiche ha rafforzato la relazione con i brand di alta moda, che possono contare su un partner capace di rispondere con precisione e rapidità alle loro esigenze.
Dal Delivery al Development
A seguito dei risultati ottenuti e dell’elevato coinvolgimento riscontrato nel miglioramento del macro-processo di Delivery, il team di Officina 3 ha avviato in autonomia nuove iniziative, applicando le competenze acquisite durante la trasformazione. Il miglioramento delle performance nel Delivery ha spinto l’azienda a estendere l’ottimizzazione anche al macro-processo di Development, confermando l’impegno verso un’evoluzione continua e una gestione sempre più efficiente dei processi.
SCAN
Lean Gap Analysis® in Development
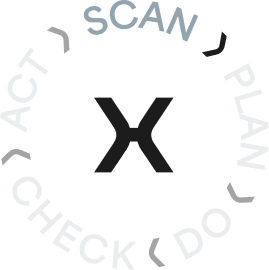
Ridurre e stabilizzare il lead time in campionatura e prototipazione era una priorità. Se i tempi di consegna sono fondamentali per la produzione in serie, lo diventano ancora di più quando si tratta di sviluppare prototipi e campioni, dove rapidità e precisione fanno la differenza.
Lean Gap Analysis®
Fase indispensabile per misurare e analizzare i processi attuali e definire i gap tra lo stato attuale e quello desiderato. In questa prima fase si va a “fotografare” lo stato corrente dei processi in termini di quantificazione degli sprechi, individuazione di eventuali problematiche e opportunità di miglioramento, nonché di tempificazione di tutte le fasi. Avere una visione chiara delle performance del processo è necessario per individuare le più corrette contromisure volte a rimuovere la causa radice del problema e progettare, in ottica futura, le attività da fare – e su quali KPI misurarsi – per efficientarlo.
I gap emersi
01
Ritardi e puntualità per il mondo campioni e prototipi
Similmente a quanto emerso nel macro-processo di Delivery, anche nel Development i tempi di consegna dei campioni sono critici. Anche in questo caso, quindi, sono stati registrati ritardi o consegne urgenti.
PLAN
Lean RoadMap® in Development
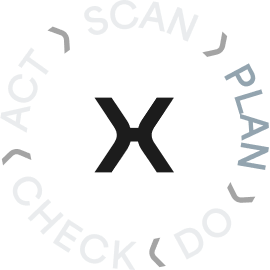
Una volta emersi i gap dalla Lean Gap Analysis® siamo passi alla fase successiva, ossia quella di PLAN. Attraverso la Lean RoadMap® abbiamo così definito la sequenza di implementazione delle più corrette tecniche lean che ci permettessero di raggiungere gli obiettivi concordati con il team Officina 3. La Lean RoadMap® identifica tecniche e metodi applicati nel corso del progetto.
