Portfolio
Energreen
Intro
How Energreen managed to make processes more efficient by increasing production capacity in less than a year
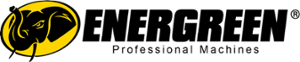
Industry
Headquarters
Subsidiaries
Energreen approached our team to find valuable support in process efficiency in order to sustain the company's growth estimated at around 30 percent annual turnover - a growth expectation far exceeded considering 2023 figures -, much of which came from the production of a specific product family: self-propelled ILF machines.
We then embarked with Energreen on a project on the Delivery macro-process comprising production, supply chain and order management: the area that would bring the most benefits in the short term.
With reference to the activities implemented, the definition of market response models, the redesign of the logistics-production flow as well as that of the warehouse and servicing allowed, also thanks to the design of a new line layout and the application of the 5S technique for space reorganization, to reduce lead time and average throughput time but above all to increase average daily productivity.
Performance Achieved
Average productivity
daily
Inventory-to-turnover ratio
(with starting target 24.1%)
Average crossing time
Market response time
History
company
1999
After 20 years of experience in outsourcing for other companies, brothers Ivo and Lino Fraron, entrepreneurs from Vicenza, Italy, founded Energreen, introducing a new branch of the company dedicated to the production of machines intended for green maintenance.
Today
Energreen is constantly evolving and over the years has become a major player in the field of public and private green maintenance machines. Its innovative machines are distinguished by performance, technological innovations, versatilityandsafety. The range of self-propelled machines, in particular, has been developed with great care to meet the direct operational needs of end users, which has led to the registration of numerous patents internationally.
Employees
0Turnover (2023)
0EBITDA (2023)
0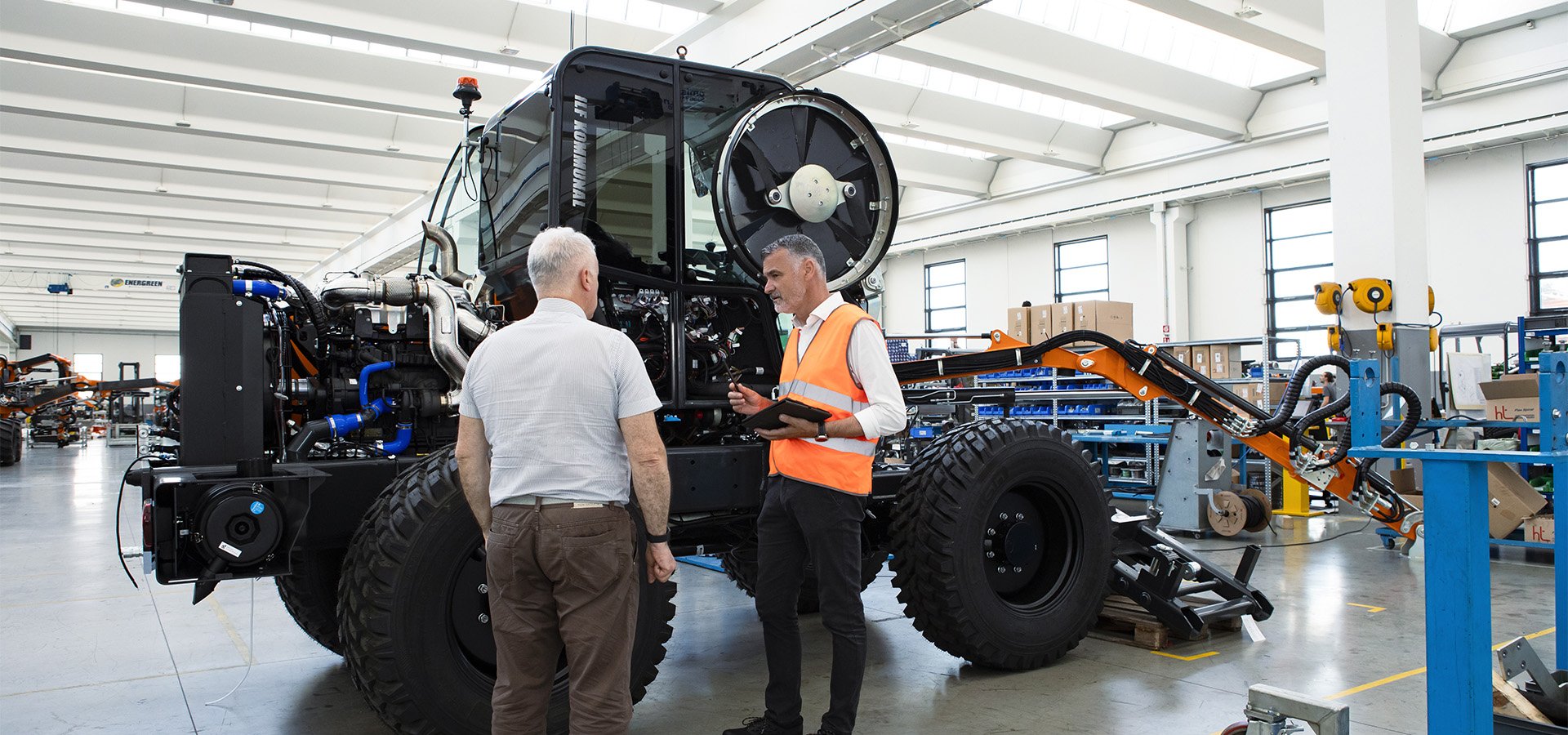
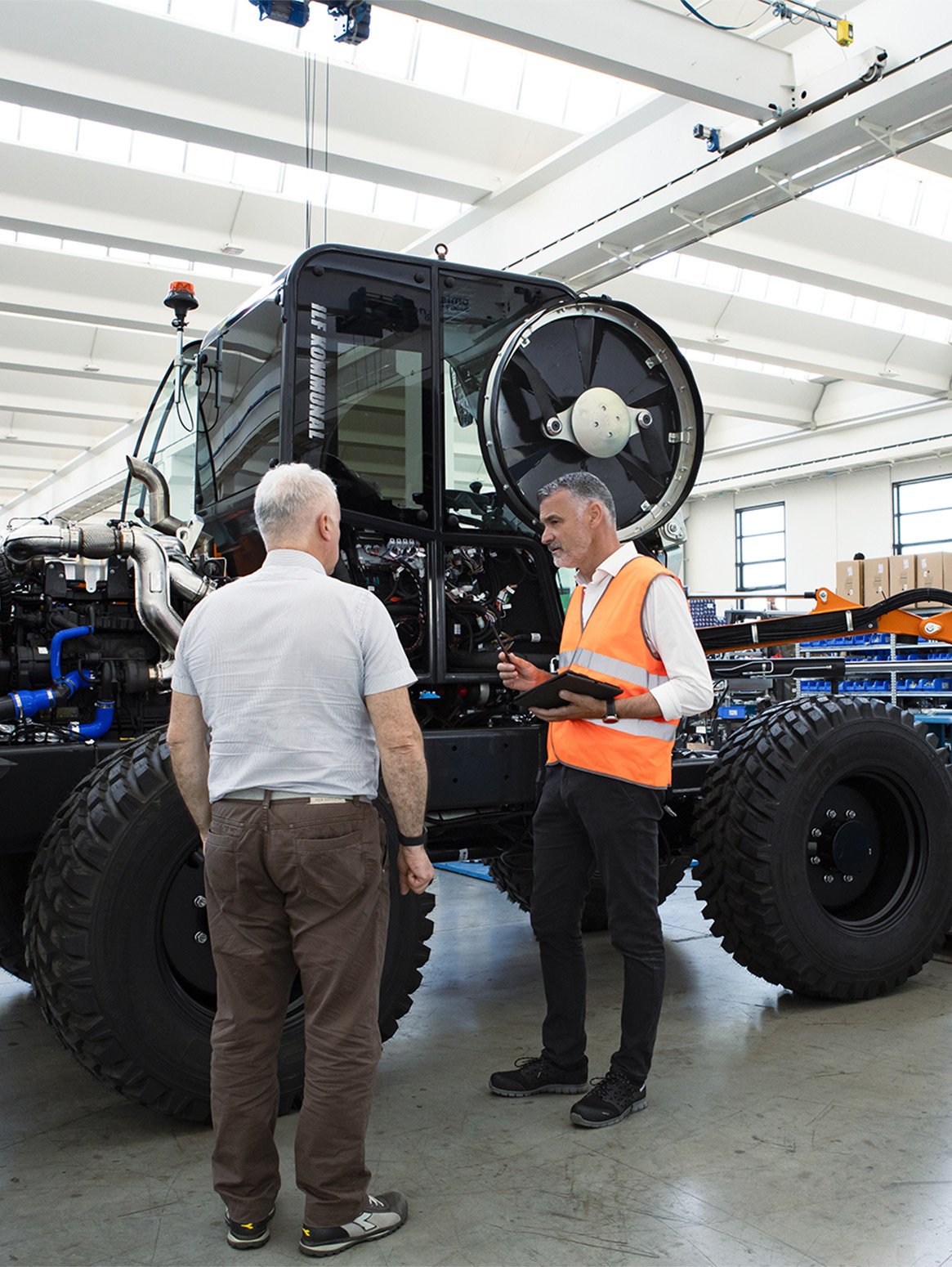
Energreen's challenge
Energreen turned to our team to find valuable support in process efficiency in order to sustain the company's estimated growth of around 30 percent in annual sales-an expectation of growth far exceeded considering 2023 figures, much of which came from the production of a specific product family: self-propelled ILF machines.
