Portfolio
ABS
Intro
Cómo se mejoró la competitividad mediante una visión sistémica de los procesos y la alineación con la demanda
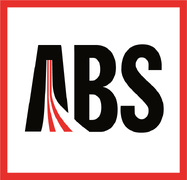
Industria
Oficina
Rendimiento
alcanzado
Productividad
media diaria
Rendimiento
alcanzado
puntualidad (LOTP)
reducción de existencias en toda la línea
¿Quiere mejorar el rendimiento de su empresa?
Historia
empresa
1988
ABS se creó en 1988 a partir de la fusión de dos acereraras altamente calificadas y experimentadas: Officine Bertoli, fundada en 1813, y Safau, cuyos orígenes se remontan a 1934. Desde entonces, representa la división siderúrgica del Grupo Danieli.
Hoy
ABS está especializada en la producción de aceros largos especiales, un tipo de producto altamente especificos para sectores que requieren prestaciones de alta calidad y aplicaciones técnicas y mecánicas avanzadas. La producción utiliza íntegramente el ciclo de la chatarra, que reduce las emisiones en un 65% en comparación con el ciclo del horno industrial. ABS es proveedor de importantes industrias en constante innovación, como las de automotora, generación de energía eólica y petróleo y gas.
Empleados (2024)
0Facturación (2024)
0EBITDA (2024)
0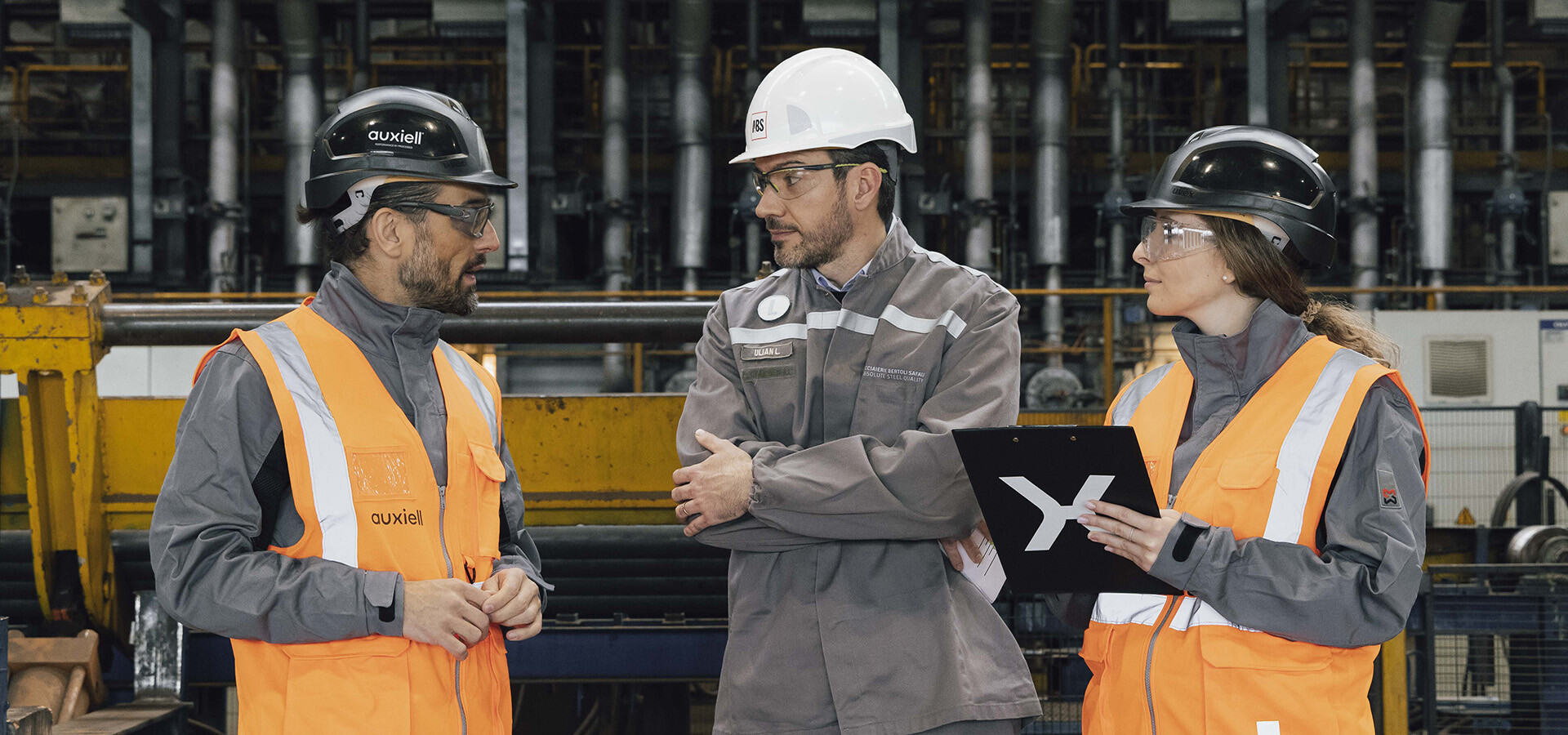
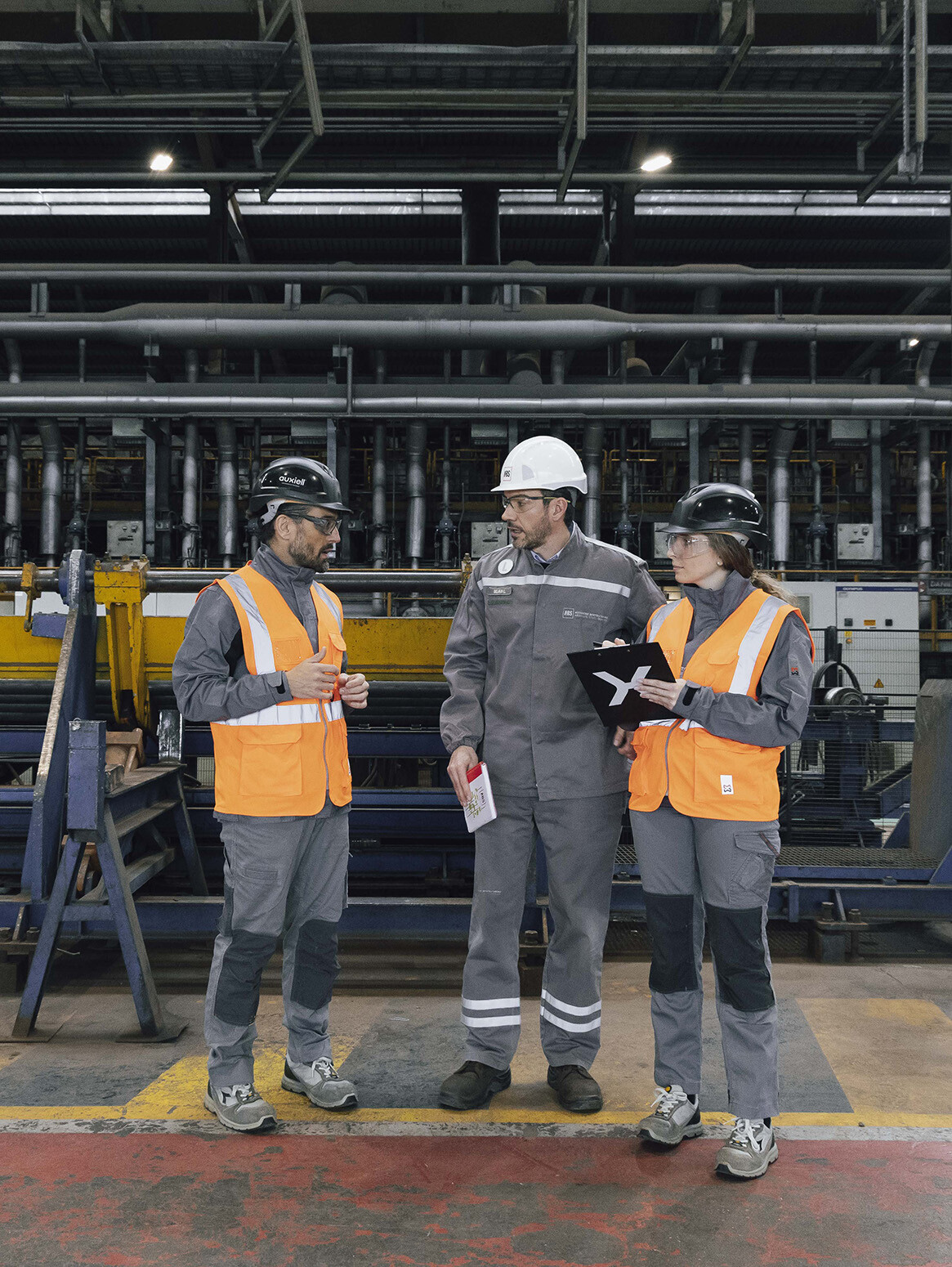
El reto ABS
ABS recurrió a nuestro equipo en busca de apoyo para adquirir una visión sistémica de sus procesos de producción. El objetivo era apoyar el crecimiento del negocio mediante la creación de los mejores procesos de suministro y producción vinculados a las necesidades reales de clientes específicos.