Lean RoadMap®
Fase in cui si progetta lo stato futuro del processo analizzato in ottica multiscenario. Una volta scelto lo scenario più corretto dal punto di vista tecnico-economico si passa alla pianificazione del percorso da intraprendere per realizzarlo. Nella Lean RoadMap® emergono le attività su cui focalizzarci e le tempistiche con cui portarle a termine.
La direzione da percorrere
01
Progettazione di un Heijunka
Per livellare i carichi di lavoro nelle macchine di campionatura e pianificare correttamente la produzione nel rispetto delle date richieste dal cliente è stato implementato un Heijunka Board all'ingresso dell'area di campionatura.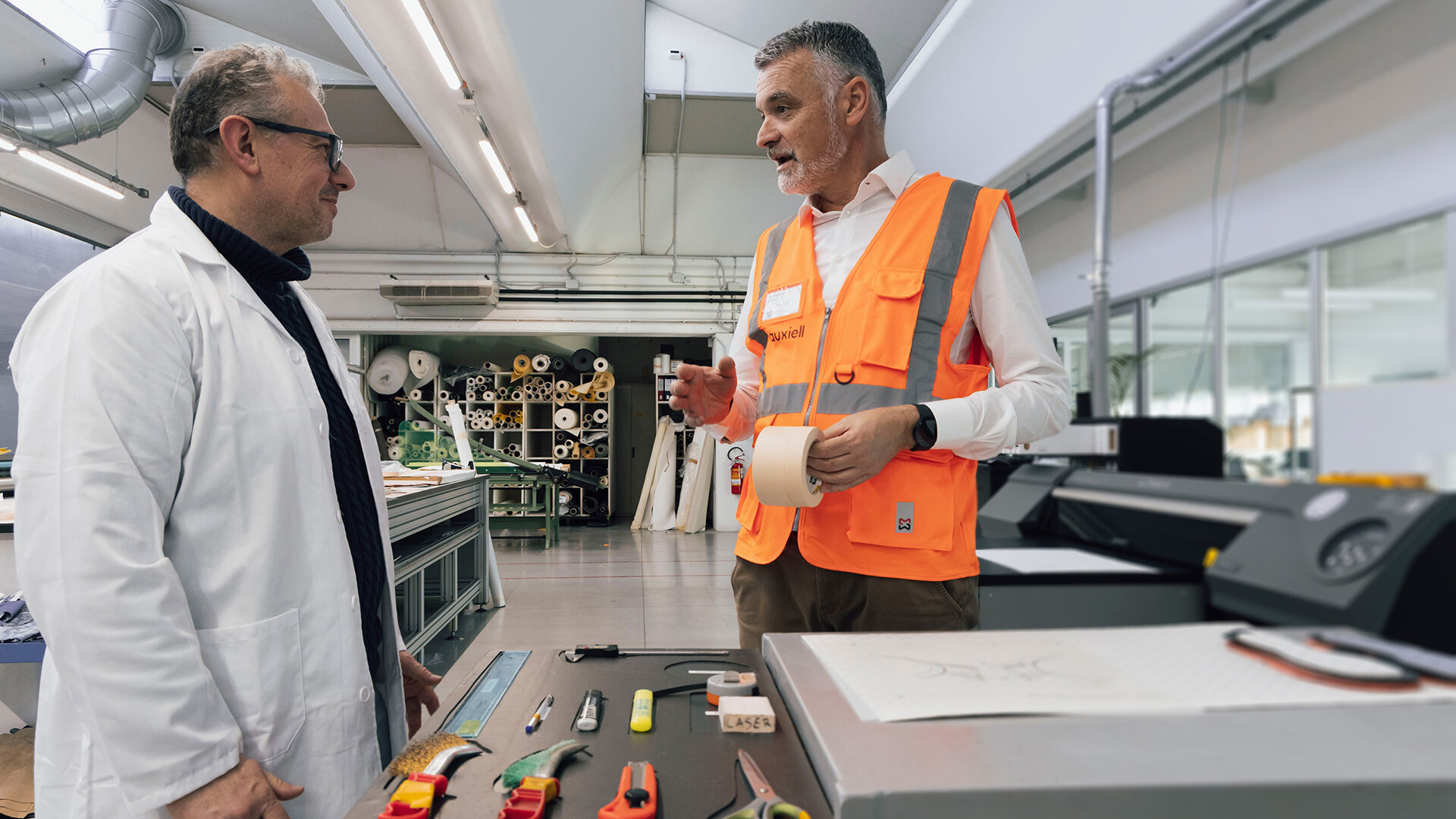
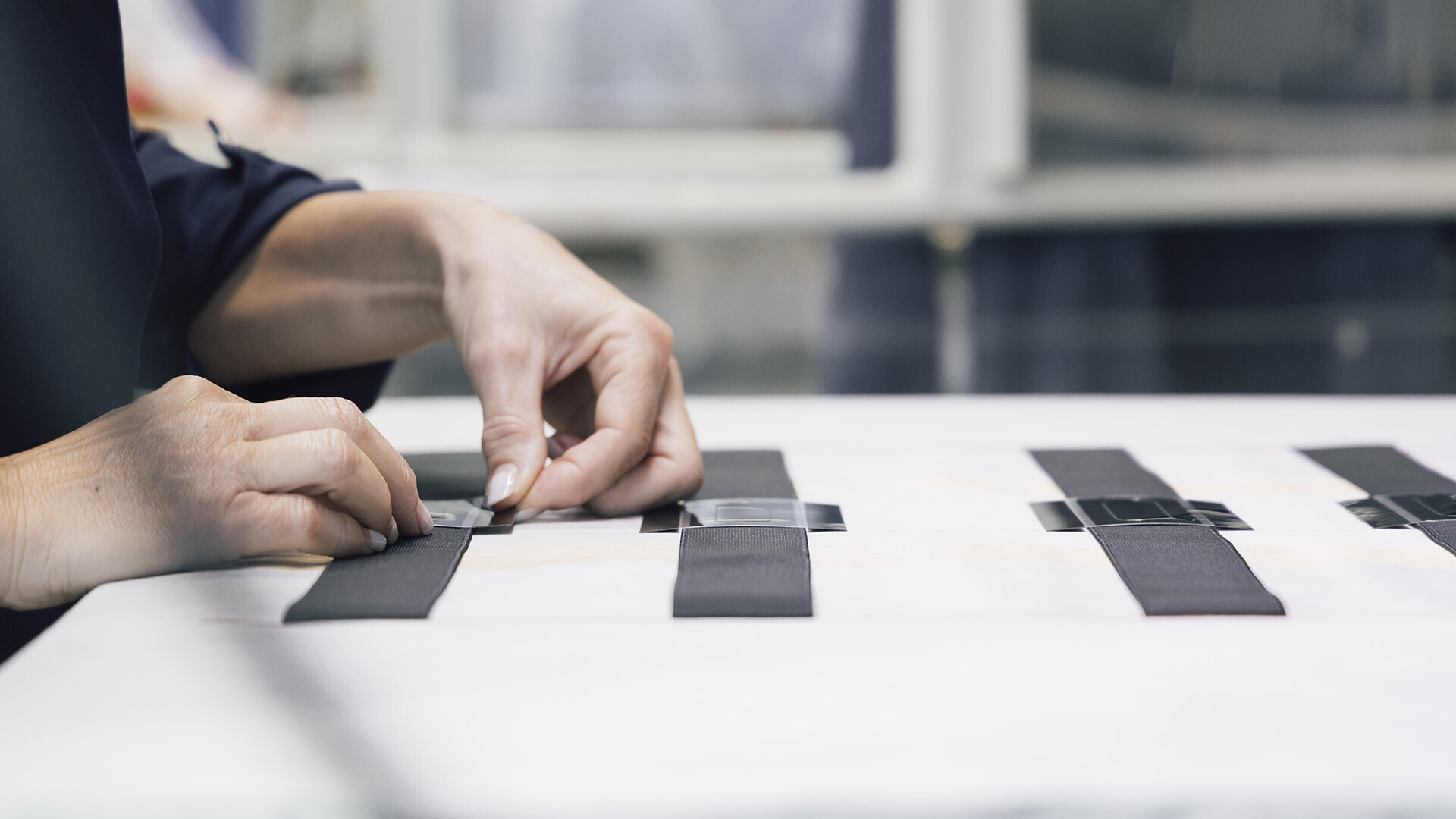
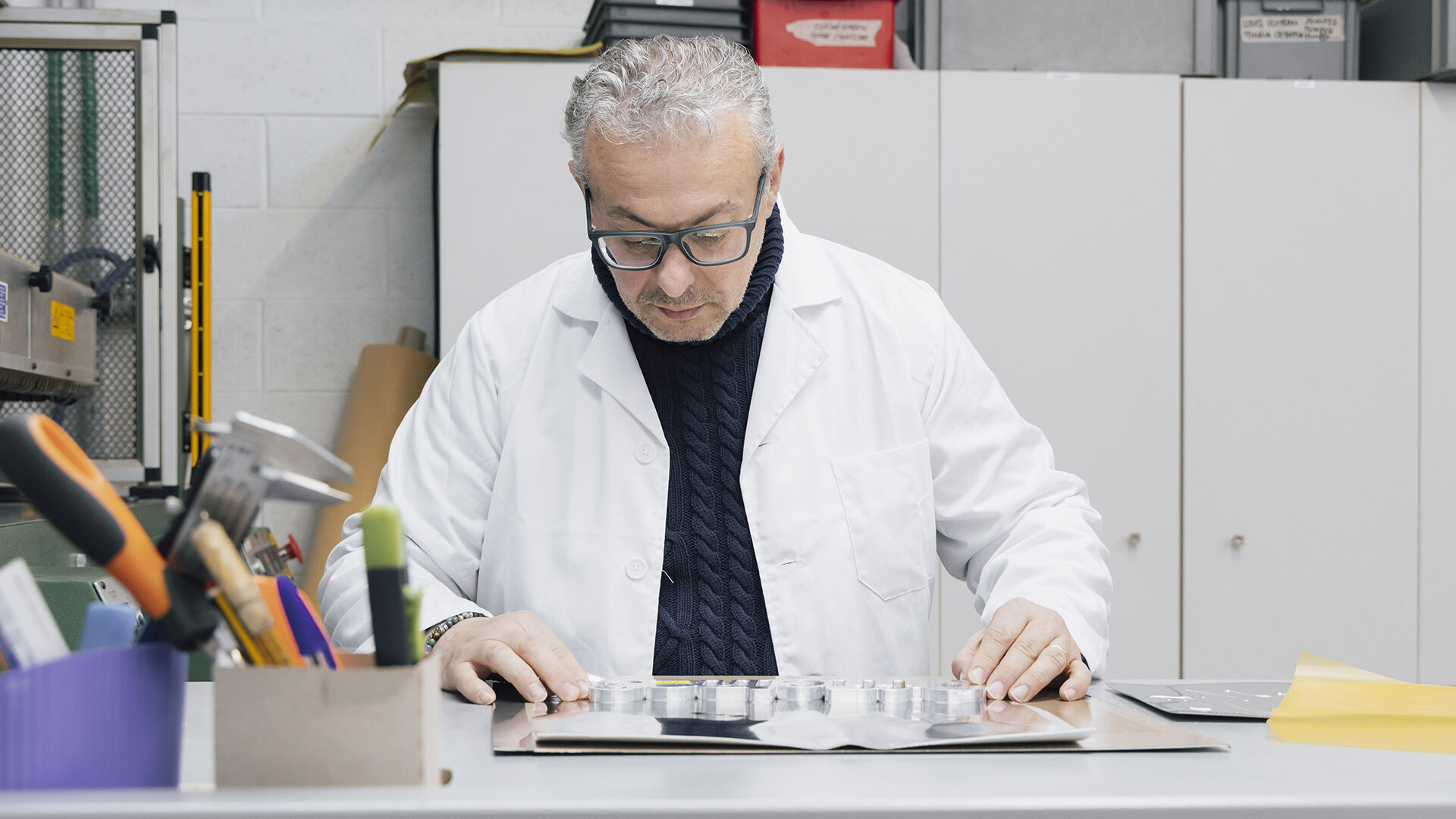
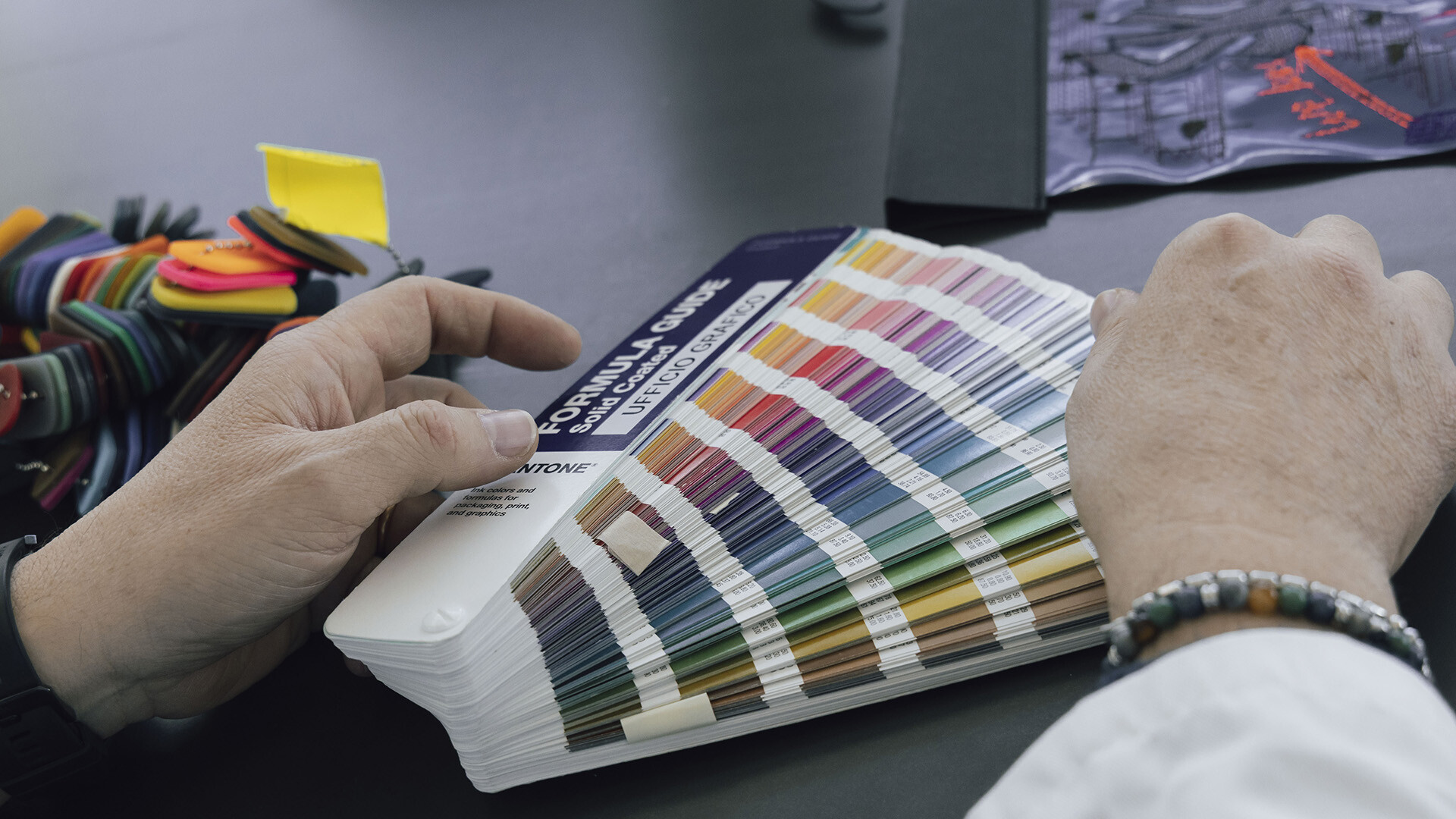
DO
Design for Simplification
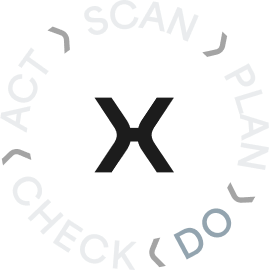
Quali attività e tecniche lean ci hanno permesso di raggiungere l’obiettivo stabilito?