The starting point
The transformation of the first macro-process: Delivery
2023
Year start collaboration
with auxiell
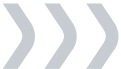
the collaboration continues
With Energreen, we undertook a project on the Delivery macro-process including production, supply chain and order management-the area that would bring the most benefits in the short term. The choice fell on the ILF self-propelled machinery product family, which alone covers 45-50% turnover and is also the product with the most important production process.
SCAN
Lean Gap Analysis® in Delivery
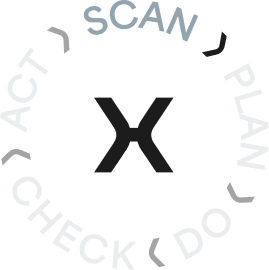
To analyze the current state of the processes, the auxiell-Energreen team engaged in Lean Gap Analysis® of the production process-from the moment the order arrives until the product is shipped to the customer. What were the value and non-value activities? What emerged was a comprehensive analysis of the as-is status of the line balance and waste within it.
Lean Gap Analysis®
Essential phase to measure and analyze current processes and define gaps between the current and desired state. In this first phase, one goes to "take a picture" of the current state of the processes in terms of quantifying waste, identifying any issues and opportunities for improvement, and timing all steps. Having a clear view of the performance of the process is necessary to identify the most correct countermeasures aimed at removing the root cause of the problem and to design, with a view to the future, the activities to be done - and on which KPIs to measure - to make it efficient.