El punto de partida
La transformación del primer macroproceso: la entrega
2022
Año de inicio de la colaboración
con auxiell
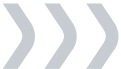
El proyecto continúa
Con ABS emprendimos inicialmente un proyecto sobre el macroproceso de entrega, que comprende la producción, la cadena de suministro y la gestión de pedidos.
SCAN
Lean Gap Analysis® en la entrega
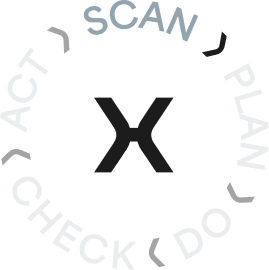
Para analizar el estado actual de los procesos, el equipo de auxiell-ABS emprendió el Lean Gap Analysis® de todo el flujo de valor de Luna: un proceso que parte de la chatarra y produce barras con distintos acabados. El mapeo abarcó todo el proceso, desde la producción en la acerera hasta la entrega del producto laminado al cliente. Los residuos y las oportunidades de mejora que surgieron se referían a la acerera (desde la fusión de la chatarra hasta la creación de la bloom), el tren de laminación y el acabado.
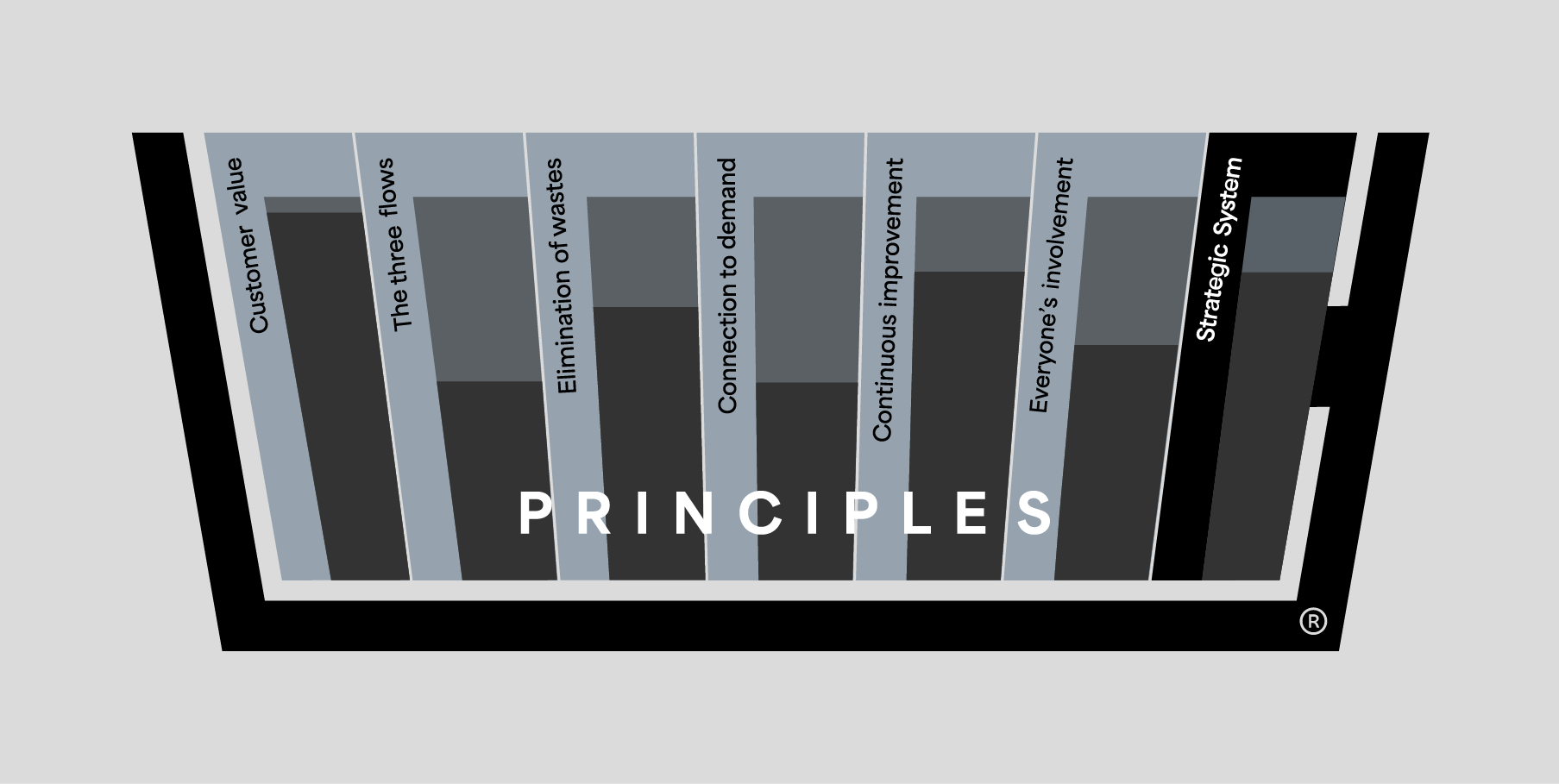
Plazos de entrega al cliente incumplidos
El elevado volumen de materiales en curso de fabricación y la estructura de producción caracterizada por una flexibilidad limitada afectaron a los plazos generales del proceso.
Variabilidad en el rendimiento de las entregas
Desviaciones de los plazos previstos que repercuten en la percepción del nivel de servicio por parte de los clientes.
Gestión de los materiales en WIP entre las distintas fases del proceso
La organización de los flujos de acabado según un modelo de "lotes y colas" conducía a un almacenamiento no siempre óptimo en los puntos de desconexión del proceso, en particular entre la acerera y el tren de laminación y en las etapas posteriores. En este fenómeno influía el desajuste de las capacidades de producción de las distintas etapas.
Eficacia de las fases
La atención se centraba en la rentabilidad de cada fase individual y faltaba una visión integral del proceso.
Decisiones tomadas a partir de indicadores de fase
La ausencia de indicadores de proceso limitó la posibilidad de apoyar las decisiones relacionadas con los flujos.