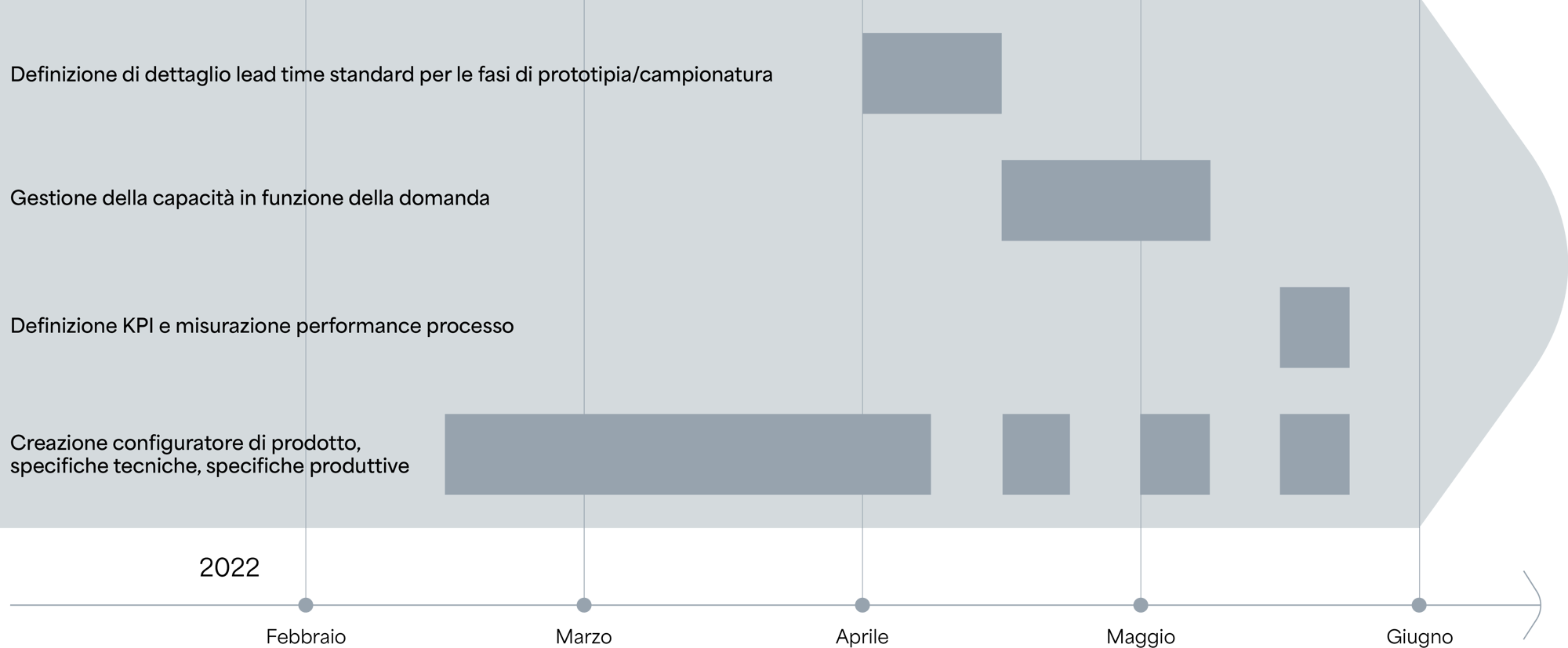
Implementazione dell'Heijunka
Sono state identificate le fasi di lavoro del processo di campionatura e raccolti i dati su vincoli e tempi ciclo. Attraverso l'implementazione di una visual board è stato possibile dare visibilità della pianificazione agli operatori in campionatura che permettesse loro di organizzare materiali e attrezzature con il giusto anticipo. Per questo motivo è fondamentale una gestione ordinata dei materiali nell'area. All'Heijunka di pianificazione è stato quindi affiancato un visual management a pavimento: il materiale previsto in lavorazione per un dato giorno era posizionato nello spazio dedicato. Questo ha permesso di eliminare il tempo di ricerca del materiale da parte degli operatori.
CHECK
Abbiamo raggiunto gli obiettivi stabiliti?
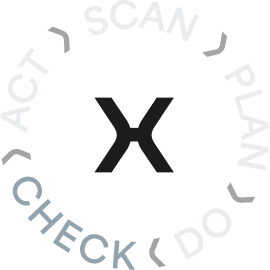
L'attività di creazione degli strumenti quali Heijunka Board e Visual Management a pavimento è stata implementata in autonomia dal team di Officina 3 con competenza e proattività sfruttando le nozioni apprese durante la trasformazione del processo di Delivery.
Grazie a una gestione più chiara delle priorità e all’introduzione di un sistema pull, la campionatura e la prototipazione seguono ora un flusso più lineare, senza interruzioni o accumuli.
L’implementazione dell’Heijunka ha migliorato la gestione della campionatura, assicurando una pianificazione chiara e strutturata. La visual board ha dato visibilità alle attività, permettendo di organizzare materiali e attrezzature in anticipo, mentre il visual management a pavimento ha eliminato i tempi di ricerca. Il team di Officina 3 ha applicato questi strumenti in autonomia, consolidando le competenze acquisite nella trasformazione del processo di Delivery. Il risultato è un flusso più lineare, senza interruzioni o accumuli, grazie a una gestione efficace delle priorità e all’introduzione di un sistema pull.
Dal Development al Deployment
Grazie ai risultati ottenuti e all’elevato coinvolgimento nel miglioramento del macro-processo di Development, il team di Officina 3 ha intrapreso autonomamente nuove iniziative, applicando le competenze acquisite durante la trasformazione.
Un esempio concreto è stata l’adozione indipendente degli strumenti di Heijunka e Visual Management, dimostrando capacità di gestione e spirito proattivo. L’ottimizzazione del Development ha spinto l’azienda a estendere l’intervento anche al macro-processo di Deployment, rafforzando l’efficienza operativa e la continuità del miglioramento.
SCAN
Lean Gap Analysis® in Deployment
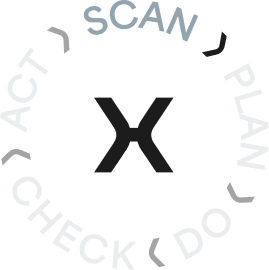
L’azienda, specializzata nel supporto ai brand di alta moda, aveva la necessità di riorganizzare la propria strategia per migliorare l’efficienza operativa. La velocità e la variabilità delle richieste rendevano complesso gestire le attività in modo strutturato, creando difficoltà nel definire le priorità e ottimizzare i flussi di lavoro. Per rispondere a questa esigenza, è stato avviato un percorso di riorganizzazione volto a mettere ordine nei processi, garantendo maggiore rapidità di esecuzione e una gestione più efficace delle attività. L’obiettivo era rafforzare il posizionamento dell’azienda come partner di riferimento per il settore dell’alta moda.
Lean Gap Analysis®
Fase indispensabile per misurare e analizzare i processi attuali e definire i gap tra lo stato attuale e quello desiderato. In questa prima fase si va a “fotografare” lo stato corrente dei processi in termini di quantificazione degli sprechi, individuazione di eventuali problematiche e opportunità di miglioramento, nonché di tempificazione di tutte le fasi. Avere una visione chiara delle performance del processo è necessario per individuare le più corrette contromisure volte a rimuovere la causa radice del problema e progettare, in ottica futura, le attività da fare – e su quali KPI misurarsi – per efficientarlo.