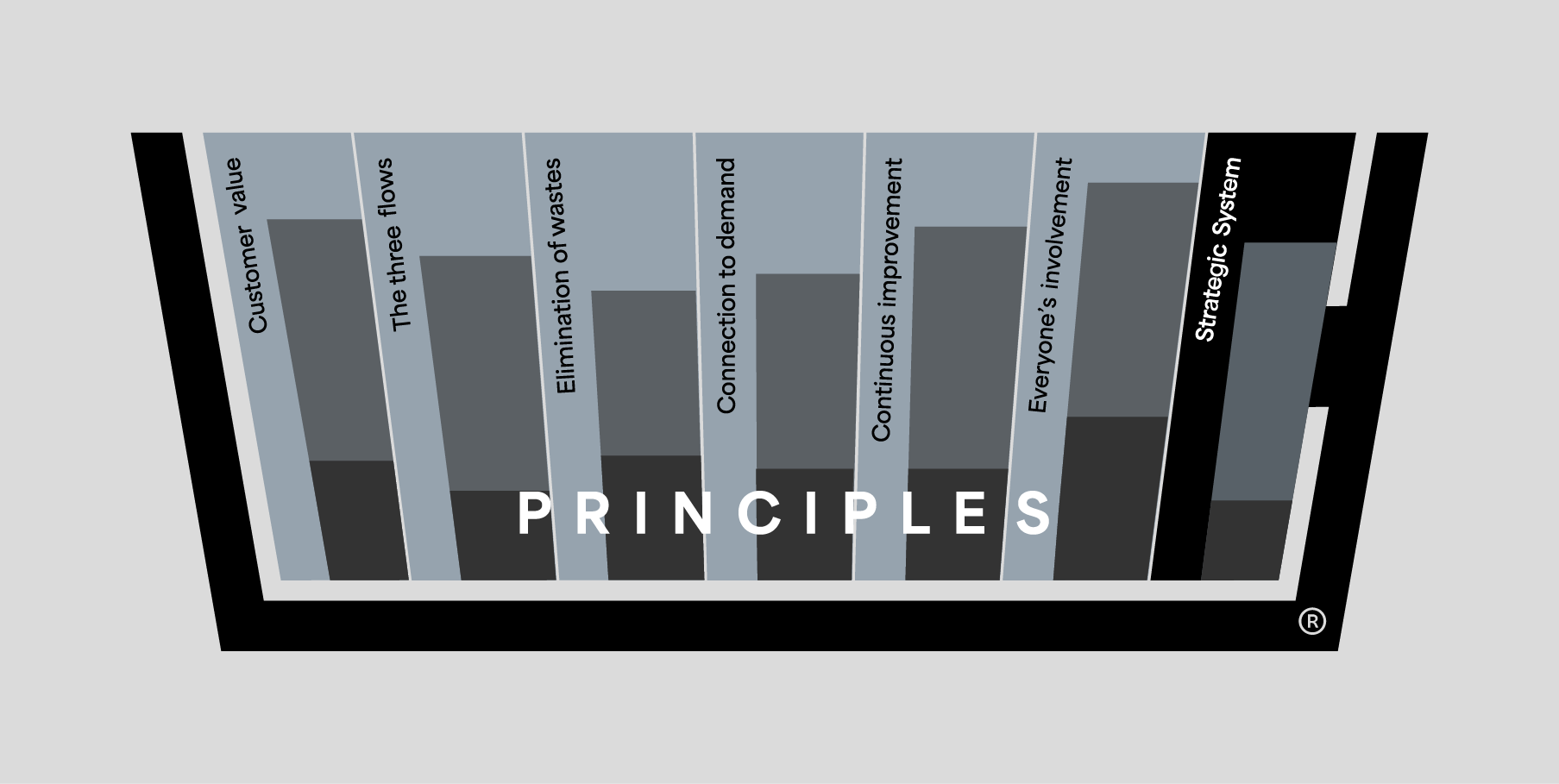
Complex processes with a high number of NVA activities.
Non-customer-value activities--such as waiting and unnecessary material handling--present in the line caused an imbalance in the production line.
Nonlinear production line layout
The nonlinearity of the line layout generated inefficiencies in production.
Material in the work area
Excessive presence of unneeded material generated inefficiencies due to the dilated time to search for it.
Point-in-time view of efficiencies
The focus was initially on the efficiencyization of the individual operation but not on the entire value stream.
Uniform production procedure for different products
"Standard" and "custom" machines followed the same production procedure with undefined and long production times.
PLAN
Lean RoadMap® in Delivery
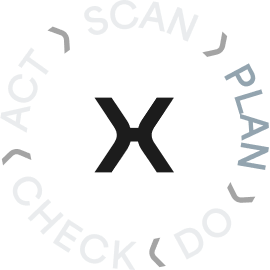
These were the starting points underlying the next phase of the project, namely the PLAN phase. Through the Lean RoadMap® we defined the sequence of implementation of the most correct lean techniques that would allow us to achieve the goals agreed upon with the Energreen team.
Lean RoadMap®
Stage in which the future state of the analyzed process is planned from a multi-scenario perspective. Once the most technically and economically correct scenario is chosen, we move on to planning the path to be taken to achieve it. In the Lean RoadMap® emerge the activities to focus on and the timeframe with which to complete them.