PLAN
Lean RoadMap® en la entrega
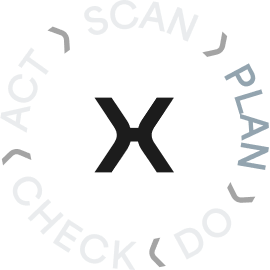
Estos fueron los puntos de partida para la siguiente fase del proyecto, la fase PLAN. A través del Lean RoadMap® definimos la secuencia de asentamiento de las técnicas lean más adecuadas que nos permitirían alcanzar los objetivos acordados con el equipo de ABS. En concreto, el equipo se centró en:
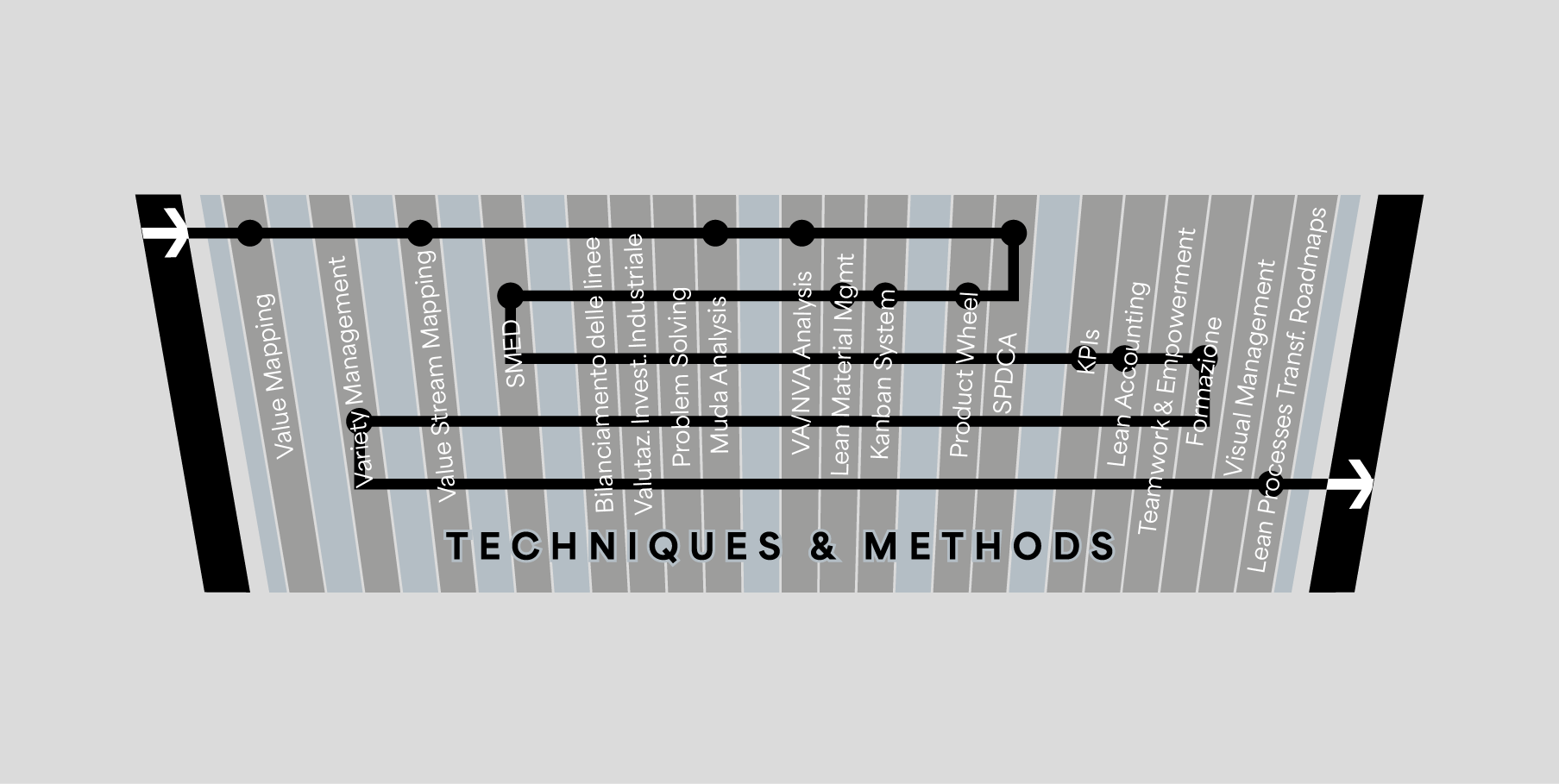