I gap emersi
01
Assenza di priorità sui progetti da intraprendere
Gli obiettivi strategici erano chiari al management e alla proprietà ma non era chiara la priorità e la frequenza di attuazione dei singoli progetti in relazione agli obiettivi da raggiungere.
PLAN
Lean RoadMap® in Deployment
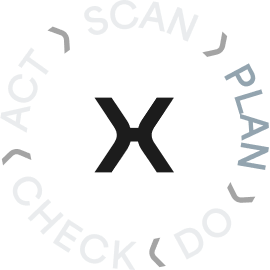
Una volta emersi i gap dalla Lean Gap Analysis® siamo passati alla fase successiva, ossia quella di PLAN. Attraverso la Lean RoadMap® abbiamo così definito la sequenza di implementazione delle più corrette tecniche lean che ci permettessero di raggiungere gli obiettivi concordati con il team Officina 3. La Lean RoadMap® identifica tecniche e metodi applicati nel corso del progetto.
Lean RoadMap®
Fase in cui si progetta lo stato futuro del processo analizzato in ottica multiscenario. Una volta scelto lo scenario più corretto dal punto di vista tecnico-economico si passa alla pianificazione del percorso da intraprendere per realizzarlo. Nella Lean RoadMap® emergono le attività su cui focalizzarci e le tempistiche con cui portarle a termine.
La direzione da percorrere
01
Implementazione dell'A3-X
Strumento che ha lo scopo di definire i progetti rilevanti per la strategia aziendale e correlarli a persone, obiettivi e indicatori chiave.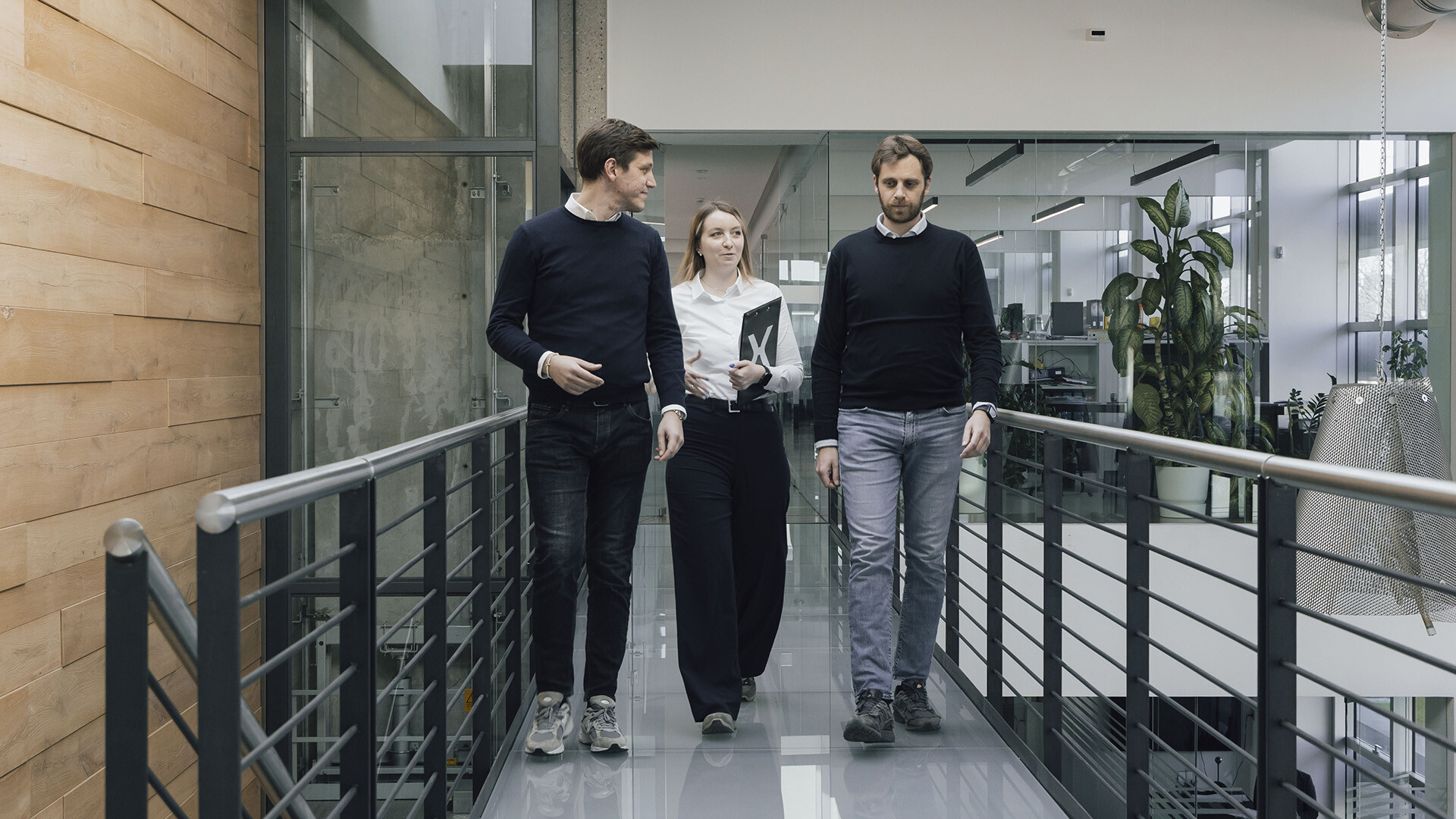