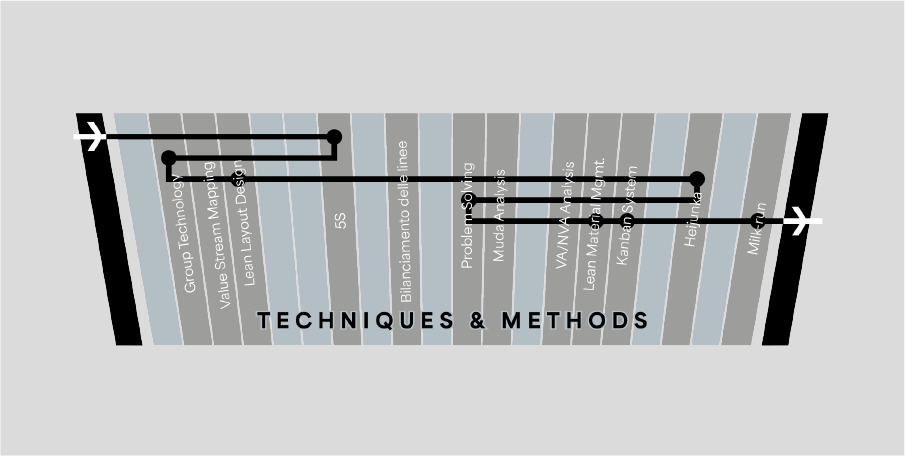
The direction to go
With the aim of reorganizing the different organizational models to better plan the production process, we reorganized the products in the following way:
-
Make to Stock - machines already ready when the order arrives.
-
Make to Order - material in stock already available to put the order into production.
-
Purchase to Order - material must be purchased in order to produce the machine.
-
Engineer to Order - when the order arrives the machine must be designed before production can begin.
Redesign of logistics-production flow.
In accordance with the reduction of NVA activities.
Design of a new layout
Redesign of the main line flow with attached production plugs for booths, arms and motors.
Application of the 5S technique.
Space reorganization technique to eliminate NVA activities.
Redesigning the warehouse and slaving.
Introducing the use of a milkrun with fixed cadence.
DO
Delivery Overall Transformation
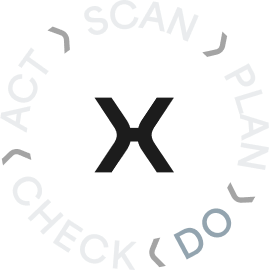
What lean activities and techniques enabled us to achieve the set goal?
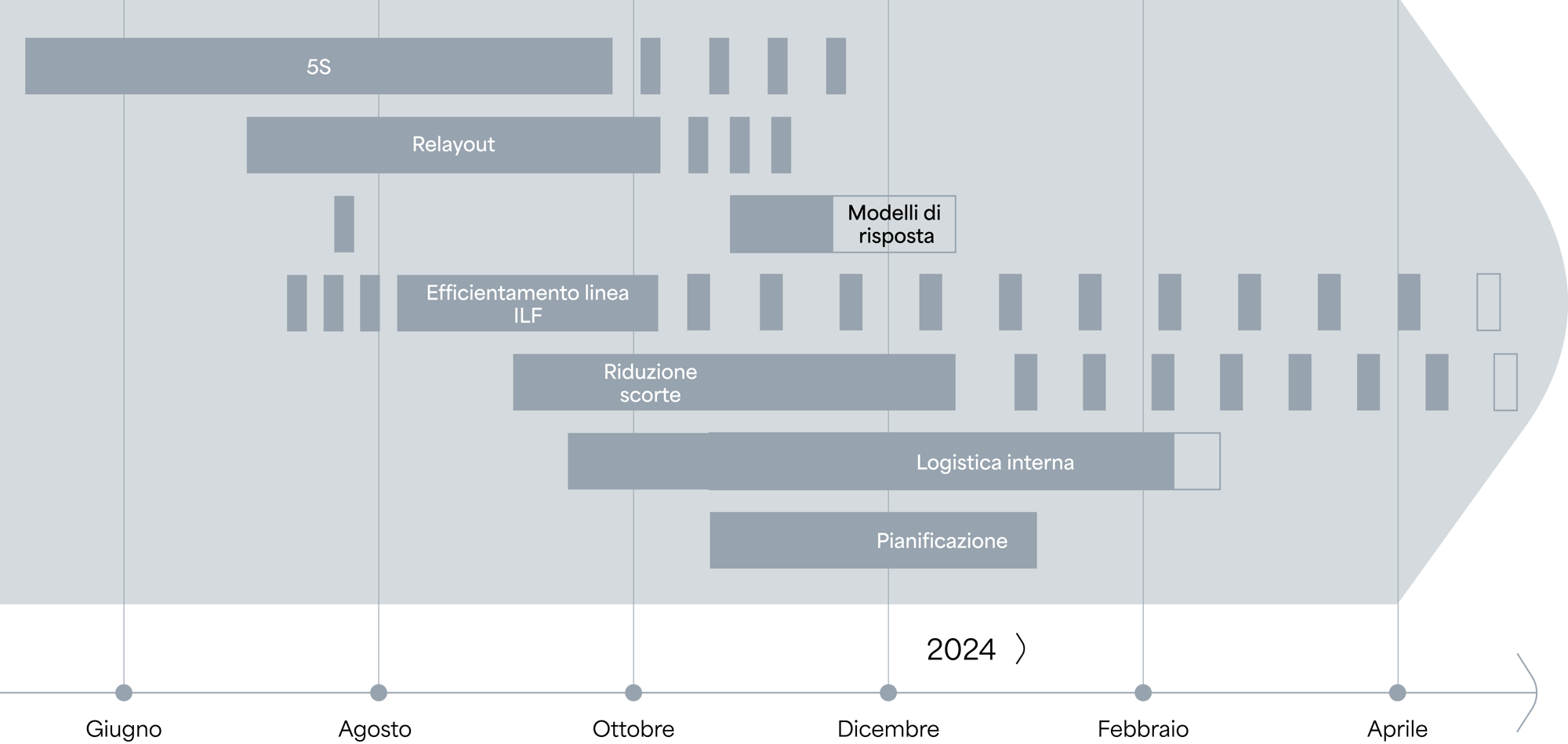
Lean layout of production and warehouse
The line stations were revised to realize the layout designed in the Plan phase through the application of the Spaghetti Chart technique.
5S
To reorganize and clean the workspace on all production line workstations, plugs attached, with the goal of reducing some of the NVAs of type 2 that could be eliminated in the short term. Specifically, we focused on those that involved unnecessary movement of operators and prolonged time searching for material. About 40 people were trained for a total of about 10 hours of training and 5 pilot sites opened.
Slave pull
The production process has been transformed starting with the way the line is enslaved: it has shifted from "batch" to "one-piece-flow" production by linking actual line consumption to material picking. Initially, material picking involved picking several machines together while today it is done by picking one machine at a time.
Through the implementation of milkrun (every four hours) in the line now there is now always only what is needed for the machines actually being processed at that time. The implemented system replenishes high-rotating, low-value, low-volume material. In addition, to balance the production line, processing steps were redefined in order to distribute activities so that different machines would balance each other.