Modernización de la rueda de productos de laminación
Aumentar la vinculación a la demanda y la flexibilidad de la producción.
Revisión de la organización de los ensayos y laboratorios según la lógica pull
Garantizar que las pruebas-realizadas por quienes verifican los parámetros de proceso y calidad- y los laboratorios -donde se llevan a cabo los análisis de calidad de los productos- se gestionen de forma más eficaz y con plazos reducidos.
Introducción de un sistema pull de gestión de la producción
Reducir el plazo de entrega del proceso y disminuir la capacidad de producción de cada etapa para evitar "colas", es decir, que el material en stock espere delante de cada etapa.
Revisión de los KPI de proceso
Para que sean más completos y estén más relacionados entre sí y con las necesidades de los clientes.
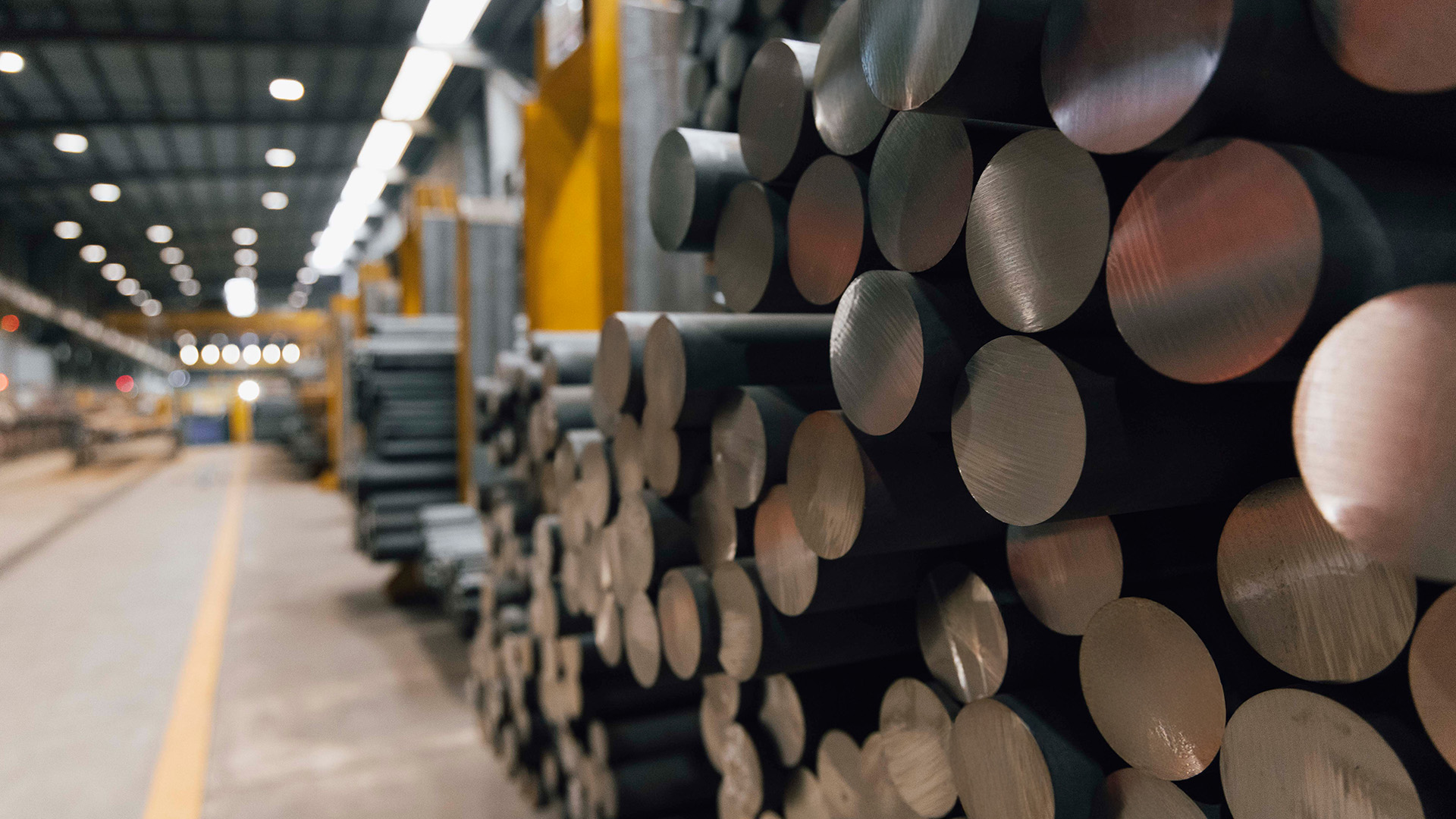