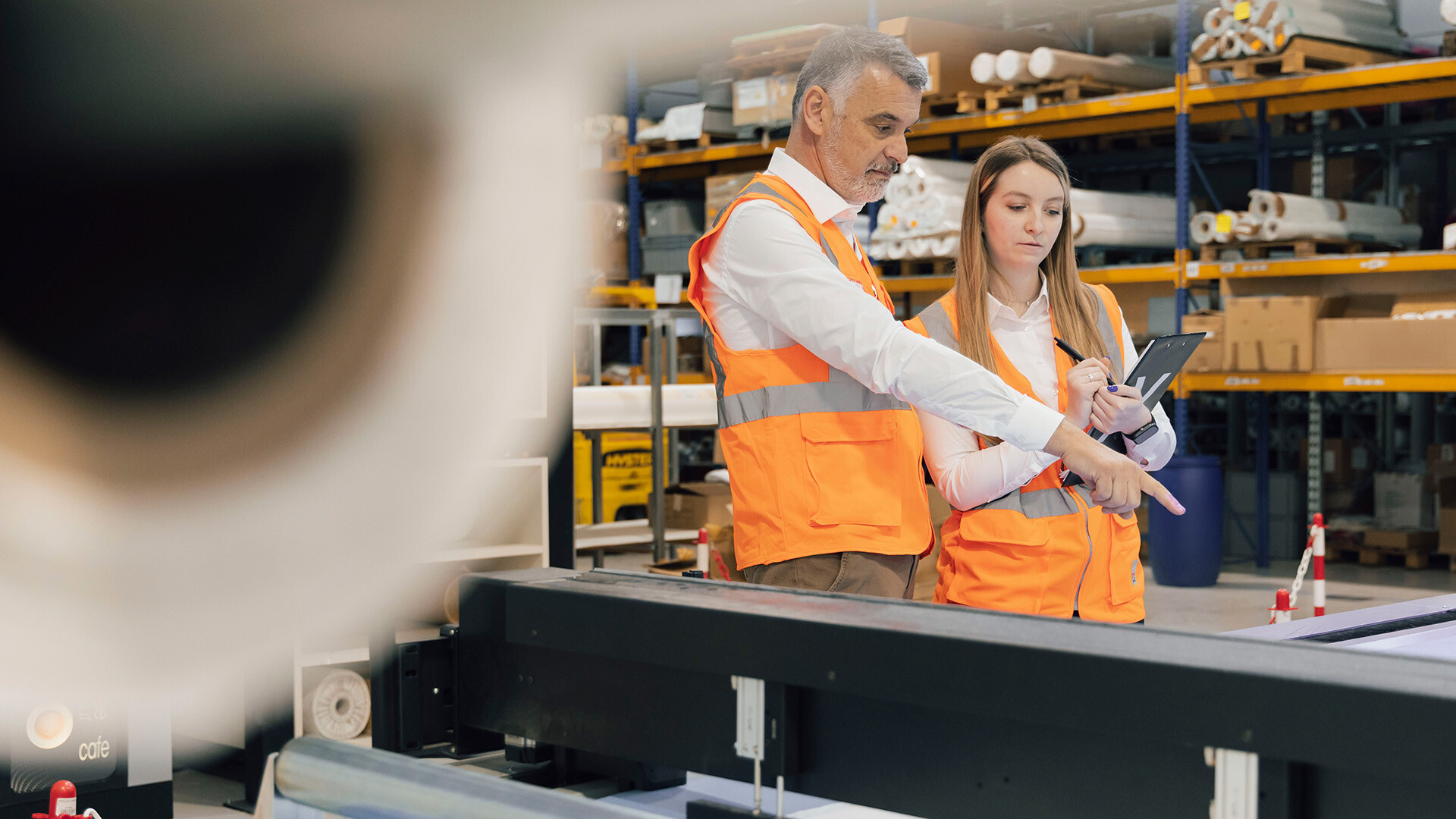
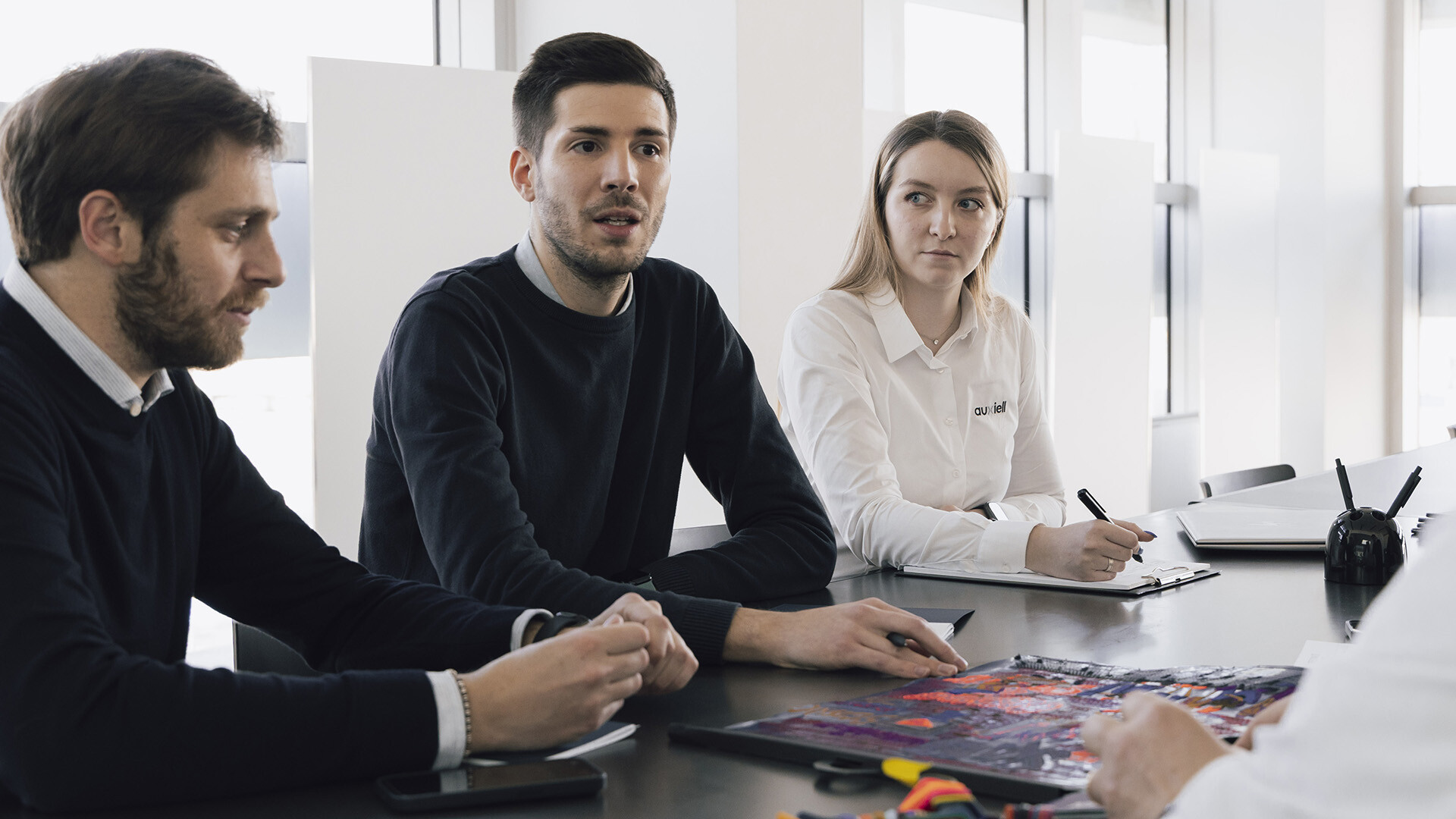
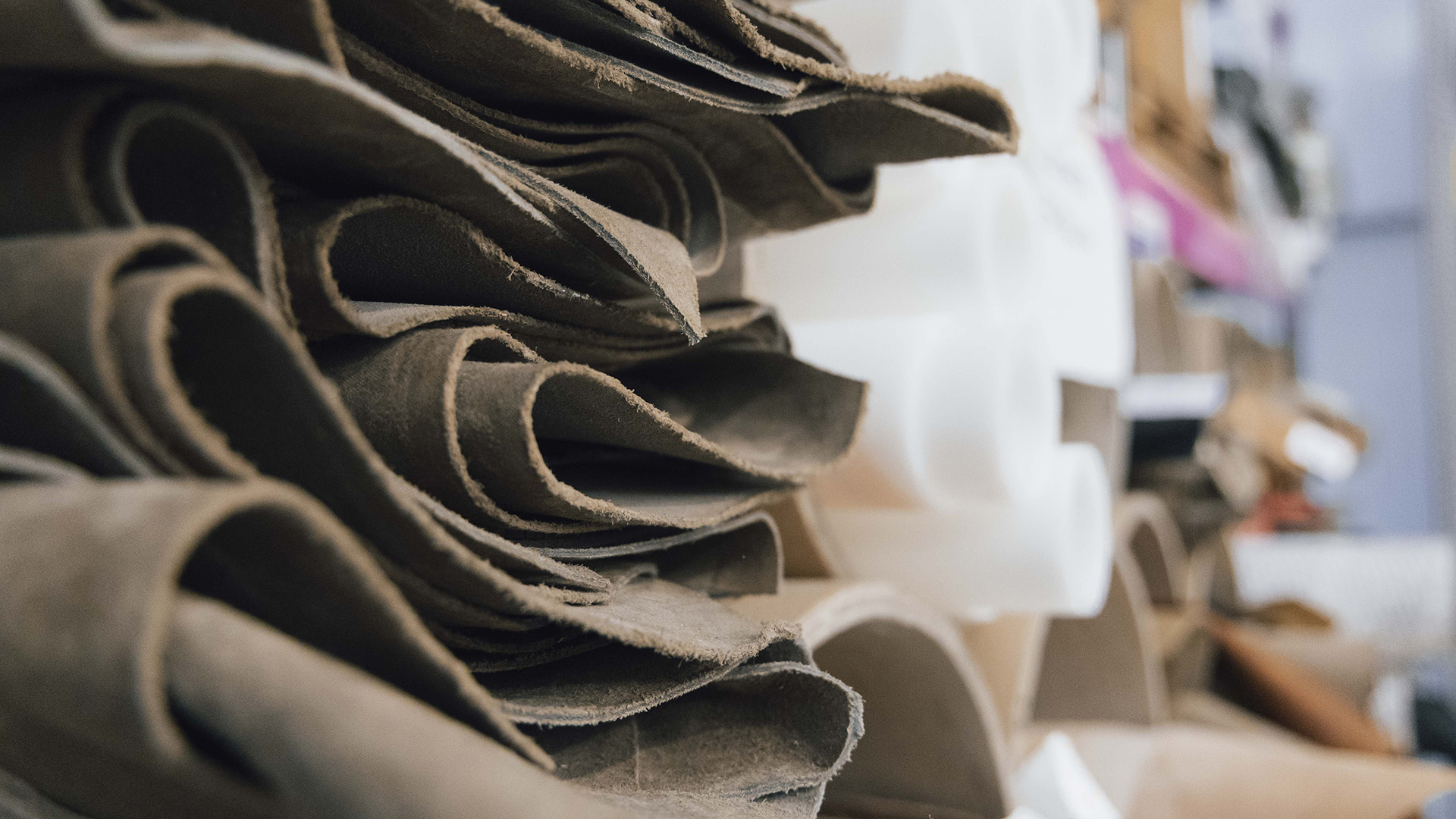
DO
Hoshin Kanri
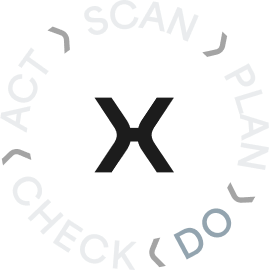
Quali attività e tecniche lean ci hanno permesso di raggiungere l’obiettivo stabilito?
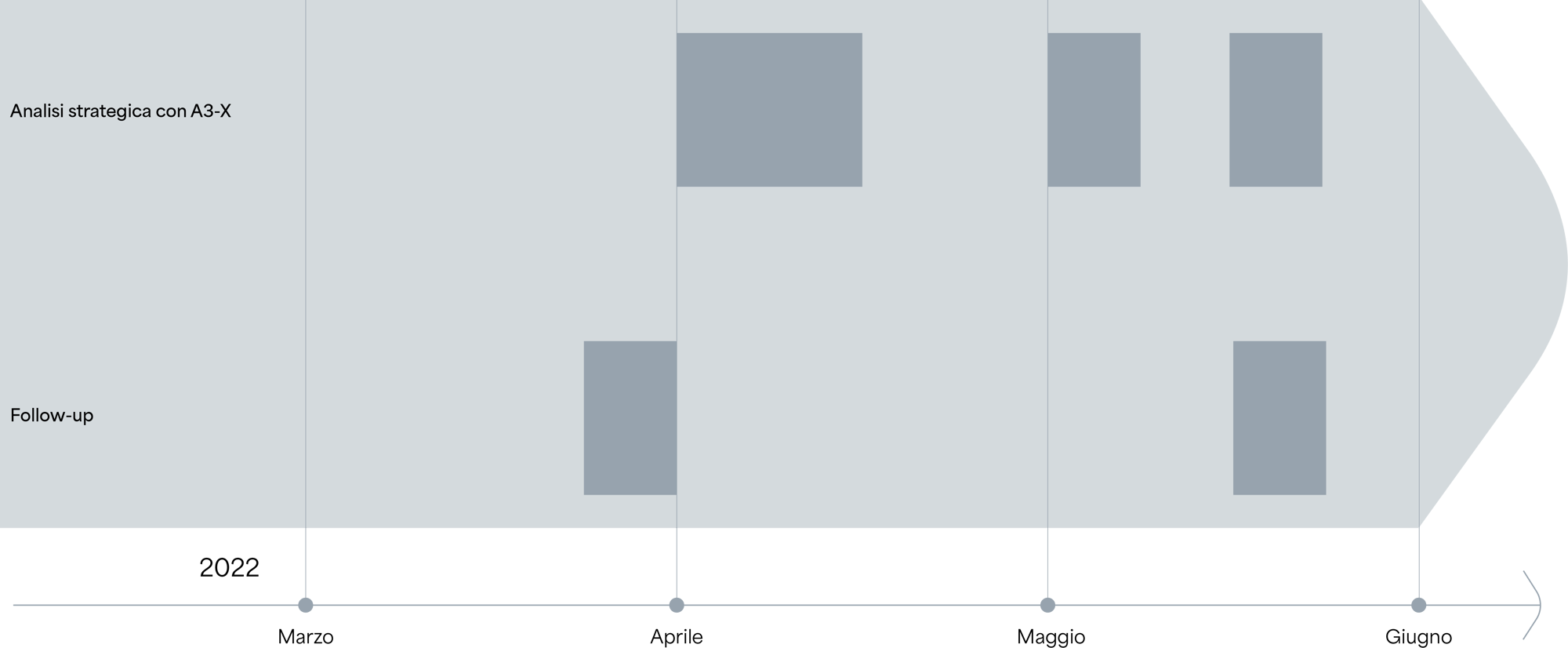
A3-X
Sono state dapprima definite le strategie aziendali da parte dell'azienda. Sulla base di queste sono stati definiti tutti i progetti principali a livello aziendale e - tramite la correlazione tra strategia e progetto - è stata effettuata individuata la priorità di attuazione di ogni progetto sulla base di un GANTT.