Heijunka implementation.
Tool used to plan the line in "mixed-model" mode by allowing different machines to be worked on sequentially and no longer in product family groups.
Application of Problem Solving for Process Efficiency.
Technique apllicated during relayout and line balancing to investigate the root cause of obstacles that emerged during process redesign and be able to effectively remove them.
CHECK
Have we achieved the goals set?
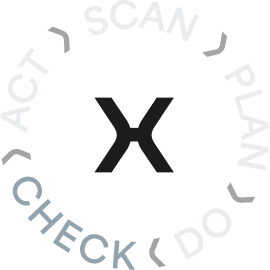
The application of the 5S technique--on all line stations, plugs attached--has enabled a complete reorganization of the area, which now appears much neater, cleaner and more functional.
The production line has been completely redesigned with a view to subservience and one-piece-flow planning compared with the previous weekly batch management.
The revised layout has improved-as well as the daily work of the team-the entire balance of the line by making production more efficient.
The line has been stabilized by aligning purchases with consumption.
Productivity efficiency increased by 18 percent, calculated as daily output per person-a goal achieved ahead of the end of the project.
The warehouse-to-turnover ratio reached 21.9 percent - out of a target set at the beginning of the project of 24.1 percent.
The average crossing time showed a 20% reduction.
Market response time - elapsed between order entry and shipment date - decreased by 28%.
The benefits achieved positively influenced the team. The people, who made themselves immediately available by demonstrating a remarkable readiness for change, embraced the project with enthusiasm. It is people who bring results, and only by changing their behavior is it possible to succeed in transformation-this is the real difference between being lean and doing lean.
From the macro-process of Delivery to that of Development
The market in which Energreen operates is experiencing continuous evolution in terms of both the breadth and depth of the product range. This leads to numerous impacts on the production process that are often not considered during design.Product innovation is therefore a fundamental aspect for this reality. Consequently, being able to streamline development processes in terms of time and resources invested is going to be outlined as a primary need.