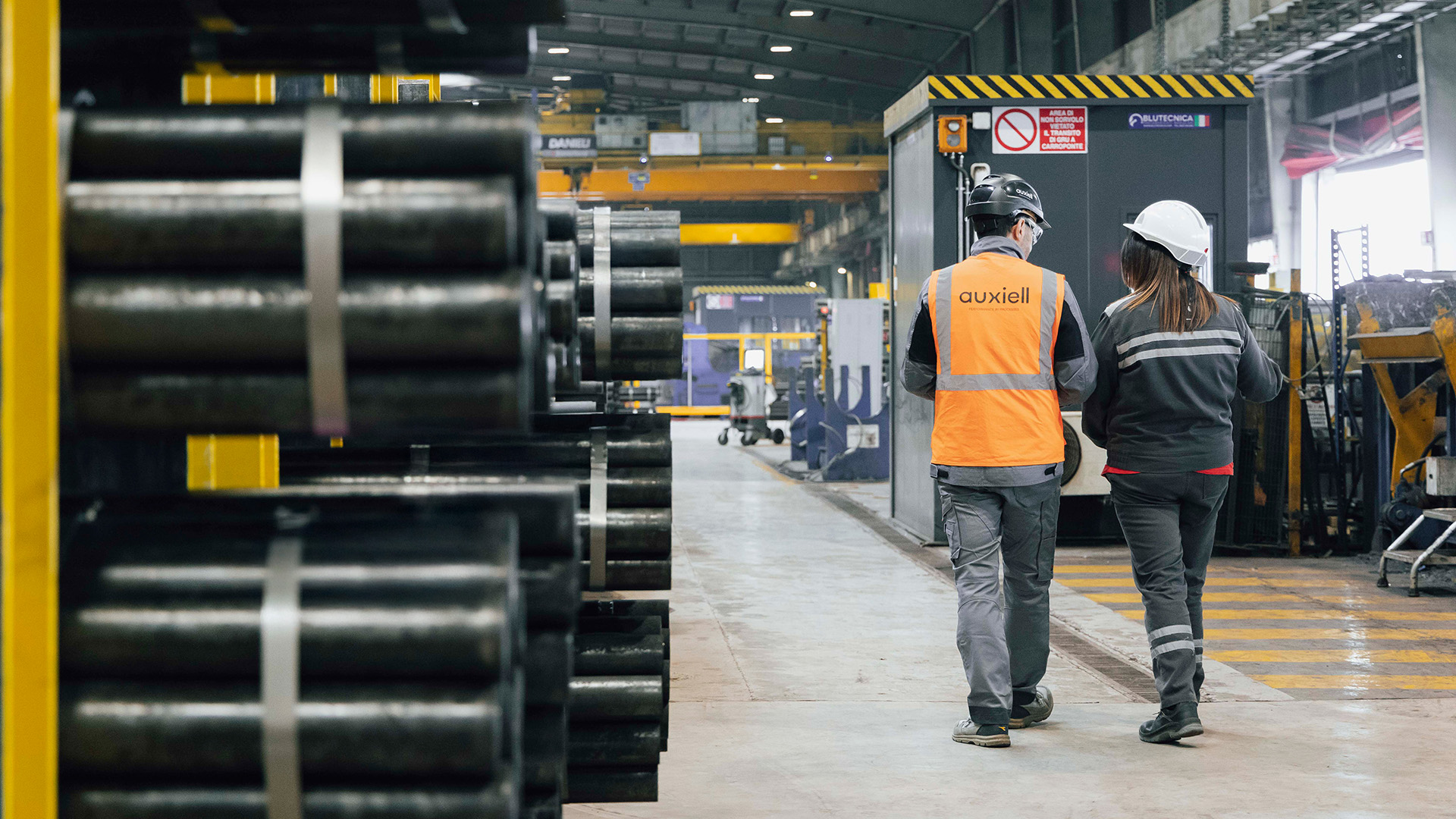
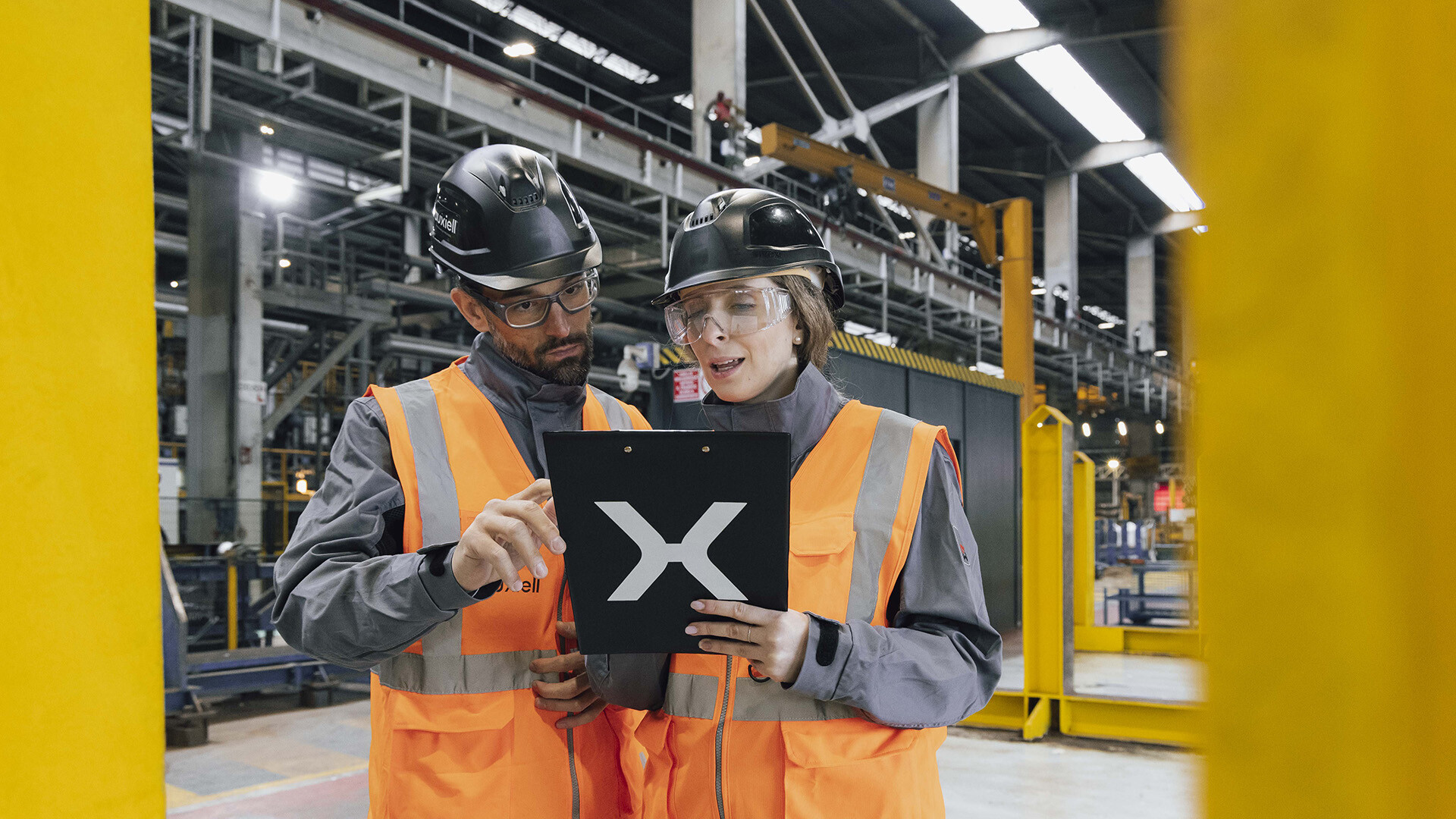
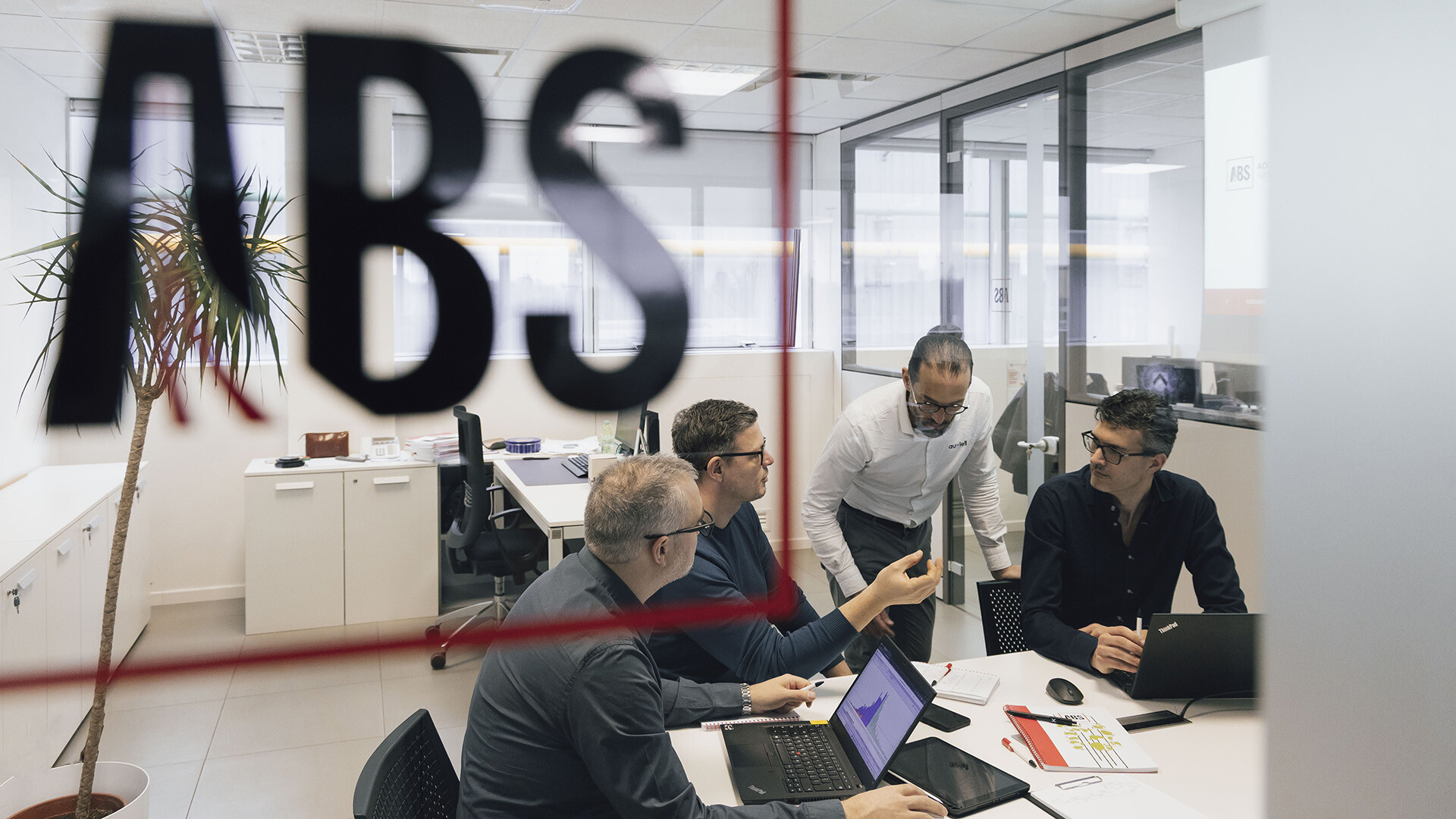
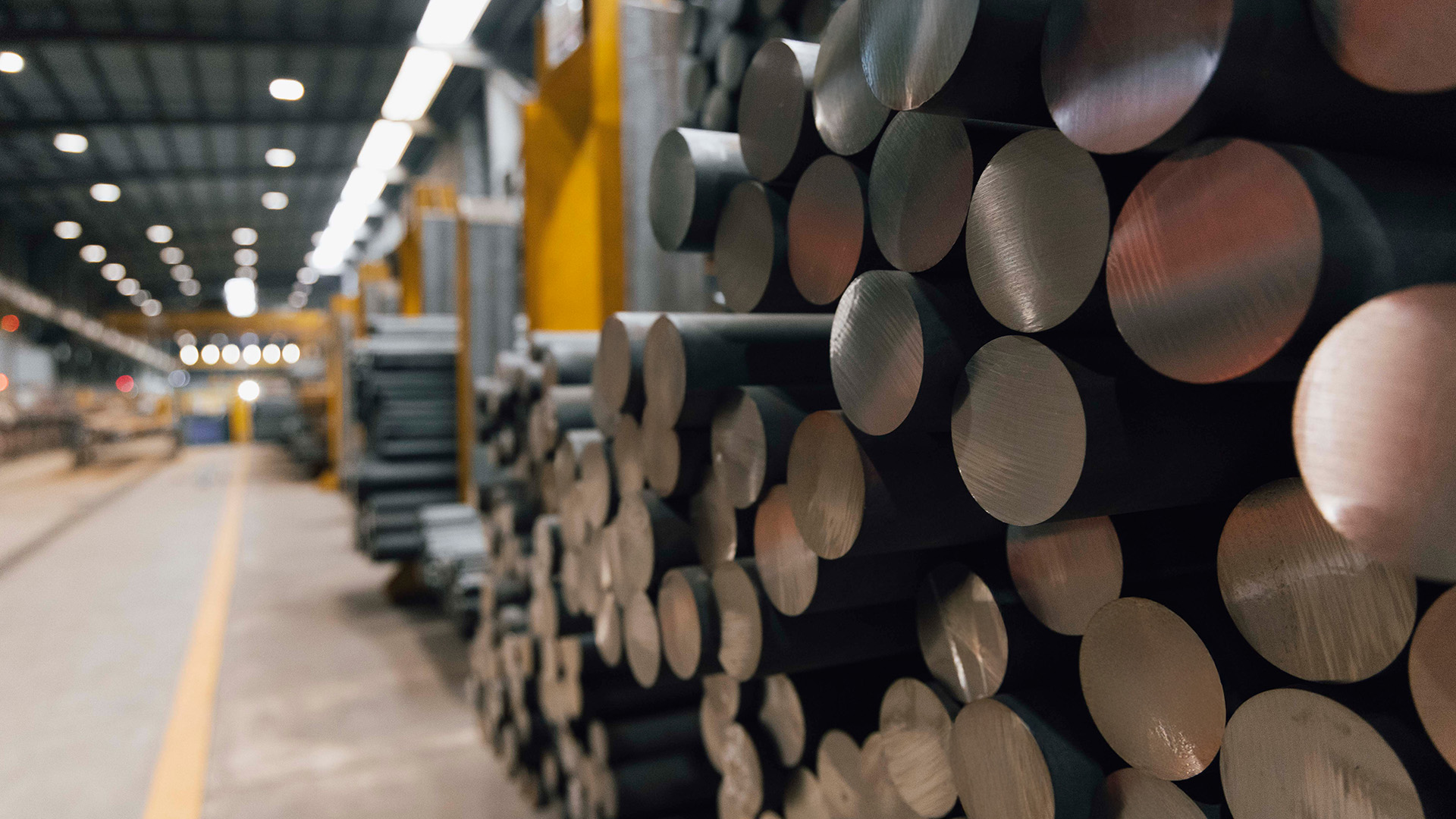
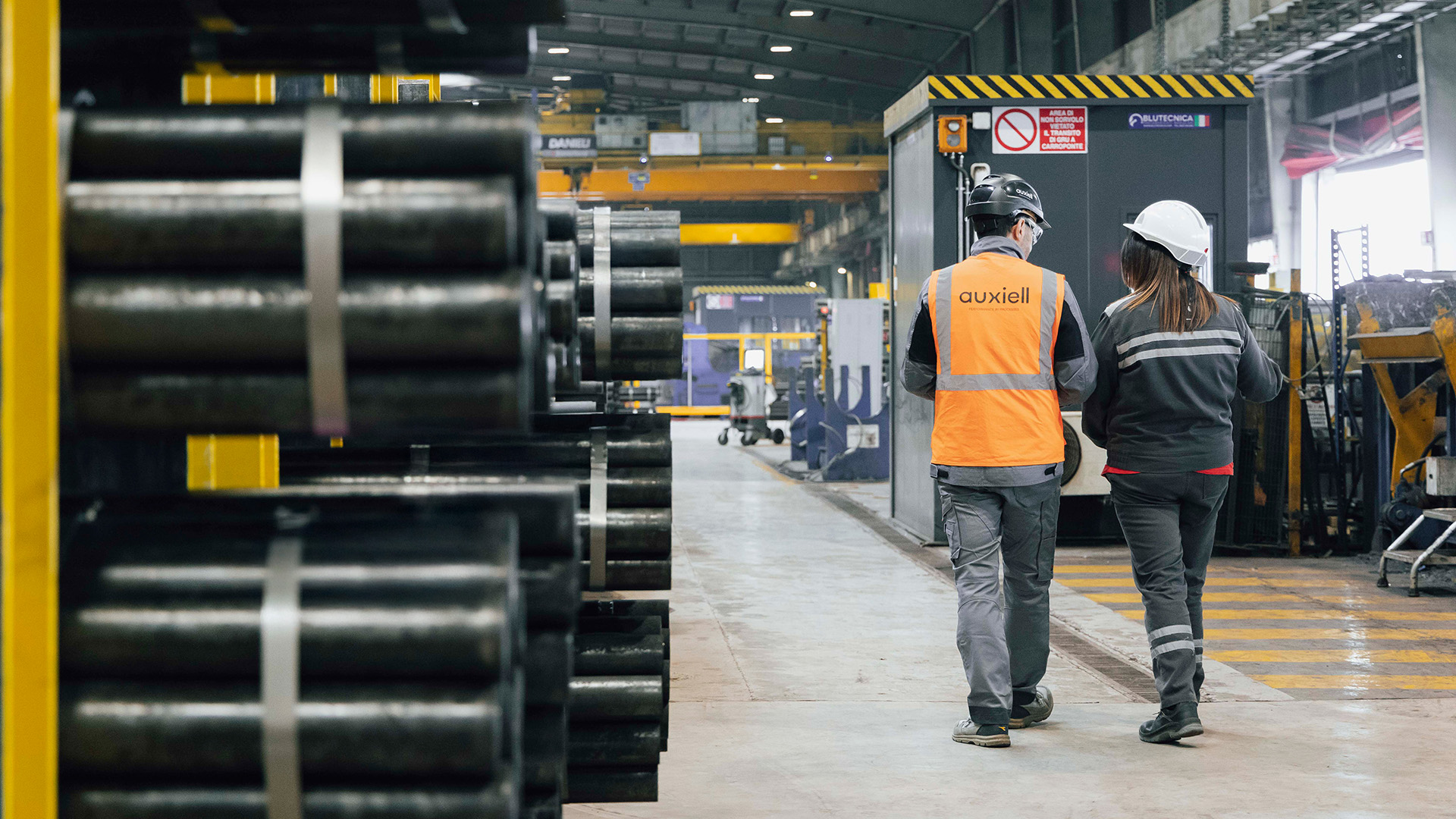
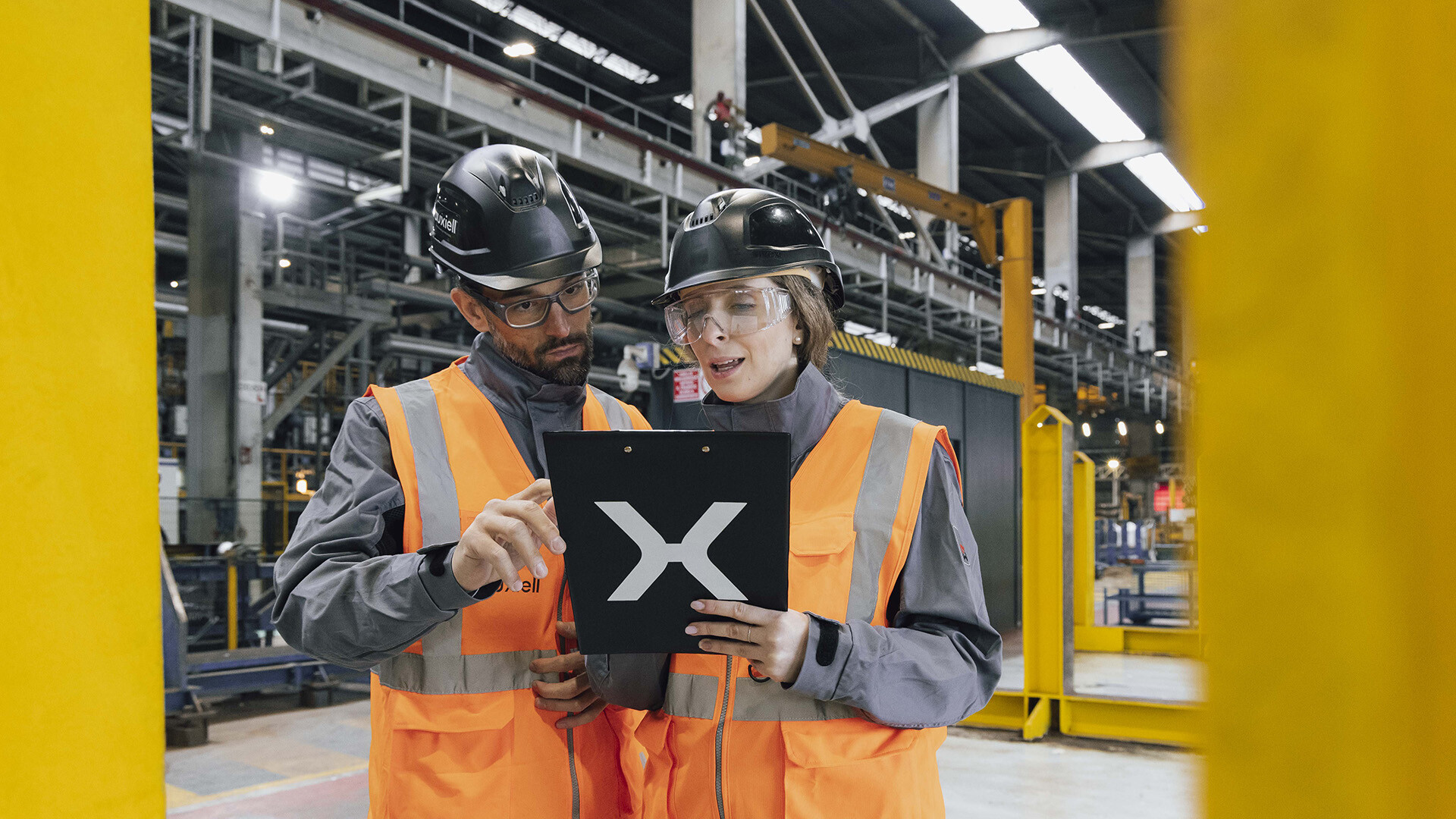
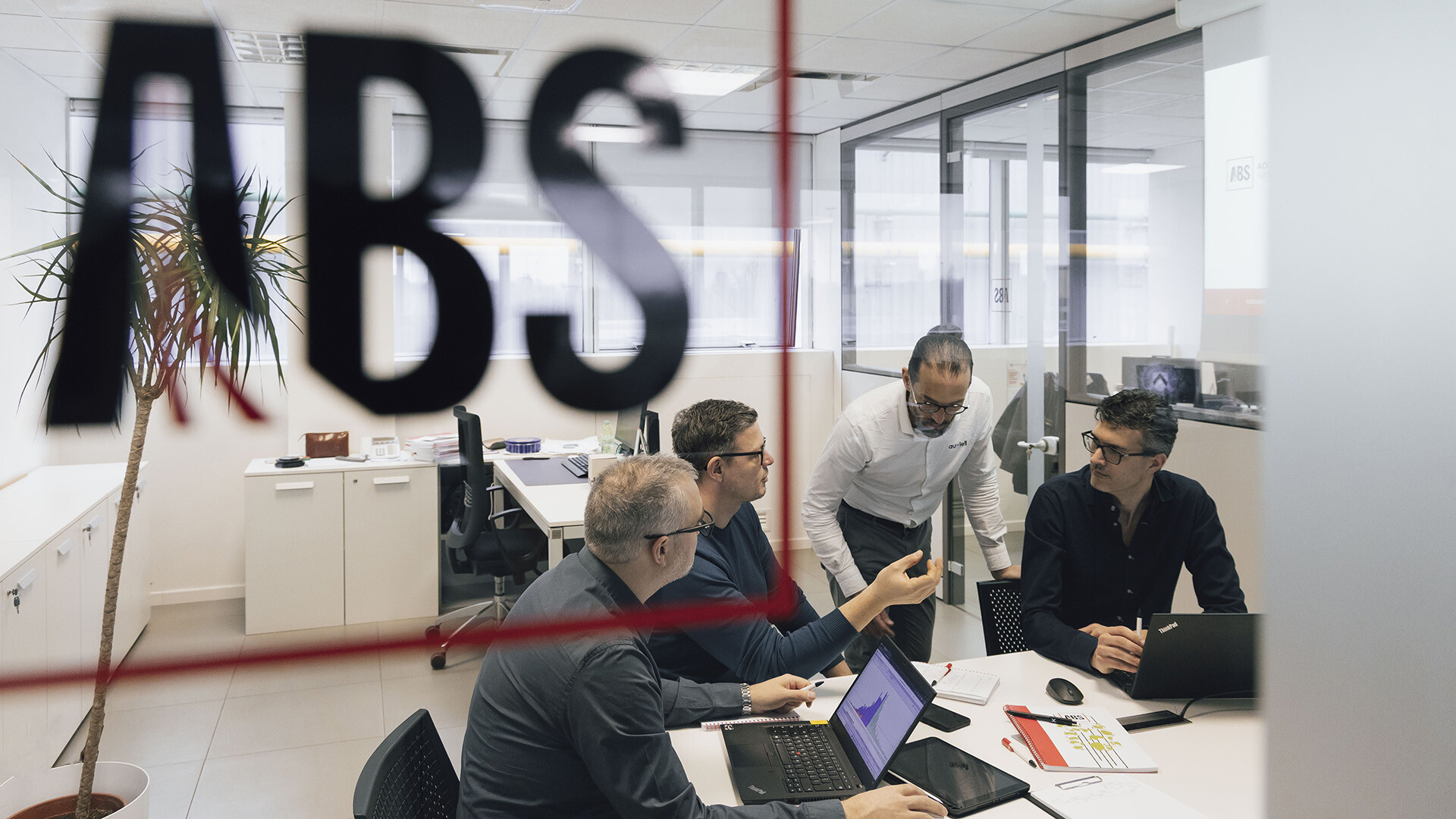
DO
Entrega Transformación global
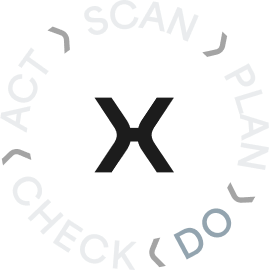
¿Qué actividades y técnicas lean nos han permitido alcanzar el objetivo definido?