CHECK
Abbiamo raggiunto gli obiettivi stabiliti?
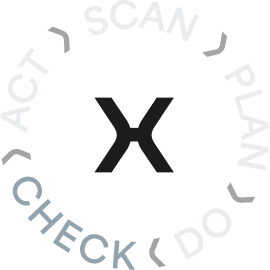
L’ottimizzazione della gestione strategica è stata ottenuta attraverso l’A3-X, strumento che ha permesso di selezionare solo i progetti prioritari in linea con gli obiettivi aziendali, assegnare team dedicati e definire indicatori chiave di performance. Questo approccio ha portato alla standardizzazione degli sprint meeting settimanali del "team hoshin" e al completamento della formazione e allineamento strategico per tutti i primi livelli garantendo una maggiore coerenza e focalizzazione sugli obiettivi aziendali.
Il livello di allineamento dei progetti alla strategia aziendale è aumentato.
Dal Deployment alle opportunità future
Il progetto nel Deployment è stato quello che ha permesso di portare avanti tutti gli altri progetti nelle altre D, ora analizzati come allineati alla strategia aziendale.
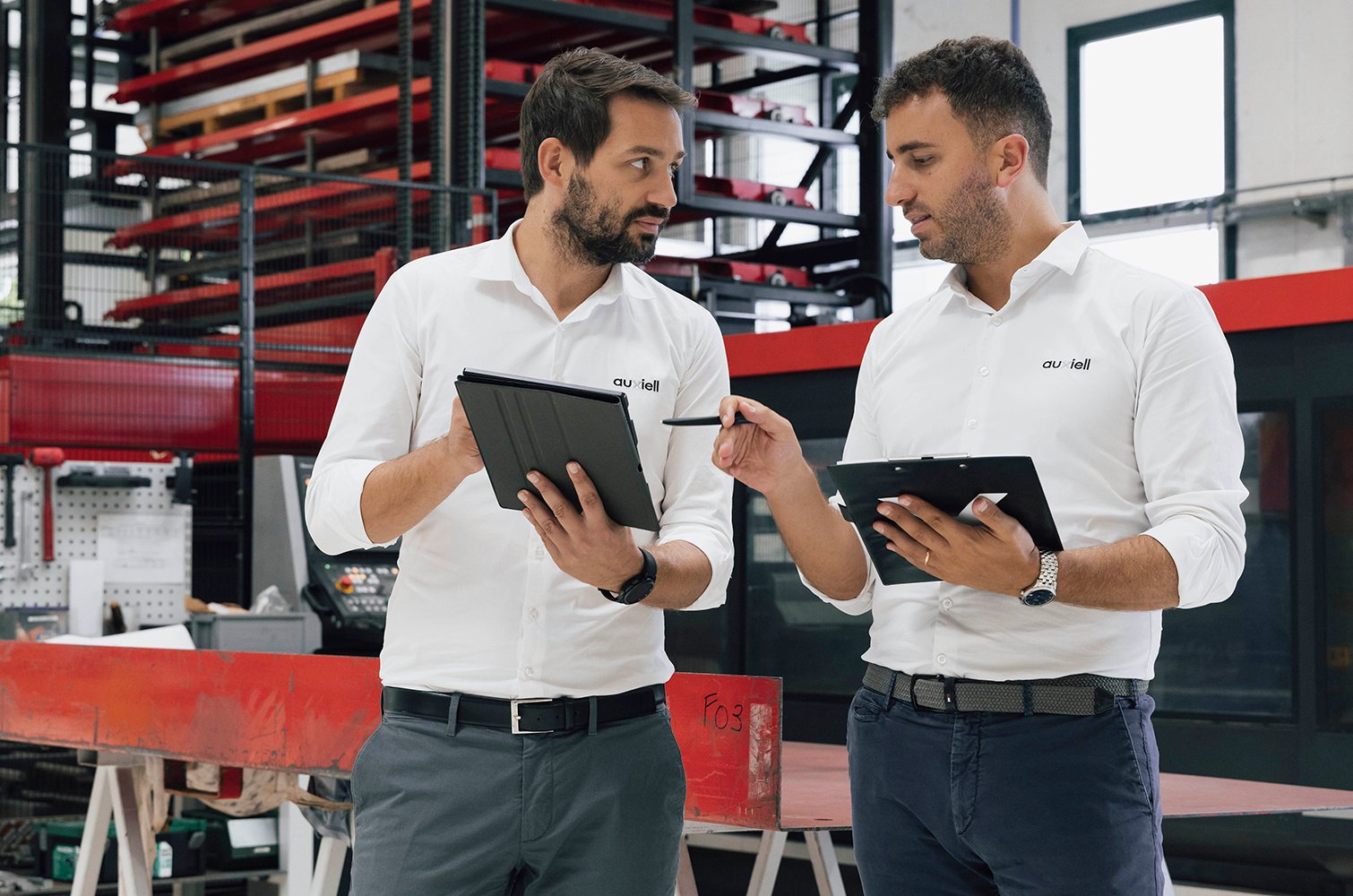
I nostri esperti a disposizione per guidare la tua azienda alla trasformazione
Iscriviti alla nostra newsletter e ricevi contenuti esclusivi, consigli pratici e novità direttamente nella tua inbox!