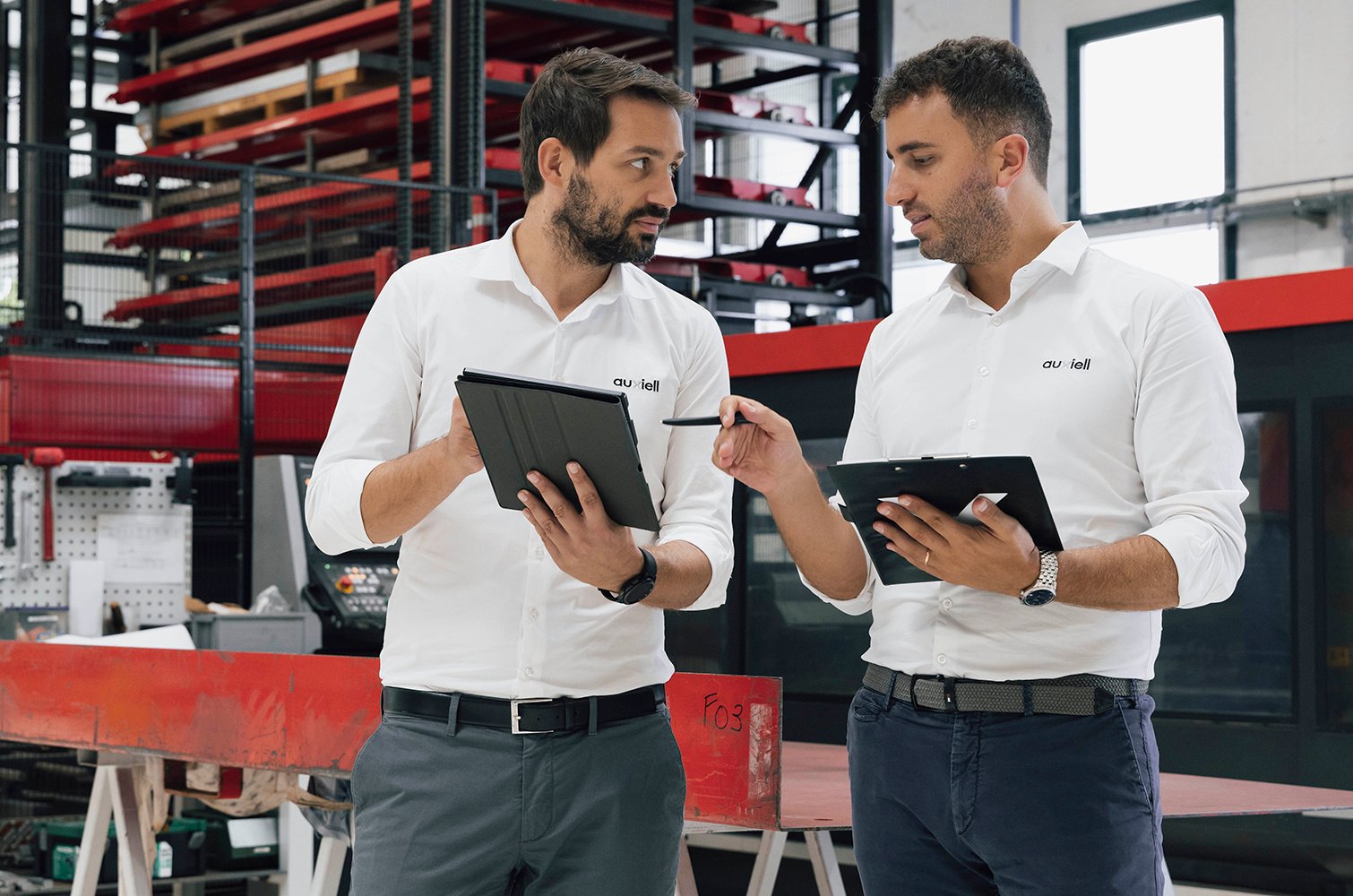
Our experts on hand to guide your business to transformation
Sign up for our newsletter and receive exclusive content, practical tips and news straight to your inbox!