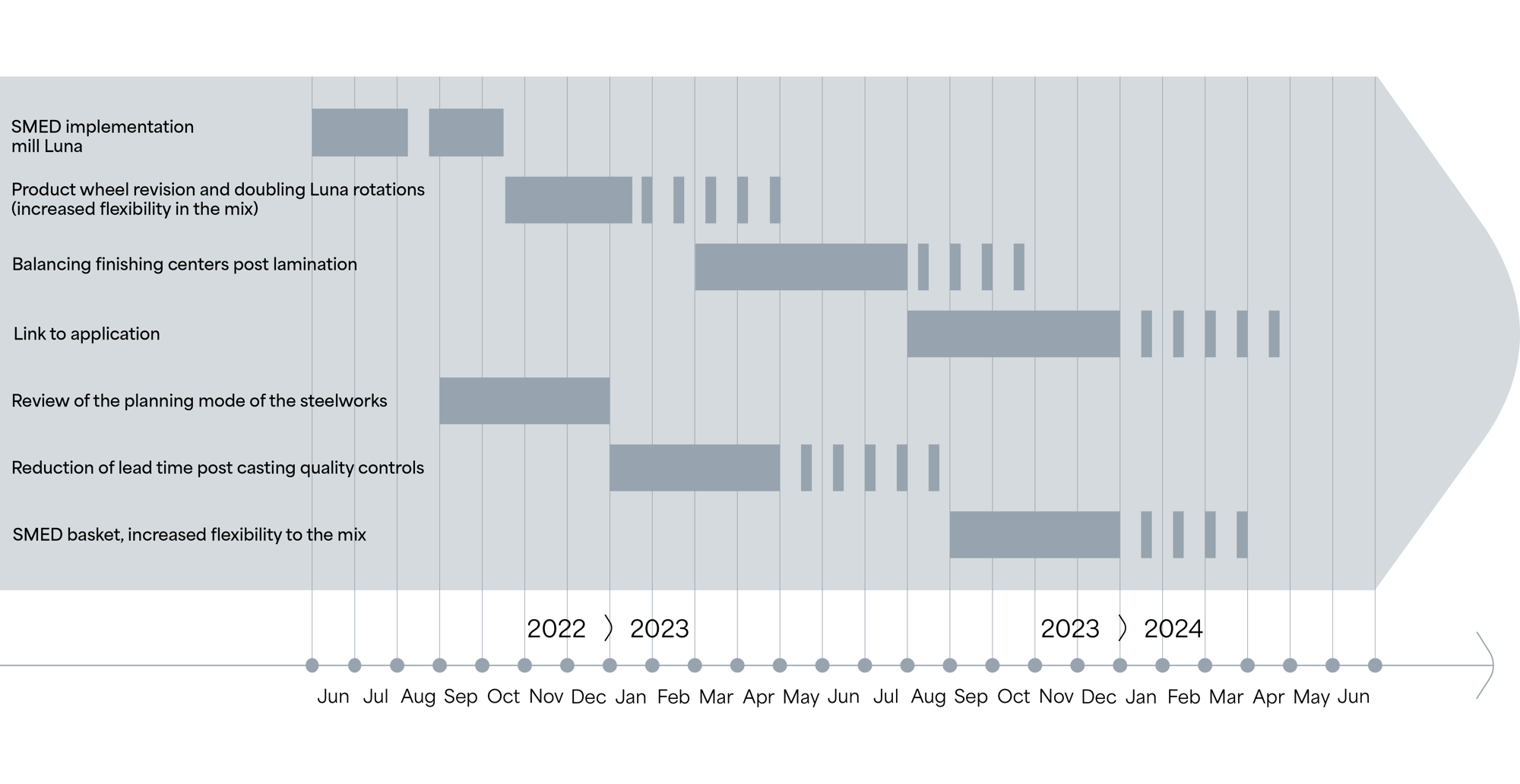
Vinculación con la demanda y la rueda de productos de la fábrica
En colaboración con los departamentos de producción y control de calidad, por un lado, y con el personal de ventas y el equipo de planificación, por otro, se determinaron las acciones más adecuadas para conocer a fondo las necesidades reales de los clientes. Con el apoyo de edxiting, se organizó un taller -el Juego del Acero- dedicado a identificar las necesidades de los clientes y vincularlas a la demanda. Una vez creados los modelos de respuesta del mercado con ABS, involucramos directamente a los clientes en el proyecto definiendo con ellos -al más alto nivel de detalle- las acciones y herramientas para satisfacer las demandas. En cuanto a la producción, el efecto fue nivelarla vinculándola mejor a la demanda mediante el uso del Kanban con clientes seleccionados. Gracias a la visibilidad de la Rueda de Productos, algunos clientes tuvieron la oportunidad de operar en lógica de "reserva de capacidad", pudiendo reservar una franja horaria específica para sus pedidos. Este enfoque permitió probar y optimizar el sistema, con beneficios potenciales que pueden ampliarse en el futuro.
Revisión del flujo de acabado
Se revisó todo el proceso de producción identificando los distintos cuellos de botella para eliminarlos y garantizar el flujo en las fases de acabado sin interrupciones ni aumento de las colas.
Resolución de problemas extendita: mejora de la puntualidad y reducción de existencias
Con un equipo multifuncional -planificación, producción, calidad, ventas-, mediante la aplicación de la técnica de resolución de problemas, se investigaron las causas raiz de los obstáculos al flujo y se definió un conjunto de acciones que tendrían un impacto directo en la puntualidad y el inventario. Se revisaron dos aspectos en particular
1. La lógica y los parámetros de planificación en la acerera, la laminación y el acabado.
2. La conexión de las fases del proceso para disminuir las existencias, reducir los plazos de entrega y mejorar la productividad.
Revisión de los KPI de proceso
Partiendo de los indicadores ya utilizados en ABS, se analizó lo que tenía valor para el cliente, pasando de los KPI de fase a los KPI de proceso. En concreto, se revisó el Lean on Time Production (LOTP) - puntualidad en la fecha establecida fin de la producción - y se introdujeron dos indicadores más:
1. Shipped on Time (SOT) para medir -una vez finalizado el proceso de fabricación- el cumplimiento de la fecha de envío del producto acabado al cliente.
2. Lean on Time Delivery (LOTD) para controlar la llegada del material al cliente.
Esta actividad se llevó a cabo íntegramente a cuatro manos, con el equipo de ABS compuesto por personalidades de distintas áreas de la empresa: desde el director de ventas hasta el de desarrollo de negocio, pasando por el de logística y el de planeación.
Gestión de las pruebas en el laboratorio
Se hizo que la fase de pruebas fluyera haciendo que las muestras cortadas fueran visibles para el laboratorio, identificando horas fijas para que los operarios del laboratorio recogieran las muestras y publicaran los resultados en un día (desde los 4 días iniciales). Se redefinieron los flujos de trabajo del laboratorio y se implementó el milkrun de recolección de muestras en lógica pull -convirtiéndolo en poka yoke- y reduciendo así también el plazo de entrega de los ensayos metalográficos en el laboratorio. Otra actividad de mejora se refería al proceso de emisión de certificados de calidad de los productos: se revisó el flujo de información vinculando la fase de preparación del material (en espera de ser enviado) a las prioridades de emisión de certificados.
Programación de las órdenes de fabricación de la acerera con horizontes variables
Con el fin de reducir las existencias entre la acerera y el tren de laminación y las existencias aguas abajo del tren de laminación, se redujo el horizonte de planeación: inicialmente, se consideró un horizonte temporal de cinco semanas. En un primer momento, se clasificaron los artículos en función del volumen y la frecuencia de consumo mediante la técnica ABC-RRS (técnica de análisis aplicada en la fase de exploración y planeación). Se propuso trabajar con un horizonte diferenciado en función de la rotación del artículo: 3 semanas en artículos de alta rotación [Runners] (consumidos durante al menos el 80% de las semanas del periodo analizado), mientras que 4 semanas en artículos de rotación media [Repeaters] y 5 semanas en artículos de baja rotación [Strangers] (consumidos durante menos del 15% de las semanas del periodo analizado). A continuación, la clasificación se introdujo en el sistema de gestión para planear la producción de pedidos en función de los plazos previstos para cada categoría.
CHECK
¿Hemos alcanzado nuestros objetivos?
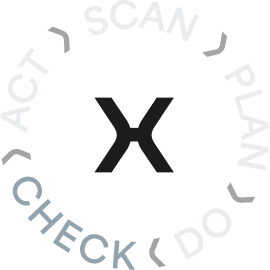
Aumento de la puntualidad en un 7% LOTP - dentro de lo previsto en comparación con el valor fijado inicialmente.
Las existencias de productos semiterminados y terminados disminuyeron un 17%.
A nivel de equipo, se han iniciado una serie de actividades de resolución de problemas auto-proporcionadas y el grupo sigue participando constantemente en la mejora autónoma de los procesos.
El involucramiento de las primeras líneas de los equipos de control comercial/logístico/producción/gestión permitió organizar reuniones semanales del proyecto para poder actuar rápidamente en caso de desviaciones del objetivo.
El equipo piensa en términos de proceso y no de costos de una sola etapa, hasta el punto de que en algunos casos optan por soluciones que aumentan los costos de una sola etapa al tiempo que reducen los costos de proceso.
Los beneficios obtenidos influyeron positivamente en el equipo. Las personas, que se pusieron a disposición desde el principio y mostraron una notable disposición al cambio, abrazaron el proyecto con entusiasmo. Son las personas las que aportan los resultados y solo cambiando su comportamiento es posible tener éxito en la transformación: esta es la verdadera diferencia entre ser lean y hacer lean.
Del punto de venta piloto a todo el canal de ventas
El método adquirido del rediseño de la tienda piloto permitió a la dirección y al equipo interno de mejora tomar conciencia de los beneficios cualitativos y cuantitativos de la transformación Lean. Esto nos llevó a construir un estándar Aspiag para el análisis y rediseño de todos los procesos de la tienda y nos permitió empezar a extender las mejoras realizadas en la tienda piloto a todas las tiendas del canal durante un periodo de 3 años.
¿Quiere mejorar el rendimiento de su empresa?
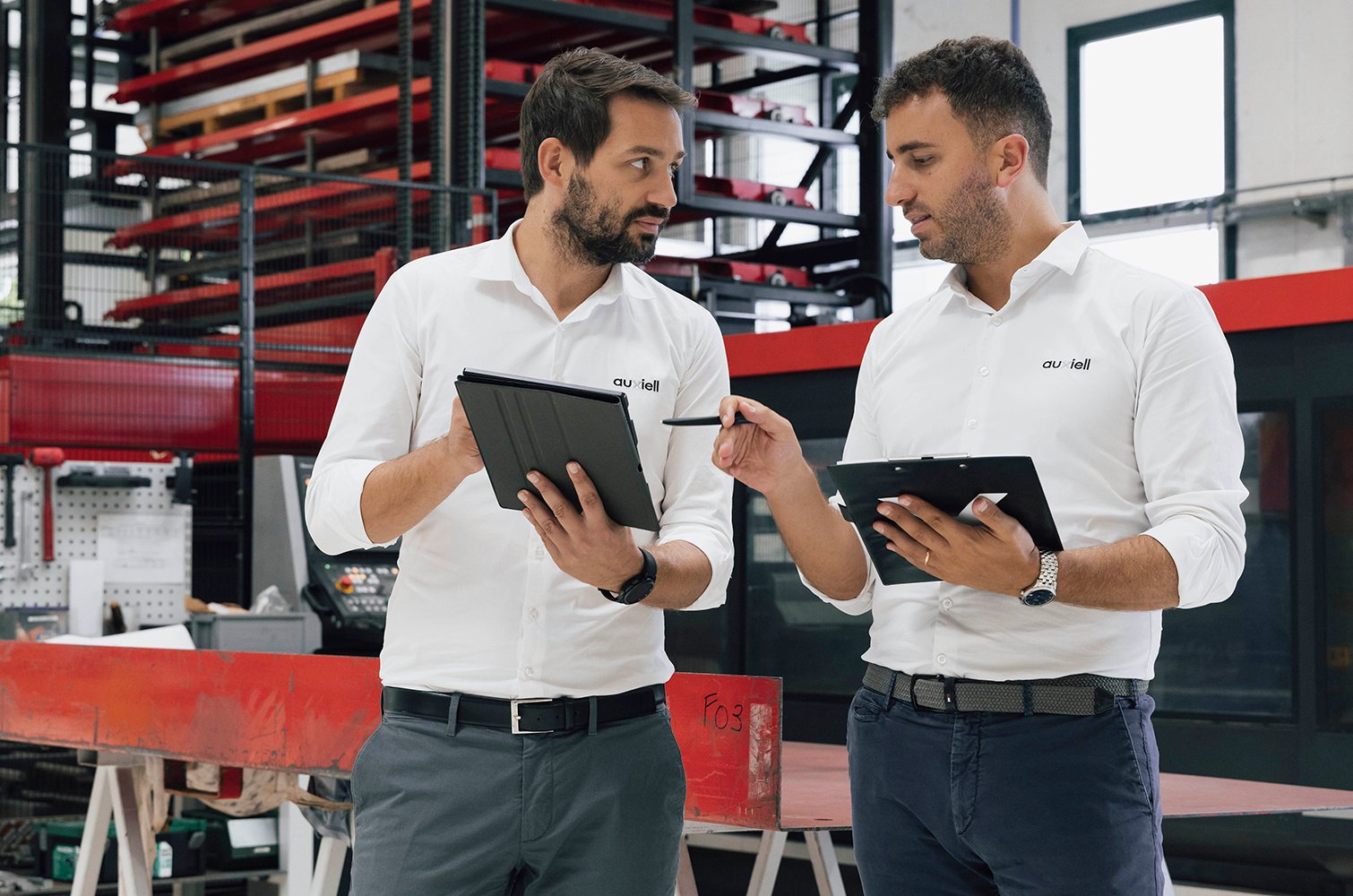
Nuestros expertos están disponibles para ayudarte en la transformación de los procesos
¡Suscríbete a nuestro boletín de noticias y recibe contenidos exclusivos, consejos prácticos y novedades directamente en tu bandeja de entrada!